What is Global Blocker Plate for Semiconductor Equipment Market?
The global Blocker Plate for Semiconductor Equipment market is a specialized segment within the semiconductor manufacturing industry. Blocker plates are critical components used in semiconductor equipment to control and direct the flow of gases and plasma during various manufacturing processes. These plates are essential for ensuring the precision and efficiency of processes such as Chemical Vapor Deposition (CVD), Physical Vapor Deposition (PVD), and etching. The market for these plates is driven by the increasing demand for semiconductors in various applications, including consumer electronics, automotive, and industrial sectors. As semiconductor technology advances, the need for high-quality and reliable blocker plates becomes even more crucial. The market is characterized by the presence of several key players who are continuously innovating to improve the performance and durability of these plates. The global market for blocker plates is expected to grow steadily, driven by the ongoing advancements in semiconductor manufacturing technologies and the increasing demand for high-performance semiconductor devices.
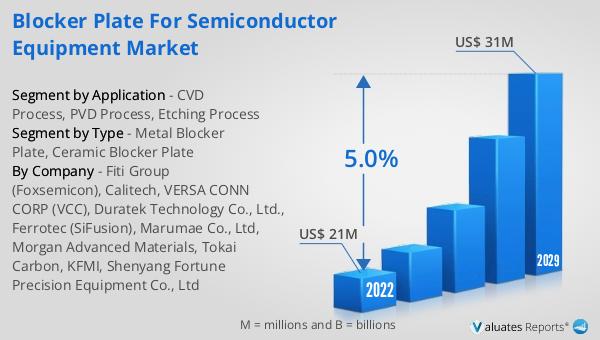
Metal Blocker Plate, Ceramic Blocker Plate in the Global Blocker Plate for Semiconductor Equipment Market:
Blocker plates used in semiconductor equipment can be broadly categorized into metal blocker plates and ceramic blocker plates. Metal blocker plates are typically made from materials such as stainless steel, aluminum, or other metal alloys. These plates are known for their durability, high thermal conductivity, and ability to withstand harsh processing environments. Metal blocker plates are often used in applications where high mechanical strength and thermal stability are required. They are also preferred in processes that involve high temperatures and aggressive chemicals, as they can resist corrosion and wear. On the other hand, ceramic blocker plates are made from advanced ceramic materials such as alumina, silicon carbide, or zirconia. These materials offer excellent thermal and electrical insulation properties, making them ideal for use in semiconductor manufacturing processes that require precise control of temperature and electrical characteristics. Ceramic blocker plates are also highly resistant to chemical attack and can maintain their structural integrity even under extreme conditions. They are often used in applications where high purity and minimal contamination are critical, such as in the production of high-performance semiconductor devices. Both metal and ceramic blocker plates play a vital role in ensuring the efficiency and reliability of semiconductor manufacturing processes. The choice between metal and ceramic blocker plates depends on the specific requirements of the application, including factors such as temperature, chemical environment, and mechanical stress. As the semiconductor industry continues to evolve, the demand for advanced blocker plates that can meet the stringent requirements of modern manufacturing processes is expected to grow.
CVD Process, PVD Process, Etching Process in the Global Blocker Plate for Semiconductor Equipment Market:
The usage of global blocker plates for semiconductor equipment is crucial in various manufacturing processes, including Chemical Vapor Deposition (CVD), Physical Vapor Deposition (PVD), and etching. In the CVD process, blocker plates are used to control the flow of precursor gases and ensure uniform deposition of thin films on the semiconductor wafers. The plates help in maintaining the desired temperature and pressure conditions within the reaction chamber, which is essential for achieving high-quality film deposition. In the PVD process, blocker plates play a similar role in controlling the flow of sputtering gases and plasma. They help in directing the plasma towards the target material, ensuring efficient sputtering and uniform deposition of thin films. The plates also protect the chamber walls and other components from being coated with unwanted material, thereby reducing maintenance requirements and improving process efficiency. In the etching process, blocker plates are used to control the flow of etching gases and plasma, ensuring precise removal of material from the semiconductor wafers. The plates help in maintaining the desired etching rate and selectivity, which is critical for achieving the required patterning and feature sizes on the wafers. Overall, the use of blocker plates in these processes is essential for ensuring the precision, efficiency, and reliability of semiconductor manufacturing.
Global Blocker Plate for Semiconductor Equipment Market Outlook:
The global Blocker Plate for Semiconductor Equipment market was valued at US$ 21 million in 2023 and is anticipated to reach US$ 31 million by 2030, witnessing a CAGR of 5.0% during the forecast period 2024-2030. According to SEMI, worldwide sales of semiconductor manufacturing equipment increased by 5% from $102.6 billion in 2021 to an all-time record of $107.6 billion in 2022. For the third consecutive year, China remained the largest semiconductor equipment market in 2022, despite a 5% slowdown in the pace of investments in the region year over year, accounting for $28.3 billion in billings.
Report Metric | Details |
Report Name | Blocker Plate for Semiconductor Equipment Market |
Accounted market size in 2023 | US$ 21 million |
Forecasted market size in 2030 | US$ 31 million |
CAGR | 5.0% |
Base Year | 2023 |
Forecasted years | 2024 - 2030 |
Segment by Type |
|
Segment by Application |
|
Production by Region |
|
Consumption by Region |
|
By Company | Fiti Group (Foxsemicon), Calitech, VERSA CONN CORP (VCC), Duratek Technology Co., Ltd., Ferrotec (SiFusion), Marumae Co., Ltd, Morgan Advanced Materials, Tokai Carbon, KFMI, Shenyang Fortune Precision Equipment Co., Ltd |
Forecast units | USD million in value |
Report coverage | Revenue and volume forecast, company share, competitive landscape, growth factors and trends |