What is Global Anodized Coating Market?
The Global Anodized Coating Market refers to the industry focused on the production and application of anodized coatings, which are protective and decorative finishes applied to metal surfaces, primarily aluminum. Anodizing is an electrochemical process that enhances the natural oxide layer on the surface of metals, making them more resistant to corrosion, wear, and tear. This market is driven by the increasing demand for durable and aesthetically pleasing metal products across various sectors, including automotive, aerospace, construction, and consumer electronics. The anodized coating not only improves the longevity and performance of metal components but also offers a wide range of color options, making it popular for both functional and decorative purposes. As industries continue to seek materials that offer both strength and visual appeal, the demand for anodized coatings is expected to grow, with advancements in technology further expanding its applications and efficiency. The market is characterized by a diverse range of products and services, catering to the specific needs of different industries, and is supported by ongoing research and development efforts aimed at enhancing the properties and applications of anodized coatings.
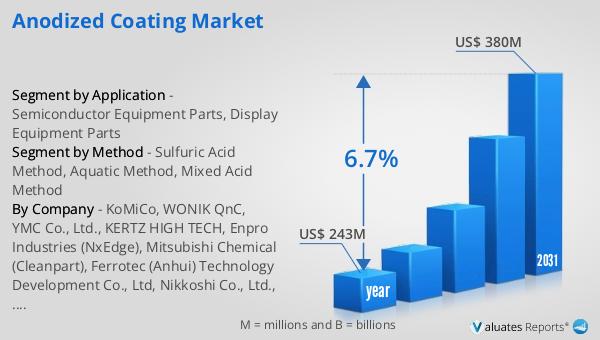
in the Global Anodized Coating Market:
The Global Anodized Coating Market offers a variety of types tailored to meet the diverse needs of its customers. One of the most common types is the sulfuric acid anodizing, which is widely used due to its cost-effectiveness and versatility. This type of anodizing creates a thick, durable oxide layer that provides excellent corrosion resistance and can be dyed in a wide range of colors, making it suitable for both industrial and decorative applications. Another popular type is hard anodizing, also known as hard coat anodizing, which produces a thicker and harder oxide layer. This type is particularly favored in industries where components are exposed to harsh conditions, such as in aerospace and automotive sectors, due to its superior wear resistance and durability. Chromic acid anodizing is another type, known for its thinner oxide layer, which is less abrasive and more flexible. This makes it ideal for applications where tight tolerances are required, such as in the aerospace industry. Additionally, there is the phosphoric acid anodizing, which is primarily used as a pre-treatment for adhesive bonding in aerospace applications. This type enhances the adhesion properties of the metal surface, ensuring strong and durable bonds. Each type of anodized coating offers unique benefits and is selected based on the specific requirements of the application, such as the desired level of corrosion resistance, wear resistance, and aesthetic appeal. The choice of anodizing type also depends on the material being coated, as different metals respond differently to the anodizing process. For instance, while aluminum is the most commonly anodized metal, other metals like titanium and magnesium can also be anodized, albeit with different processes and outcomes. The Global Anodized Coating Market continues to evolve, with ongoing research and development efforts aimed at improving the properties and applications of anodized coatings. Innovations in anodizing technology are leading to the development of new types of coatings that offer enhanced performance and sustainability. For example, eco-friendly anodizing processes are being developed to reduce the environmental impact of anodizing, while new dyeing techniques are expanding the color options available for anodized products. As industries continue to demand materials that offer both functionality and aesthetic appeal, the variety of anodized coatings available in the market is expected to grow, providing customers with more options to meet their specific needs.
Semiconductor Equipment Parts, Display Equipment Parts in the Global Anodized Coating Market:
In the realm of semiconductor equipment parts, anodized coatings play a crucial role in enhancing the performance and longevity of components. Semiconductor manufacturing involves processes that are highly sensitive to contamination and require materials that can withstand extreme conditions. Anodized coatings provide a protective barrier that prevents corrosion and wear, ensuring the reliability and durability of semiconductor equipment parts. The non-conductive nature of anodized coatings is particularly beneficial in semiconductor applications, as it prevents electrical interference and maintains the integrity of the components. Additionally, the smooth surface finish achieved through anodizing reduces the risk of particle contamination, which is critical in maintaining the purity of semiconductor wafers. In display equipment parts, anodized coatings are used to enhance both the functional and aesthetic properties of components. The demand for high-quality displays in consumer electronics, such as smartphones, tablets, and televisions, has driven the need for materials that offer superior performance and visual appeal. Anodized coatings provide a durable and attractive finish that enhances the appearance of display equipment parts, while also offering protection against scratches, corrosion, and wear. The ability to dye anodized coatings in a wide range of colors allows manufacturers to create visually appealing products that meet the aesthetic preferences of consumers. Furthermore, the lightweight nature of anodized aluminum makes it an ideal choice for display equipment parts, as it contributes to the overall reduction in weight of electronic devices. The use of anodized coatings in semiconductor and display equipment parts is supported by ongoing advancements in anodizing technology, which are leading to the development of coatings with enhanced properties and performance. For instance, new anodizing processes are being developed to improve the thermal conductivity of anodized coatings, which is particularly beneficial in semiconductor applications where heat dissipation is critical. Similarly, innovations in dyeing techniques are expanding the color options available for anodized coatings, allowing manufacturers to create products that stand out in the competitive consumer electronics market. As the demand for high-performance and aesthetically pleasing electronic devices continues to grow, the use of anodized coatings in semiconductor and display equipment parts is expected to increase, driving further advancements in anodizing technology and expanding the applications of anodized coatings in these industries.
Global Anodized Coating Market Outlook:
The global market for anodized coatings was valued at $243 million in 2024 and is anticipated to expand to a revised size of $380 million by 2031, reflecting a compound annual growth rate (CAGR) of 6.7% over the forecast period. This growth trajectory underscores the increasing demand for anodized coatings across various industries, driven by their superior protective and aesthetic properties. The rising adoption of anodized coatings in sectors such as automotive, aerospace, construction, and consumer electronics is a key factor contributing to this market expansion. As industries continue to seek materials that offer both durability and visual appeal, the demand for anodized coatings is expected to grow. The market's growth is also supported by ongoing advancements in anodizing technology, which are leading to the development of coatings with enhanced performance and sustainability. Innovations in eco-friendly anodizing processes and new dyeing techniques are expanding the applications and color options available for anodized products, further driving market growth. As the global market for anodized coatings continues to evolve, it presents significant opportunities for manufacturers and suppliers to capitalize on the increasing demand for high-quality, durable, and aesthetically pleasing metal finishes.
Report Metric | Details |
Report Name | Anodized Coating Market |
Accounted market size in year | US$ 243 million |
Forecasted market size in 2031 | US$ 380 million |
CAGR | 6.7% |
Base Year | year |
Forecasted years | 2025 - 2031 |
Segment by Method |
|
Segment by Application |
|
By Region |
|
By Company | KoMiCo, WONIK QnC, YMC Co., Ltd., KERTZ HIGH TECH, Enpro Industries (NxEdge), Mitsubishi Chemical (Cleanpart), Ferrotec (Anhui) Technology Development Co., Ltd, Nikkoshi Co., Ltd., ULVAC TECHNO, Ltd., Aldon Group, FM INDUSTRIES, Semano, YKMC Inc |
Forecast units | USD million in value |
Report coverage | Revenue and volume forecast, company share, competitive landscape, growth factors and trends |