What is Global Pricise Cleaning for Semiconductor Equipment Parts Market?
The global precise cleaning for semiconductor equipment parts market is a specialized sector focused on maintaining the cleanliness and functionality of semiconductor manufacturing equipment. This market is crucial because semiconductor devices are highly sensitive to contaminants, which can affect their performance and reliability. Precise cleaning involves removing microscopic particles, residues, and other contaminants from equipment parts to ensure optimal operation. The market encompasses various cleaning methods and technologies designed to meet the stringent requirements of the semiconductor industry. As the demand for advanced electronic devices continues to grow, the need for precise cleaning solutions becomes increasingly important. This market is driven by technological advancements, increasing production of semiconductors, and the need for high-quality, reliable electronic components.
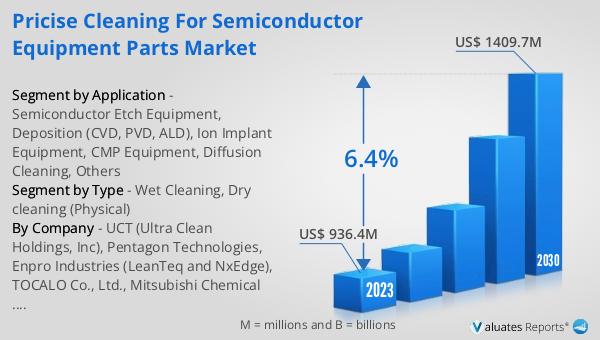
Wet Cleaning, Dry cleaning (Physical) in the Global Pricise Cleaning for Semiconductor Equipment Parts Market:
Wet cleaning and dry cleaning (physical) are two primary methods used in the global precise cleaning for semiconductor equipment parts market. Wet cleaning involves the use of liquid chemicals to remove contaminants from equipment parts. This method is highly effective in dissolving and washing away particles, residues, and other impurities. Common wet cleaning techniques include chemical baths, ultrasonic cleaning, and megasonic cleaning. Chemical baths use specific solutions to dissolve contaminants, while ultrasonic and megasonic cleaning use high-frequency sound waves to agitate the cleaning solution, enhancing its ability to remove particles. Wet cleaning is particularly effective for removing organic contaminants and particles that are difficult to dislodge with physical methods. On the other hand, dry cleaning (physical) methods do not involve the use of liquids. Instead, they rely on physical forces to remove contaminants. Common dry cleaning techniques include plasma cleaning, laser cleaning, and cryogenic cleaning. Plasma cleaning uses ionized gas to break down and remove contaminants from surfaces. This method is highly effective for removing organic residues and can also modify the surface properties of the equipment parts to improve their performance. Laser cleaning uses focused laser beams to vaporize and remove contaminants. This method is precise and can be used to clean specific areas without affecting the surrounding surfaces. Cryogenic cleaning involves the use of solid carbon dioxide (dry ice) pellets that are blasted onto the surface to remove contaminants through a combination of thermal shock and mechanical action. Both wet and dry cleaning methods have their advantages and are chosen based on the specific requirements of the cleaning process. Wet cleaning is generally more effective for removing a wide range of contaminants, including organic and inorganic residues. It is also suitable for cleaning complex geometries and hard-to-reach areas. However, it requires careful handling and disposal of chemical solutions to avoid environmental and safety hazards. Dry cleaning methods, on the other hand, are more environmentally friendly as they do not produce liquid waste. They are also suitable for cleaning delicate surfaces that may be damaged by liquid chemicals. However, dry cleaning methods may not be as effective for removing certain types of contaminants, such as heavy organic residues. In the global precise cleaning for semiconductor equipment parts market, both wet and dry cleaning methods are used in combination to achieve the highest level of cleanliness. The choice of cleaning method depends on factors such as the type of contaminants, the material of the equipment parts, and the specific requirements of the semiconductor manufacturing process. As the semiconductor industry continues to advance, the demand for more efficient and effective cleaning solutions is expected to grow, driving innovation and development in both wet and dry cleaning technologies.
Semiconductor Etch Equipment, Deposition (CVD, PVD, ALD), Ion Implant Equipment, CMP Equipment, Diffusion Cleaning, Others in the Global Pricise Cleaning for Semiconductor Equipment Parts Market:
The usage of global precise cleaning for semiconductor equipment parts market spans several critical areas, including semiconductor etch equipment, deposition (CVD, PVD, ALD), ion implant equipment, CMP equipment, diffusion cleaning, and others. In semiconductor etch equipment, precise cleaning is essential to remove residues and particles that can affect the etching process. Etching involves the removal of material from the surface of a semiconductor wafer to create patterns and structures. Any contaminants on the equipment parts can lead to defects in the etched patterns, affecting the performance of the final semiconductor devices. Precise cleaning ensures that the etch equipment operates at optimal efficiency and produces high-quality results. In deposition processes such as Chemical Vapor Deposition (CVD), Physical Vapor Deposition (PVD), and Atomic Layer Deposition (ALD), precise cleaning is crucial to maintain the purity and uniformity of the deposited layers. These processes involve the deposition of thin films of material onto the surface of a semiconductor wafer. Contaminants on the equipment parts can lead to defects in the deposited layers, affecting the performance and reliability of the semiconductor devices. Precise cleaning ensures that the deposition equipment is free from contaminants, resulting in high-quality, uniform thin films. Ion implant equipment is used to introduce dopants into the semiconductor wafer to modify its electrical properties. Precise cleaning is essential to remove any contaminants that can affect the implantation process. Contaminants on the equipment parts can lead to non-uniform doping, affecting the performance of the semiconductor devices. Precise cleaning ensures that the ion implant equipment operates at optimal efficiency and produces consistent, high-quality results. Chemical Mechanical Planarization (CMP) equipment is used to planarize the surface of a semiconductor wafer to achieve a smooth, flat surface. Precise cleaning is crucial to remove any particles and residues that can affect the planarization process. Contaminants on the equipment parts can lead to defects in the planarized surface, affecting the performance of the semiconductor devices. Precise cleaning ensures that the CMP equipment operates at optimal efficiency and produces high-quality, smooth surfaces. Diffusion cleaning involves the removal of contaminants from the surface of a semiconductor wafer before and after diffusion processes. Diffusion is used to introduce dopants into the semiconductor wafer to modify its electrical properties. Precise cleaning is essential to remove any contaminants that can affect the diffusion process. Contaminants on the equipment parts can lead to non-uniform doping, affecting the performance of the semiconductor devices. Precise cleaning ensures that the diffusion equipment operates at optimal efficiency and produces consistent, high-quality results. In addition to these specific areas, precise cleaning is also used in other semiconductor manufacturing processes to ensure the cleanliness and functionality of equipment parts. This includes cleaning of photolithography equipment, metrology equipment, and other critical tools used in semiconductor manufacturing. Precise cleaning ensures that these tools operate at optimal efficiency and produce high-quality, reliable semiconductor devices. Overall, the usage of global precise cleaning for semiconductor equipment parts market is essential to maintain the cleanliness and functionality of equipment parts in various semiconductor manufacturing processes. This ensures that the semiconductor devices produced are of high quality, reliable, and meet the stringent requirements of the industry. As the demand for advanced electronic devices continues to grow, the need for precise cleaning solutions becomes increasingly important, driving innovation and development in this market.
Global Pricise Cleaning for Semiconductor Equipment Parts Market Outlook:
The global precise cleaning for semiconductor equipment parts market was valued at $936.4 million in 2023 and is projected to reach $1,409.7 million by 2030, reflecting a compound annual growth rate (CAGR) of 6.4% during the forecast period from 2024 to 2030. According to SEMI, worldwide sales of semiconductor manufacturing equipment increased by 5% from $102.6 billion in 2021 to an all-time high of $107.6 billion in 2022. For the third consecutive year, China remained the largest semiconductor equipment market in 2022, despite a 5% slowdown in the pace of investments in the region year over year, accounting for $28.3 billion in billings.
Report Metric | Details |
Report Name | Pricise Cleaning for Semiconductor Equipment Parts Market |
Accounted market size in 2023 | US$ 936.4 million |
Forecasted market size in 2030 | US$ 1409.7 million |
CAGR | 6.4% |
Base Year | 2023 |
Forecasted years | 2024 - 2030 |
Segment by Type |
|
Segment by Application |
|
By Region |
|
By Company | UCT (Ultra Clean Holdings, Inc), Pentagon Technologies, Enpro Industries (LeanTeq and NxEdge), TOCALO Co., Ltd., Mitsubishi Chemical (Cleanpart), KoMiCo, Cinos, Hansol IONES, WONIK QnC, DFtech, Frontken Corporation Berhad, Value Engineering Co., Ltd, Shih Her Technology, KERTZ HIGH TECH, Hung Jie Technology Corporation, Jiangsu Kaiweitesi Semiconductor Technology Co., Ltd., HCUT Co., Ltd, Ferrotec (Anhui) Technology Development Co., Ltd, Neutron Technology Enterprise, JST Manufacturing |
Forecast units | USD million in value |
Report coverage | Revenue and volume forecast, company share, competitive landscape, growth factors and trends |