What is Global Metal Wafer End Effector Market?
The Global Metal Wafer End Effector Market is a specialized segment within the semiconductor equipment industry. Metal wafer end effectors are critical components used in semiconductor manufacturing processes. These devices are designed to handle and transport semiconductor wafers, which are thin slices of semiconductor material, typically silicon, used in the fabrication of integrated circuits and other microdevices. The market for metal wafer end effectors is driven by the increasing demand for semiconductors in various applications, including consumer electronics, automotive, and industrial sectors. The precision and reliability of these end effectors are crucial for maintaining the integrity of the wafers during the manufacturing process, thereby ensuring high-quality output. The market encompasses various types of metal wafer end effectors, including those made from aluminum and stainless steel, each offering distinct advantages in terms of strength, durability, and resistance to contamination. As the semiconductor industry continues to evolve and expand, the demand for advanced and efficient wafer handling solutions is expected to grow, making the global metal wafer end effector market a vital component of the semiconductor supply chain.
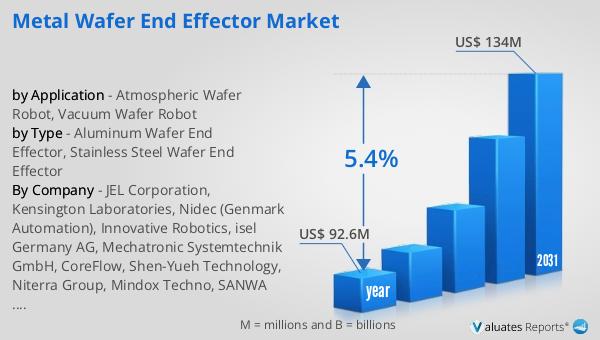
Aluminum Wafer End Effector, Stainless Steel Wafer End Effector in the Global Metal Wafer End Effector Market:
Aluminum wafer end effectors are widely used in the semiconductor industry due to their lightweight and high strength-to-weight ratio. These end effectors are designed to handle delicate semiconductor wafers with precision and care, minimizing the risk of damage during the manufacturing process. Aluminum's natural resistance to corrosion and its ability to dissipate heat effectively make it an ideal material for wafer handling in high-temperature environments. Additionally, aluminum end effectors can be easily machined and customized to meet specific requirements, offering flexibility in design and application. On the other hand, stainless steel wafer end effectors are known for their exceptional durability and resistance to wear and tear. Stainless steel's robustness makes it suitable for handling wafers in harsh environments where exposure to chemicals and abrasive materials is common. The material's inherent strength ensures that the end effectors can withstand repeated use without compromising performance. Moreover, stainless steel end effectors are often preferred in applications where cleanliness and contamination control are paramount, as the material can be easily cleaned and sterilized. Both aluminum and stainless steel wafer end effectors play a crucial role in the semiconductor manufacturing process, each offering unique benefits that cater to different operational needs. The choice between aluminum and stainless steel end effectors depends on various factors, including the specific requirements of the manufacturing process, the operating environment, and the desired balance between weight, strength, and resistance to contamination. As the semiconductor industry continues to advance, the demand for high-performance wafer handling solutions is expected to drive innovation and development in the global metal wafer end effector market.
Atmospheric Wafer Robot, Vacuum Wafer Robot in the Global Metal Wafer End Effector Market:
The usage of metal wafer end effectors in atmospheric wafer robots and vacuum wafer robots is integral to the semiconductor manufacturing process. Atmospheric wafer robots operate in environments where the wafers are exposed to ambient air. These robots are designed to handle wafers with precision and care, ensuring that they are transported safely between different stages of the manufacturing process. Metal wafer end effectors used in atmospheric wafer robots must be lightweight yet strong enough to handle the delicate wafers without causing damage. Aluminum end effectors are often preferred in these applications due to their lightweight nature and excellent strength-to-weight ratio. The ability to dissipate heat effectively also makes aluminum end effectors suitable for use in atmospheric environments where temperature control is critical. On the other hand, vacuum wafer robots operate in environments where the wafers are handled in a vacuum or low-pressure conditions. These robots are used in processes such as chemical vapor deposition (CVD) and physical vapor deposition (PVD), where maintaining a contaminant-free environment is crucial. Stainless steel wafer end effectors are commonly used in vacuum wafer robots due to their exceptional durability and resistance to contamination. The material's robustness ensures that the end effectors can withstand the harsh conditions of vacuum environments without compromising performance. Additionally, stainless steel's ability to be easily cleaned and sterilized makes it an ideal choice for applications where cleanliness is paramount. The use of metal wafer end effectors in both atmospheric and vacuum wafer robots highlights the importance of selecting the right material for specific applications. The choice between aluminum and stainless steel end effectors depends on various factors, including the operating environment, the specific requirements of the manufacturing process, and the desired balance between weight, strength, and resistance to contamination. As the semiconductor industry continues to evolve, the demand for advanced wafer handling solutions is expected to drive innovation and development in the global metal wafer end effector market.
Global Metal Wafer End Effector Market Outlook:
The global Metal Wafer End Effector market was valued at US$ 87 million in 2023 and is anticipated to reach US$ 121.3 million by 2030, witnessing a CAGR of 5.4% during the forecast period 2024-2030. This market growth reflects the increasing demand for high-quality semiconductor manufacturing equipment, driven by the expanding applications of semiconductors in various industries. The precision and reliability of metal wafer end effectors are crucial for maintaining the integrity of semiconductor wafers during the manufacturing process, ensuring high-quality output. The market encompasses various types of metal wafer end effectors, including those made from aluminum and stainless steel, each offering distinct advantages in terms of strength, durability, and resistance to contamination. As the semiconductor industry continues to advance, the demand for advanced and efficient wafer handling solutions is expected to grow, making the global metal wafer end effector market a vital component of the semiconductor supply chain. The projected growth in the market underscores the importance of innovation and development in wafer handling technologies to meet the evolving needs of the semiconductor industry.
Report Metric | Details |
Report Name | Metal Wafer End Effector Market |
Accounted market size in 2023 | US$ 87 million |
Forecasted market size in 2030 | US$ 121.3 million |
CAGR | 5.4% |
Base Year | 2023 |
Forecasted years | 2024 - 2030 |
Segment by Type |
|
Segment by Application |
|
Production by Region |
|
Consumption by Region |
|
By Company | JEL Corporation, Kensington Laboratories, Nidec (Genmark Automation), Innovative Robotics, isel Germany AG, Mechatronic Systemtechnik GmbH, CoreFlow, Shen-Yueh Technology, Niterra Group, Mindox Techno, SANWA ENGINEERING CORP. |
Forecast units | USD million in value |
Report coverage | Revenue and volume forecast, company share, competitive landscape, growth factors and trends |