What is Global Face Plate for Semiconductor Shower Head Market?
The Global Face Plate for Semiconductor Shower Head Market is a specialized segment within the semiconductor manufacturing industry. Face plates are critical components used in semiconductor shower heads, which are essential for processes like chemical vapor deposition (CVD) and physical vapor deposition (PVD). These face plates ensure the uniform distribution of gases over the wafer surface, which is crucial for the consistent quality of semiconductor devices. The market for these face plates is driven by the increasing demand for semiconductors in various applications, including consumer electronics, automotive, and industrial sectors. As technology advances, the need for more precise and efficient semiconductor manufacturing processes grows, further propelling the demand for high-quality face plates. Companies in this market are continuously innovating to improve the materials and designs of face plates to meet the stringent requirements of modern semiconductor fabrication. The global market for face plates is characterized by a mix of established players and new entrants, all striving to capture a share of this niche but vital market.
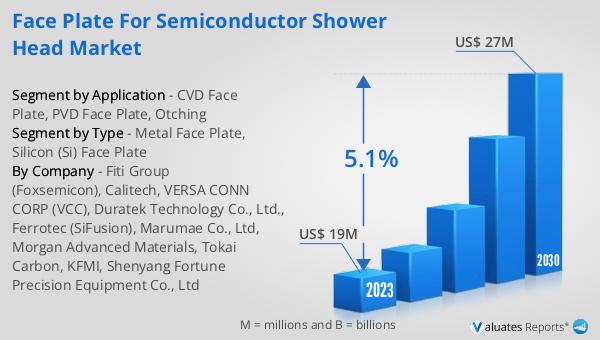
Metal Face Plate, Silicon (Si) Face Plate in the Global Face Plate for Semiconductor Shower Head Market:
Metal face plates and silicon (Si) face plates are two primary types of face plates used in the Global Face Plate for Semiconductor Shower Head Market. Metal face plates are typically made from materials like stainless steel, aluminum, or other metal alloys. These face plates are known for their durability and ability to withstand high temperatures and corrosive environments, making them suitable for various semiconductor manufacturing processes. Metal face plates are often used in applications where mechanical strength and longevity are critical. On the other hand, silicon face plates are made from high-purity silicon, the same material used in semiconductor wafers. Silicon face plates offer excellent thermal conductivity and chemical resistance, which are essential for maintaining the integrity of the semiconductor manufacturing process. They are particularly useful in processes that require high precision and minimal contamination. The choice between metal and silicon face plates depends on the specific requirements of the semiconductor manufacturing process, including factors like temperature, chemical exposure, and the desired level of precision. Both types of face plates play a crucial role in ensuring the efficiency and quality of semiconductor production. Companies in this market are constantly researching and developing new materials and designs to enhance the performance of face plates, addressing the evolving needs of the semiconductor industry.
CVD Face Plate, PVD Face Plate, Otching in the Global Face Plate for Semiconductor Shower Head Market:
The usage of Global Face Plate for Semiconductor Shower Head Market in areas such as CVD face plates, PVD face plates, and etching is extensive and critical for the semiconductor manufacturing process. In Chemical Vapor Deposition (CVD), face plates are used to distribute precursor gases uniformly over the wafer surface, ensuring consistent film deposition. The quality of the face plate directly impacts the uniformity and quality of the thin films deposited on the wafers. High-quality CVD face plates are essential for producing semiconductors with precise electrical properties and minimal defects. In Physical Vapor Deposition (PVD), face plates play a similar role in distributing sputtering gases evenly across the wafer. PVD processes often involve high-energy particles, and the face plates must be able to withstand these conditions while maintaining uniform gas distribution. The performance of PVD face plates is crucial for achieving the desired thickness and composition of the deposited films. In etching processes, face plates are used to control the distribution of etching gases, which remove material from the wafer surface to create the desired patterns. The precision and uniformity of the etching process are heavily dependent on the quality of the face plates. Any inconsistencies in gas distribution can lead to defects and reduced yield in semiconductor production. Overall, the face plates used in CVD, PVD, and etching processes are vital components that directly influence the efficiency, quality, and yield of semiconductor manufacturing. Companies in this market are continually innovating to develop face plates that meet the stringent requirements of these processes, ensuring the production of high-performance semiconductor devices.
Global Face Plate for Semiconductor Shower Head Market Outlook:
The global Face Plate for Semiconductor Shower Head market was valued at US$ 19 million in 2023 and is anticipated to reach US$ 27 million by 2030, witnessing a CAGR of 5.1% during the forecast period 2024-2030. According to SEMI, worldwide sales of semiconductor manufacturing equipment increased 5% from $102.6 billion in 2021 to an all-time record of $107.6 billion in 2022. For the third consecutive year, China remained the largest semiconductor equipment market in 2022, despite a 5% slowdown in the pace of investments in the region year over year, accounting for $28.3 billion in billings. This growth in the semiconductor equipment market highlights the increasing demand for advanced manufacturing technologies, including face plates for semiconductor shower heads. The continuous investment in semiconductor manufacturing infrastructure, particularly in regions like China, underscores the critical role of face plates in ensuring the efficiency and quality of semiconductor production. As the semiconductor industry continues to expand, the demand for high-quality face plates is expected to grow, driving innovation and development in this specialized market segment.
Report Metric | Details |
Report Name | Face Plate for Semiconductor Shower Head Market |
Accounted market size in 2023 | US$ 19 million |
Forecasted market size in 2030 | US$ 27 million |
CAGR | 5.1% |
Base Year | 2023 |
Forecasted years | 2024 - 2030 |
Segment by Type |
|
Segment by Application |
|
Production by Region |
|
Consumption by Region |
|
By Company | Fiti Group (Foxsemicon), Calitech, VERSA CONN CORP (VCC), Duratek Technology Co., Ltd., Ferrotec (SiFusion), Marumae Co., Ltd, Morgan Advanced Materials, Tokai Carbon, KFMI, Shenyang Fortune Precision Equipment Co., Ltd |
Forecast units | USD million in value |
Report coverage | Revenue and volume forecast, company share, competitive landscape, growth factors and trends |