What is Global FDA Grade Thermoplastic Elastomers Market?
Global FDA Grade Thermoplastic Elastomers (TPEs) are a unique class of materials that combine the properties of rubber with the processing advantages of plastics. These materials are designed to meet the stringent requirements set by the U.S. Food and Drug Administration (FDA) for safety and performance, making them suitable for applications that involve direct contact with food, medical devices, and other sensitive uses. TPEs are known for their flexibility, durability, and resistance to various environmental factors, which makes them highly versatile. They can be molded, extruded, or cast into a variety of shapes and forms, providing manufacturers with a wide range of design possibilities. The global market for FDA Grade TPEs is driven by the increasing demand for safe and reliable materials in industries such as healthcare, food packaging, and consumer goods. As these industries continue to grow, the need for high-quality, FDA-compliant materials is expected to rise, further fueling the expansion of the TPE market. The adaptability and performance of these materials make them an essential component in the development of innovative products that meet the evolving needs of consumers and regulatory standards.
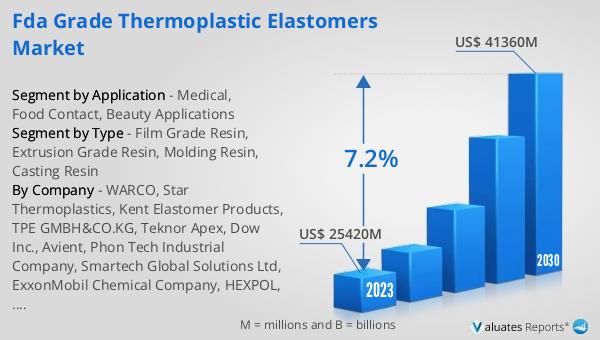
Film Grade Resin, Extrusion Grade Resin, Molding Resin, Casting Resin in the Global FDA Grade Thermoplastic Elastomers Market:
Film Grade Resin, Extrusion Grade Resin, Molding Resin, and Casting Resin are all integral components of the Global FDA Grade Thermoplastic Elastomers Market, each serving distinct purposes and applications. Film Grade Resin is primarily used in the production of thin, flexible films that are often employed in packaging applications. These films are valued for their clarity, strength, and ability to form a barrier against moisture and gases, making them ideal for food packaging and medical applications where hygiene and product integrity are paramount. The flexibility of Film Grade Resin allows it to be used in a variety of packaging formats, from simple wraps to complex multi-layered structures that provide enhanced protection and shelf life for perishable goods. Extrusion Grade Resin, on the other hand, is designed for processes that involve forcing the material through a shaped die to create continuous profiles, such as tubes, pipes, and sheets. This type of resin is particularly useful in the medical industry, where it is used to produce tubing for fluid transfer, catheters, and other medical devices that require precise dimensions and consistent quality. The ability of Extrusion Grade Resin to maintain its properties under various conditions makes it a reliable choice for applications that demand high performance and safety. Molding Resin is used in injection molding processes to create complex, three-dimensional shapes with high precision and repeatability. This type of resin is essential for manufacturing components that require intricate designs and tight tolerances, such as medical device housings, consumer electronics, and automotive parts. The versatility of Molding Resin allows manufacturers to produce parts with varying levels of hardness, flexibility, and color, enabling them to meet specific application requirements. Casting Resin, meanwhile, is used in processes where the material is poured into a mold and allowed to set, creating solid objects with detailed features. This type of resin is often used in applications that require high clarity and a smooth finish, such as lenses, decorative items, and prototypes. The ability of Casting Resin to replicate fine details makes it a popular choice for applications that demand aesthetic appeal and precision. Each of these resins plays a crucial role in the Global FDA Grade Thermoplastic Elastomers Market, providing manufacturers with the materials they need to create innovative products that meet the highest standards of safety and performance.
Medical, Food Contact, Beauty Applications in the Global FDA Grade Thermoplastic Elastomers Market:
The usage of Global FDA Grade Thermoplastic Elastomers in medical, food contact, and beauty applications highlights their versatility and importance in various industries. In the medical field, TPEs are used to manufacture a wide range of products, including medical tubing, catheters, syringe components, and seals. Their biocompatibility, flexibility, and resistance to sterilization processes make them ideal for medical applications where safety and reliability are critical. TPEs can be easily molded into complex shapes, allowing for the production of intricate medical devices that meet stringent regulatory requirements. In food contact applications, FDA Grade TPEs are used to produce items such as food storage containers, seals, gaskets, and flexible packaging films. These materials are designed to be non-toxic and resistant to oils, fats, and other food substances, ensuring that they do not contaminate the food they come into contact with. The ability of TPEs to maintain their properties over a wide temperature range makes them suitable for both hot and cold food applications, providing consumers with safe and reliable food storage solutions. In the beauty industry, TPEs are used in the production of personal care products such as toothbrushes, cosmetic applicators, and packaging components. Their soft touch and flexibility make them comfortable to use, while their resistance to chemicals and oils ensures that they maintain their appearance and functionality over time. The use of FDA Grade TPEs in beauty applications underscores the importance of safety and performance in products that come into direct contact with the skin. Overall, the use of Global FDA Grade Thermoplastic Elastomers in these areas demonstrates their ability to meet the diverse needs of different industries, providing manufacturers with the materials they need to create safe, effective, and innovative products.
Global FDA Grade Thermoplastic Elastomers Market Outlook:
The global market for FDA Grade Thermoplastic Elastomers was valued at approximately $29,020 million in 2024. This market is anticipated to expand significantly, reaching an estimated size of $46,890 million by the year 2031. This growth trajectory represents a compound annual growth rate (CAGR) of 7.2% over the forecast period. This upward trend is indicative of the increasing demand for high-quality, FDA-compliant materials across various industries. The versatility and adaptability of thermoplastic elastomers make them a preferred choice for manufacturers looking to develop products that meet stringent safety and performance standards. As industries such as healthcare, food packaging, and consumer goods continue to evolve, the need for reliable and innovative materials is expected to drive the expansion of the TPE market. The projected growth of this market highlights the importance of FDA Grade Thermoplastic Elastomers in the development of products that cater to the changing needs of consumers and regulatory requirements. This market outlook underscores the potential for continued innovation and advancement in the field of thermoplastic elastomers, as manufacturers seek to capitalize on the growing demand for safe and effective materials.
Report Metric | Details |
Report Name | FDA Grade Thermoplastic Elastomers Market |
Accounted market size in year | US$ 29020 million |
Forecasted market size in 2031 | US$ 46890 million |
CAGR | 7.2% |
Base Year | year |
Forecasted years | 2025 - 2031 |
by Type |
|
by Application |
|
Production by Region |
|
Consumption by Region |
|
By Company | WARCO, Star Thermoplastics, Kent Elastomer Products, TPE GMBH&CO.KG, Teknor Apex, Dow Inc., Avient, Phon Tech Industrial Company, Smartech Global Solutions Ltd, ExxonMobil Chemical Company, HEXPOL, Elastron, LCY GROUP, Mitsui Chemicals, FM plastics, Miller Waste Mills,Inc., Alphagary, Celanese, Zeon Chemicals, Zylog ElastoComp, Kin Join Co.,Ltd, Prime Technic Group |
Forecast units | USD million in value |
Report coverage | Revenue and volume forecast, company share, competitive landscape, growth factors and trends |