What is Global Aluminum Foam for Automotive Market?
The Global Aluminum Foam for Automotive Market is a specialized segment within the broader automotive materials industry, focusing on the use of aluminum foam in vehicle manufacturing. Aluminum foam is a lightweight, porous material that offers a unique combination of properties, making it highly suitable for automotive applications. It is produced by injecting gas into molten aluminum, creating a foam-like structure with numerous small, closed or open cells. This material is prized for its excellent strength-to-weight ratio, energy absorption capabilities, and thermal and acoustic insulation properties. In the automotive sector, aluminum foam is increasingly being used to enhance vehicle performance, safety, and efficiency. Its lightweight nature contributes to reducing the overall weight of vehicles, which in turn improves fuel efficiency and reduces emissions. Additionally, aluminum foam's ability to absorb impact energy makes it an ideal choice for crash protection components, while its thermal and acoustic insulation properties are beneficial for improving passenger comfort. As the automotive industry continues to prioritize sustainability and performance, the demand for innovative materials like aluminum foam is expected to grow, driving advancements and adoption in this niche market.
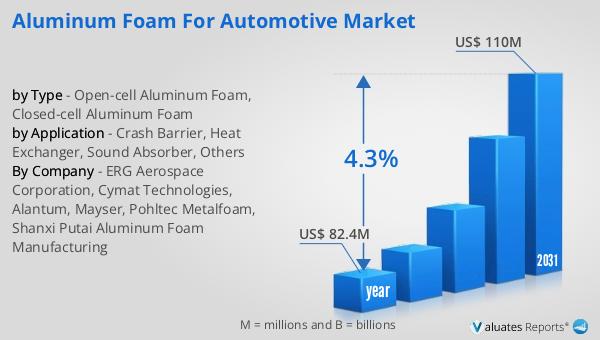
Open-cell Aluminum Foam, Closed-cell Aluminum Foam in the Global Aluminum Foam for Automotive Market:
Open-cell and closed-cell aluminum foams are two distinct types of materials used in the Global Aluminum Foam for Automotive Market, each offering unique properties and applications. Open-cell aluminum foam is characterized by its interconnected network of pores, which allows fluids and gases to pass through. This type of foam is particularly valued for its excellent sound absorption and thermal management capabilities. In the automotive industry, open-cell aluminum foam is often used in applications where noise reduction and heat dissipation are critical, such as in engine compartments and exhaust systems. Its porous structure also makes it suitable for use in filters and catalytic converters, where it can facilitate the flow of gases while trapping particulates. On the other hand, closed-cell aluminum foam consists of discrete, sealed cells that do not allow the passage of fluids or gases. This type of foam is known for its superior strength and energy absorption properties, making it ideal for structural and safety applications in vehicles. Closed-cell aluminum foam is commonly used in crash protection components, such as bumpers and side-impact beams, where its ability to absorb impact energy can significantly enhance passenger safety. Additionally, its lightweight nature contributes to overall vehicle weight reduction, improving fuel efficiency and reducing emissions. Both open-cell and closed-cell aluminum foams offer distinct advantages in the automotive sector, and their selection depends on the specific requirements of the application. For instance, while open-cell foam is preferred for applications requiring sound and thermal management, closed-cell foam is chosen for its structural integrity and impact resistance. The versatility of aluminum foam, combined with its unique properties, makes it an attractive material for automotive manufacturers seeking to improve vehicle performance, safety, and efficiency. The growing emphasis on sustainability and environmental responsibility in the automotive industry is also driving the adoption of aluminum foam. As automakers strive to meet stringent emissions regulations and improve fuel economy, the lightweight nature of aluminum foam becomes increasingly valuable. By reducing the overall weight of vehicles, aluminum foam helps to enhance fuel efficiency and lower emissions, contributing to a more sustainable automotive industry. Furthermore, advancements in manufacturing technologies are enabling the production of aluminum foam with improved properties and at lower costs, making it more accessible to a wider range of automotive applications. As research and development efforts continue to focus on optimizing the performance and cost-effectiveness of aluminum foam, its adoption in the automotive sector is expected to expand. In conclusion, open-cell and closed-cell aluminum foams are integral components of the Global Aluminum Foam for Automotive Market, each offering unique benefits that cater to different automotive applications. Their ability to enhance vehicle performance, safety, and efficiency, combined with their contribution to sustainability, positions aluminum foam as a key material in the future of automotive manufacturing.
Crash Barrier, Heat Exchanger, Sound Absorber, Others in the Global Aluminum Foam for Automotive Market:
The Global Aluminum Foam for Automotive Market finds its usage in various areas, including crash barriers, heat exchangers, sound absorbers, and other applications, each leveraging the unique properties of aluminum foam to enhance vehicle performance and safety. In the realm of crash barriers, aluminum foam is highly valued for its exceptional energy absorption capabilities. When used in crash protection components such as bumpers and side-impact beams, aluminum foam can effectively absorb and dissipate impact energy, reducing the force transmitted to vehicle occupants and thereby enhancing passenger safety. Its lightweight nature also contributes to overall vehicle weight reduction, which is crucial for improving fuel efficiency and reducing emissions. In heat exchangers, aluminum foam's high thermal conductivity and large surface area make it an ideal material for efficient heat transfer. The open-cell structure of aluminum foam allows for the rapid dissipation of heat, making it suitable for use in engine cooling systems and other thermal management applications. By improving heat exchange efficiency, aluminum foam helps to maintain optimal operating temperatures, enhancing vehicle performance and reliability. Sound absorption is another critical area where aluminum foam is utilized in the automotive industry. The porous structure of open-cell aluminum foam makes it highly effective at absorbing sound waves, reducing noise levels within the vehicle cabin. This property is particularly beneficial in enhancing passenger comfort by minimizing engine noise, road noise, and vibrations. As automakers continue to prioritize the development of quieter and more comfortable vehicles, the demand for sound-absorbing materials like aluminum foam is expected to grow. Beyond these specific applications, aluminum foam is also used in various other automotive components where its unique properties can be leveraged. For instance, its lightweight and corrosion-resistant nature make it suitable for use in body panels and structural components, contributing to overall vehicle weight reduction and durability. Additionally, aluminum foam's ability to withstand high temperatures and harsh environments makes it an attractive choice for components exposed to extreme conditions. The versatility of aluminum foam, combined with its ability to enhance vehicle performance, safety, and efficiency, makes it a valuable material in the automotive industry. As automakers continue to seek innovative solutions to meet evolving consumer demands and regulatory requirements, the adoption of aluminum foam in various automotive applications is expected to increase. This trend is further supported by ongoing advancements in manufacturing technologies, which are enabling the production of aluminum foam with improved properties and at lower costs. In summary, the Global Aluminum Foam for Automotive Market plays a crucial role in enhancing vehicle performance and safety across various applications, including crash barriers, heat exchangers, sound absorbers, and more. Its unique combination of properties, such as lightweight, energy absorption, thermal conductivity, and sound absorption, makes it an attractive material for automotive manufacturers seeking to improve vehicle efficiency, safety, and comfort. As the automotive industry continues to evolve, the demand for innovative materials like aluminum foam is expected to grow, driving further advancements and adoption in this niche market.
Global Aluminum Foam for Automotive Market Outlook:
In 2024, the global market for Aluminum Foam for Automotive was valued at approximately $82.4 million. This market is anticipated to experience growth, reaching an estimated size of $110 million by 2031. This growth trajectory represents a compound annual growth rate (CAGR) of 4.3% over the forecast period. The increasing demand for lightweight and efficient materials in the automotive industry is a key driver of this growth. Aluminum foam, with its unique properties such as lightweight, energy absorption, and thermal and acoustic insulation, is becoming an increasingly popular choice for automotive manufacturers. As the industry continues to prioritize sustainability and performance, the adoption of innovative materials like aluminum foam is expected to rise. This growth is further supported by advancements in manufacturing technologies, which are enabling the production of aluminum foam with improved properties and at lower costs. As a result, the Global Aluminum Foam for Automotive Market is poised for significant expansion in the coming years, driven by the increasing demand for lightweight and efficient materials in the automotive industry.
Report Metric | Details |
Report Name | Aluminum Foam for Automotive Market |
Accounted market size in year | US$ 82.4 million |
Forecasted market size in 2031 | US$ 110 million |
CAGR | 4.3% |
Base Year | year |
Forecasted years | 2025 - 2031 |
by Type |
|
by Application |
|
Production by Region |
|
Consumption by Region |
|
By Company | ERG Aerospace Corporation, Cymat Technologies, Alantum, Mayser, Pohltec Metalfoam, Shanxi Putai Aluminum Foam Manufacturing |
Forecast units | USD million in value |
Report coverage | Revenue and volume forecast, company share, competitive landscape, growth factors and trends |