What is Global Heat Cure Silicone Conformal Coating Market?
The Global Heat Cure Silicone Conformal Coating Market is a specialized segment within the broader coatings industry, focusing on the use of silicone-based materials to protect electronic components and assemblies. These coatings are applied to printed circuit boards (PCBs) and other electronic components to shield them from environmental factors such as moisture, dust, chemicals, and temperature extremes. The heat cure process involves applying the silicone coating and then curing it at elevated temperatures to form a durable, protective layer. This market is driven by the increasing demand for reliable and long-lasting electronic devices across various industries, including consumer electronics, automotive, aerospace, and industrial applications. The unique properties of silicone, such as its flexibility, thermal stability, and resistance to harsh environments, make it an ideal choice for conformal coatings. As technology advances and the need for miniaturization and enhanced performance of electronic devices grows, the demand for heat cure silicone conformal coatings is expected to rise, offering significant opportunities for manufacturers and suppliers in this market.
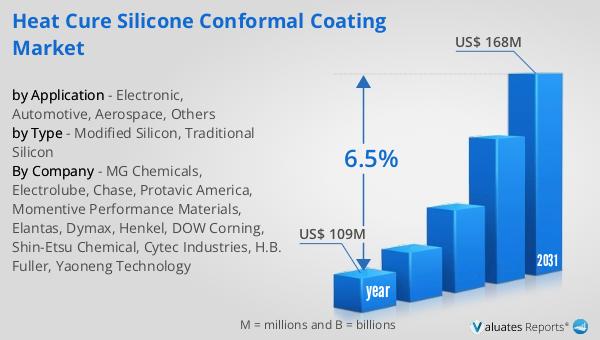
Modified Silicon, Traditional Silicon in the Global Heat Cure Silicone Conformal Coating Market:
In the realm of Global Heat Cure Silicone Conformal Coating Market, Modified Silicon and Traditional Silicon represent two distinct approaches to silicone-based coatings, each with its own set of characteristics and applications. Traditional Silicon coatings are primarily composed of unmodified silicone polymers, which are known for their excellent thermal stability, flexibility, and resistance to environmental factors. These coatings are widely used in applications where basic protection against moisture, dust, and chemicals is required. Traditional Silicon coatings are relatively easy to apply and cure, making them a popular choice for many standard electronic applications. However, they may have limitations in terms of adhesion to certain substrates and may not offer the enhanced performance characteristics required for more demanding applications. On the other hand, Modified Silicon coatings are engineered to enhance the properties of traditional silicone by incorporating additional chemical modifications or additives. These modifications can improve adhesion, increase resistance to specific chemicals, or enhance mechanical properties such as hardness and abrasion resistance. Modified Silicon coatings are often used in applications where traditional silicone coatings may fall short, such as in high-performance automotive or aerospace environments where components are exposed to extreme conditions. The ability to tailor the properties of Modified Silicon coatings makes them highly versatile and suitable for a wide range of applications. One of the key advantages of Modified Silicon coatings is their ability to adhere to a variety of substrates, including metals, plastics, and glass. This makes them ideal for use in complex electronic assemblies where multiple materials are present. Additionally, Modified Silicon coatings can be formulated to provide specific levels of electrical insulation or conductivity, depending on the requirements of the application. This versatility allows manufacturers to customize coatings to meet the precise needs of their products, ensuring optimal performance and reliability. In terms of environmental resistance, Modified Silicon coatings often outperform their traditional counterparts. They can be designed to withstand exposure to harsh chemicals, UV radiation, and extreme temperatures, making them suitable for use in challenging environments such as automotive engine compartments or aerospace applications. The enhanced durability of Modified Silicon coatings also contributes to the longevity of electronic components, reducing the need for frequent maintenance or replacement. Despite their advantages, Modified Silicon coatings can be more complex and costly to produce than Traditional Silicon coatings. The additional chemical modifications and formulation processes required to achieve the desired properties can increase production costs, which may be a consideration for manufacturers when selecting a coating solution. However, the benefits of enhanced performance and reliability often outweigh the additional costs, particularly in high-value applications where component failure is not an option. In conclusion, both Modified Silicon and Traditional Silicon coatings play important roles in the Global Heat Cure Silicone Conformal Coating Market. While Traditional Silicon coatings offer a reliable and cost-effective solution for many standard applications, Modified Silicon coatings provide the enhanced performance and versatility needed for more demanding environments. As technology continues to evolve and the requirements for electronic components become more stringent, the demand for both types of coatings is expected to grow, offering opportunities for innovation and development within the market.
Electronic, Automotive, Aerospace, Others in the Global Heat Cure Silicone Conformal Coating Market:
The Global Heat Cure Silicone Conformal Coating Market finds extensive usage across various industries, including electronics, automotive, aerospace, and others, due to its unique protective properties. In the electronics industry, these coatings are primarily used to protect printed circuit boards (PCBs) and other sensitive components from environmental factors such as moisture, dust, and chemicals. The application of silicone conformal coatings ensures the longevity and reliability of electronic devices, which is crucial in consumer electronics, industrial equipment, and telecommunications. The flexibility and thermal stability of silicone coatings make them ideal for use in devices that are subject to temperature fluctuations and mechanical stress. In the automotive industry, heat cure silicone conformal coatings are used to protect electronic components in vehicles, such as engine control units, sensors, and infotainment systems. The harsh operating conditions in automotive environments, including exposure to high temperatures, vibration, and chemicals, necessitate the use of robust protective coatings. Silicone conformal coatings provide the necessary protection to ensure the reliable operation of electronic systems, contributing to vehicle safety and performance. As the automotive industry continues to advance with the integration of more electronic systems and the development of electric and autonomous vehicles, the demand for high-performance conformal coatings is expected to increase. The aerospace industry also benefits significantly from the use of heat cure silicone conformal coatings. In aerospace applications, electronic components are exposed to extreme conditions, including high altitudes, temperature variations, and potential exposure to corrosive substances. Silicone conformal coatings offer the necessary protection to ensure the reliability and functionality of critical aerospace systems, such as avionics, navigation, and communication equipment. The ability of silicone coatings to withstand harsh environments and provide long-term protection makes them an essential component in the aerospace sector. Beyond electronics, automotive, and aerospace, heat cure silicone conformal coatings are used in various other industries where electronic components require protection from environmental factors. These industries include medical devices, where the reliability and safety of electronic components are paramount, and the industrial sector, where equipment is often exposed to harsh operating conditions. The versatility and protective properties of silicone conformal coatings make them suitable for a wide range of applications, ensuring the performance and longevity of electronic systems across different sectors. In summary, the Global Heat Cure Silicone Conformal Coating Market plays a vital role in protecting electronic components across multiple industries. The unique properties of silicone coatings, including their flexibility, thermal stability, and resistance to environmental factors, make them an ideal choice for applications in electronics, automotive, aerospace, and beyond. As technology continues to advance and the demand for reliable electronic systems grows, the importance of high-performance conformal coatings is expected to increase, driving further innovation and development in the market.
Global Heat Cure Silicone Conformal Coating Market Outlook:
The outlook for the Global Heat Cure Silicone Conformal Coating Market indicates a promising growth trajectory. In 2024, the market was valued at approximately US$ 109 million, reflecting the significant demand for these specialized coatings across various industries. By 2031, the market is projected to expand to a revised size of US$ 168 million, driven by a compound annual growth rate (CAGR) of 6.5% during the forecast period. This growth is attributed to the increasing need for reliable and durable protective coatings for electronic components, as industries such as electronics, automotive, and aerospace continue to evolve and integrate more advanced technologies. The rising adoption of electronic devices in everyday life, coupled with the growing complexity of electronic systems in vehicles and aircraft, is fueling the demand for high-performance conformal coatings. The ability of heat cure silicone coatings to provide superior protection against environmental factors, such as moisture, dust, and chemicals, makes them an essential component in ensuring the longevity and reliability of electronic systems. As manufacturers seek to enhance the performance and durability of their products, the demand for advanced coating solutions is expected to rise, contributing to the market's growth. Furthermore, the trend towards miniaturization and increased functionality of electronic devices is driving the need for coatings that can provide effective protection without compromising performance. Heat cure silicone conformal coatings offer the necessary flexibility and thermal stability to meet these requirements, making them a preferred choice for manufacturers across various industries. As the market continues to expand, opportunities for innovation and development in coating technologies are expected to emerge, further enhancing the capabilities and applications of silicone conformal coatings. In conclusion, the Global Heat Cure Silicone Conformal Coating Market is poised for significant growth in the coming years, driven by the increasing demand for reliable and durable protective coatings for electronic components. The market's expansion is supported by advancements in technology and the growing complexity of electronic systems across various industries. As manufacturers continue to seek high-performance coating solutions, the market is expected to offer numerous opportunities for innovation and development, ensuring the continued evolution and success of silicone conformal coatings.
Report Metric | Details |
Report Name | Heat Cure Silicone Conformal Coating Market |
Accounted market size in year | US$ 109 million |
Forecasted market size in 2031 | US$ 168 million |
CAGR | 6.5% |
Base Year | year |
Forecasted years | 2025 - 2031 |
by Type |
|
by Application |
|
Production by Region |
|
Consumption by Region |
|
By Company | MG Chemicals, Electrolube, Chase, Protavic America, Momentive Performance Materials, Elantas, Dymax, Henkel, DOW Corning, Shin-Etsu Chemical, Cytec Industries, H.B. Fuller, Yaoneng Technology |
Forecast units | USD million in value |
Report coverage | Revenue and volume forecast, company share, competitive landscape, growth factors and trends |