What is Global Wafer Vacuum End Effector Market?
The Global Wafer Vacuum End Effector Market is a specialized segment within the semiconductor industry that focuses on the development and distribution of vacuum end effectors used in wafer handling processes. These end effectors are critical components in semiconductor manufacturing, as they are responsible for the precise and contamination-free handling of wafers during various stages of production. The market encompasses a range of products designed to cater to different wafer sizes and materials, ensuring high efficiency and reliability in wafer transfer operations. The demand for wafer vacuum end effectors is driven by the increasing complexity of semiconductor devices and the need for advanced automation solutions in manufacturing processes. As the semiconductor industry continues to evolve, the Global Wafer Vacuum End Effector Market is expected to grow, driven by technological advancements and the rising demand for high-performance semiconductor devices.
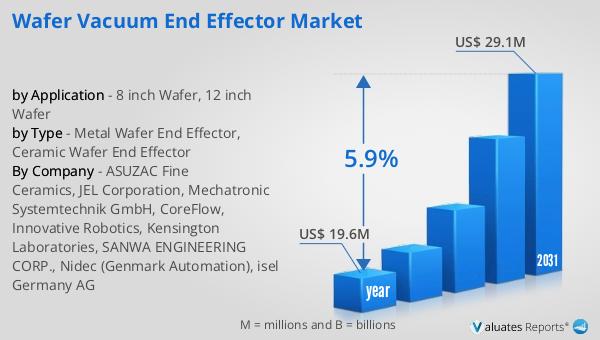
Metal Wafer End Effector, Ceramic Wafer End Effector in the Global Wafer Vacuum End Effector Market:
Metal Wafer End Effectors and Ceramic Wafer End Effectors are two primary types of end effectors used in the Global Wafer Vacuum End Effector Market. Metal Wafer End Effectors are typically made from materials such as stainless steel or aluminum, offering high strength and durability. These end effectors are designed to handle wafers with precision and are often used in environments where mechanical robustness is crucial. Metal end effectors are known for their ability to withstand harsh conditions and provide reliable performance over extended periods. On the other hand, Ceramic Wafer End Effectors are made from advanced ceramic materials, which offer superior thermal and chemical resistance. These end effectors are ideal for applications where high purity and minimal contamination are essential. Ceramic end effectors are often used in processes that involve high temperatures or aggressive chemicals, as they can maintain their integrity and performance under such conditions. Both types of end effectors play a vital role in ensuring the smooth and efficient handling of wafers in semiconductor manufacturing. The choice between metal and ceramic end effectors depends on the specific requirements of the application, including factors such as the operating environment, wafer material, and desired performance characteristics. As the semiconductor industry continues to advance, the demand for both metal and ceramic wafer end effectors is expected to grow, driven by the need for more sophisticated and reliable wafer handling solutions.
8 inch Wafer, 12 inch Wafer in the Global Wafer Vacuum End Effector Market:
The usage of Global Wafer Vacuum End Effectors in handling 8-inch and 12-inch wafers is crucial for the semiconductor manufacturing process. 8-inch wafers, also known as 200mm wafers, are commonly used in the production of various semiconductor devices, including microprocessors, memory chips, and sensors. The handling of these wafers requires precision and care to avoid contamination and damage. Vacuum end effectors designed for 8-inch wafers are equipped with features that ensure secure gripping and smooth transfer of the wafers between different stages of the manufacturing process. These end effectors are often used in automated systems that handle large volumes of wafers, ensuring high throughput and efficiency. Similarly, 12-inch wafers, or 300mm wafers, are used in the production of advanced semiconductor devices that require larger surface areas for more complex circuitry. The handling of 12-inch wafers presents additional challenges due to their larger size and increased fragility. Vacuum end effectors designed for 12-inch wafers are engineered to provide gentle yet secure handling, minimizing the risk of breakage and contamination. These end effectors are often integrated into advanced automation systems that facilitate the seamless transfer of wafers through various stages of production, including lithography, etching, and deposition. The use of vacuum end effectors in handling both 8-inch and 12-inch wafers is essential for maintaining the integrity and quality of the wafers, ensuring the production of high-performance semiconductor devices. As the demand for more advanced and miniaturized semiconductor devices continues to grow, the need for efficient and reliable wafer handling solutions, such as vacuum end effectors, is expected to increase.
Global Wafer Vacuum End Effector Market Outlook:
The global Wafer Vacuum End Effector market was valued at US$ 16 million in 2023 and is anticipated to reach US$ 26 million by 2030, witnessing a CAGR of 5.9% during the forecast period 2024-2030. This market outlook highlights the significant growth potential of the wafer vacuum end effector market, driven by the increasing demand for advanced semiconductor devices and the need for efficient wafer handling solutions. The projected growth rate indicates a steady increase in market value, reflecting the ongoing advancements in semiconductor manufacturing technologies and the rising adoption of automation in production processes. As the semiconductor industry continues to evolve, the demand for high-performance wafer vacuum end effectors is expected to rise, contributing to the overall growth of the market. The market outlook underscores the importance of innovation and technological advancements in driving the growth of the wafer vacuum end effector market, as manufacturers strive to develop more sophisticated and reliable solutions to meet the evolving needs of the semiconductor industry.
Report Metric | Details |
Report Name | Wafer Vacuum End Effector Market |
Accounted market size in 2023 | US$ 16 million |
Forecasted market size in 2030 | US$ 26 million |
CAGR | 5.9% |
Base Year | 2023 |
Forecasted years | 2024 - 2030 |
Segment by Type |
|
Segment by Application |
|
Production by Region |
|
Consumption by Region |
|
By Company | ASUZAC Fine Ceramics, JEL Corporation, Mechatronic Systemtechnik GmbH, CoreFlow, Innovative Robotics, Kensington Laboratories, SANWA ENGINEERING CORP., Nidec (Genmark Automation), isel Germany AG |
Forecast units | USD million in value |
Report coverage | Revenue and volume forecast, company share, competitive landscape, growth factors and trends |