What is Global Anti-corrosion Coating for Semiconductor Equipment Parts Market?
The global anti-corrosion coating for semiconductor equipment parts market is a specialized segment within the broader coatings industry. These coatings are essential for protecting semiconductor equipment parts from corrosion, which can significantly impact the performance and longevity of these high-precision devices. Semiconductor equipment operates in highly corrosive environments due to the use of various chemicals and gases during the manufacturing process. Anti-corrosion coatings help to extend the life of these parts, reduce maintenance costs, and improve overall efficiency. The market for these coatings is driven by the increasing demand for semiconductors in various applications, including consumer electronics, automotive, and industrial sectors. As technology advances, the need for more durable and reliable semiconductor equipment parts becomes even more critical, further fueling the demand for high-quality anti-corrosion coatings.
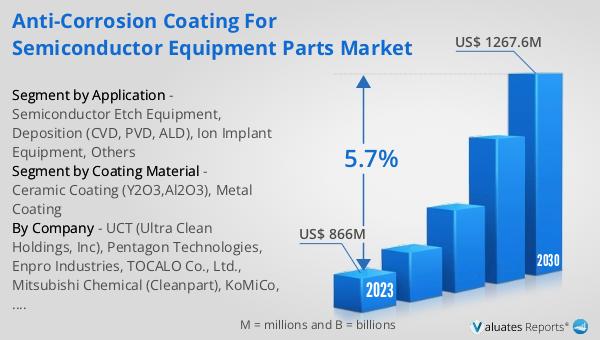
in the Global Anti-corrosion Coating for Semiconductor Equipment Parts Market:
The global anti-corrosion coating for semiconductor equipment parts market offers a variety of types to cater to the diverse needs of its customers. These coatings can be broadly categorized into several types based on their chemical composition and application methods. One of the most common types is epoxy coatings, known for their excellent adhesion, chemical resistance, and durability. Epoxy coatings are widely used in semiconductor equipment parts due to their ability to withstand harsh chemical environments. Another popular type is polyurethane coatings, which offer superior flexibility and abrasion resistance. These coatings are particularly useful in applications where parts are subjected to mechanical stress and wear. Fluoropolymer coatings, such as PTFE and PFA, are also extensively used in the semiconductor industry. These coatings provide exceptional chemical resistance and low friction properties, making them ideal for parts that come into contact with aggressive chemicals and gases. Additionally, ceramic coatings are gaining popularity due to their high-temperature resistance and excellent wear properties. These coatings are often used in high-temperature applications where other types of coatings may fail. Each type of coating has its unique advantages and is selected based on the specific requirements of the application. For instance, epoxy coatings are preferred for their strong adhesion and chemical resistance, while polyurethane coatings are chosen for their flexibility and abrasion resistance. Fluoropolymer coatings are selected for their exceptional chemical resistance and low friction properties, making them ideal for parts exposed to aggressive chemicals. Ceramic coatings are favored for their high-temperature resistance and wear properties, making them suitable for high-temperature applications. The choice of coating also depends on the application method. Some coatings are applied using spray techniques, while others are applied using dip or brush methods. The application method can impact the performance and durability of the coating, so it is essential to choose the right method for each type of coating. Overall, the global anti-corrosion coating for semiconductor equipment parts market offers a wide range of options to meet the diverse needs of its customers.
Semiconductor Etch Equipment, Deposition (CVD, PVD, ALD), Ion Implant Equipment, Others in the Global Anti-corrosion Coating for Semiconductor Equipment Parts Market:
The usage of global anti-corrosion coating for semiconductor equipment parts is crucial in various areas, including semiconductor etch equipment, deposition equipment (CVD, PVD, ALD), ion implant equipment, and others. In semiconductor etch equipment, anti-corrosion coatings play a vital role in protecting parts from the highly corrosive chemicals used in the etching process. These coatings help to extend the life of the equipment, reduce maintenance costs, and improve overall efficiency. In deposition equipment, such as Chemical Vapor Deposition (CVD), Physical Vapor Deposition (PVD), and Atomic Layer Deposition (ALD), anti-corrosion coatings are essential for protecting parts from the harsh chemical environments. These coatings help to ensure the reliability and performance of the equipment, which is critical for producing high-quality semiconductor devices. In ion implant equipment, anti-corrosion coatings are used to protect parts from the aggressive chemicals and gases used in the ion implantation process. These coatings help to extend the life of the equipment, reduce downtime, and improve overall productivity. Other areas where anti-corrosion coatings are used include cleaning and inspection equipment, where parts are exposed to various chemicals and gases. In these applications, anti-corrosion coatings help to protect the parts from corrosion, ensuring their longevity and performance. Overall, the usage of anti-corrosion coatings in semiconductor equipment parts is essential for maintaining the reliability and performance of the equipment, reducing maintenance costs, and improving overall efficiency.
Global Anti-corrosion Coating for Semiconductor Equipment Parts Market Outlook:
The global anti-corrosion coating for semiconductor equipment parts market was valued at US$ 866 million in 2023 and is anticipated to reach US$ 1267.6 million by 2030, witnessing a CAGR of 5.7% during the forecast period 2024-2030. According to SEMI, worldwide sales of semiconductor manufacturing equipment increased 5% from $102.6 billion in 2021 to an all-time record of $107.6 billion in 2022. For the third consecutive year, China remained the largest semiconductor equipment market in 2022, despite a 5% slowdown in the pace of investments in the region year over year, accounting for $28.3 billion in billings.
Report Metric | Details |
Report Name | Anti-corrosion Coating for Semiconductor Equipment Parts Market |
Accounted market size in 2023 | US$ 866 million |
Forecasted market size in 2030 | US$ 1267.6 million |
CAGR | 5.7% |
Base Year | 2023 |
Forecasted years | 2024 - 2030 |
Segment by Coating Material |
|
Segment by Application |
|
By Region |
|
By Company | UCT (Ultra Clean Holdings, Inc), Pentagon Technologies, Enpro Industries, TOCALO Co., Ltd., Mitsubishi Chemical (Cleanpart), KoMiCo, Cinos, Hansol IONES, WONIK QnC, DFtech, TOPWINTECH, FEMVIX, SEWON HARDFACING CO.,LTD, Frontken Corporation Berhad, Value Engineering Co., Ltd, KERTZ HIGH TECH, Hung Jie Technology Corporation, Oerlikon Balzers, Beneq, APS Materials, Inc., SilcoTek, Alumiplate, Alcadyne, ASSET Solutions, Inc., Jiangsu Kaiweitesi Semiconductor Technology Co., Ltd., HCUT Co., Ltd, Ferrotec (Anhui) Technology Development Co., Ltd, Shanghai Companion |
Forecast units | USD million in value |
Report coverage | Revenue and volume forecast, company share, competitive landscape, growth factors and trends |