What is Global Wafer Handling Arm for Semiconductor Wafer Robots Market?
The Global Wafer Handling Arm for Semiconductor Wafer Robots Market is a specialized segment within the semiconductor manufacturing industry that focuses on the development and deployment of robotic arms designed to handle semiconductor wafers. These robotic arms are crucial for the precise and efficient movement of wafers during the manufacturing process, ensuring minimal contamination and damage. The market encompasses various types of wafer handling arms, each tailored to specific stages of wafer processing, from initial wafer loading to final inspection. These arms are equipped with advanced sensors and control systems to maintain high levels of accuracy and repeatability. The increasing demand for semiconductors in various applications, such as consumer electronics, automotive, and telecommunications, drives the growth of this market. Additionally, advancements in robotics and automation technologies further enhance the capabilities of wafer handling arms, making them indispensable in modern semiconductor fabs.
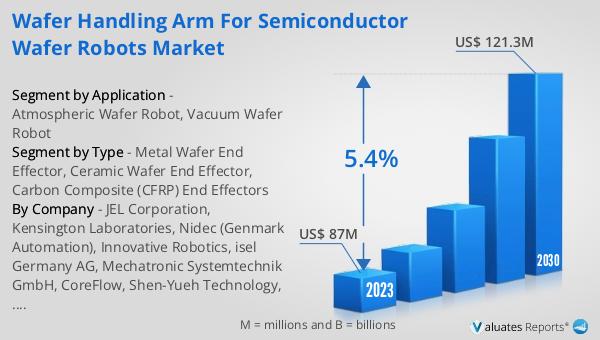
Metal Wafer End Effector, Ceramic Wafer End Effector, Carbon Composite (CFRP) End Effectors in the Global Wafer Handling Arm for Semiconductor Wafer Robots Market:
In the Global Wafer Handling Arm for Semiconductor Wafer Robots Market, different types of end effectors are used to handle wafers, each with unique properties and applications. Metal Wafer End Effectors are commonly used due to their durability and strength. They are typically made from stainless steel or aluminum, providing a robust solution for handling wafers in various stages of the manufacturing process. These end effectors are designed to withstand harsh environments and repeated use, making them ideal for high-throughput applications. However, their weight and potential for contamination are drawbacks that need to be managed. Ceramic Wafer End Effectors offer a lightweight and non-contaminating alternative to metal end effectors. Made from materials like alumina or zirconia, these end effectors provide excellent thermal and chemical resistance, making them suitable for use in high-temperature and corrosive environments. Their non-conductive nature also makes them ideal for applications where electrical interference needs to be minimized. Despite their advantages, ceramic end effectors can be brittle and prone to chipping, requiring careful handling and maintenance. Carbon Composite (CFRP) End Effectors combine the best of both worlds, offering a lightweight and durable solution for wafer handling. Made from carbon fiber reinforced polymers, these end effectors provide high strength-to-weight ratios and excellent resistance to thermal and chemical stresses. Their low mass reduces the load on robotic arms, enhancing the speed and precision of wafer handling operations. Additionally, CFRP end effectors are less likely to generate particles, reducing the risk of contamination. However, their higher cost compared to metal and ceramic end effectors can be a limiting factor for some applications. Each type of end effector has its own set of advantages and challenges, and the choice of end effector depends on the specific requirements of the wafer handling application.
Atmospheric Wafer Robot, Vacuum Wafer Robot in the Global Wafer Handling Arm for Semiconductor Wafer Robots Market:
The usage of Global Wafer Handling Arm for Semiconductor Wafer Robots Market is critical in both Atmospheric Wafer Robots and Vacuum Wafer Robots. Atmospheric Wafer Robots operate in environments where the wafers are exposed to air. These robots are typically used in the initial stages of wafer processing, such as wafer loading, alignment, and inspection. The wafer handling arms in these robots must be designed to minimize contamination and ensure precise positioning of the wafers. Advanced sensors and control systems are integrated into these arms to maintain high levels of accuracy and repeatability. The use of lightweight materials, such as carbon composites, helps reduce the load on the robotic arms, enhancing their speed and efficiency. Additionally, the arms are often equipped with end effectors made from materials like ceramics or metals, depending on the specific requirements of the application. Vacuum Wafer Robots, on the other hand, operate in vacuum environments where the wafers are processed in the absence of air. These robots are used in critical stages of wafer processing, such as etching, deposition, and lithography. The wafer handling arms in these robots must be designed to operate under vacuum conditions, which require specialized materials and designs to prevent outgassing and contamination. Ceramic and carbon composite end effectors are commonly used in vacuum wafer robots due to their excellent thermal and chemical resistance. The arms are also equipped with advanced control systems to ensure precise and repeatable movements, which are crucial for maintaining the integrity of the wafers during processing. The integration of sensors and feedback mechanisms allows for real-time monitoring and adjustment of the arm's movements, ensuring optimal performance. Both atmospheric and vacuum wafer robots play a vital role in the semiconductor manufacturing process, and the choice of wafer handling arm depends on the specific requirements of the application. The advancements in materials and control systems have significantly enhanced the capabilities of these robots, making them indispensable in modern semiconductor fabs.
Global Wafer Handling Arm for Semiconductor Wafer Robots Market Outlook:
The global Wafer Handling Arm for Semiconductor Wafer Robots market was valued at US$ 87 million in 2023 and is anticipated to reach US$ 121.3 million by 2030, witnessing a CAGR of 5.4% during the forecast period 2024-2030. According to SEMI, worldwide sales of semiconductor manufacturing equipment increased 5% from $102.6 billion in 2021 to an all-time record of $107.6 billion in 2022. For the third consecutive year, China remained the largest semiconductor equipment market in 2022, despite a 5% slowdown in the pace of investments in the region year over year, accounting for $28.3 billion in billings. This growth in the semiconductor equipment market highlights the increasing demand for advanced wafer handling solutions, which are essential for maintaining the efficiency and precision of semiconductor manufacturing processes. The continuous advancements in robotics and automation technologies are expected to further drive the growth of the wafer handling arm market, as manufacturers seek to enhance their production capabilities and meet the growing demand for semiconductors across various industries.
Report Metric | Details |
Report Name | Wafer Handling Arm for Semiconductor Wafer Robots Market |
Accounted market size in 2023 | US$ 87 million |
Forecasted market size in 2030 | US$ 121.3 million |
CAGR | 5.4% |
Base Year | 2023 |
Forecasted years | 2024 - 2030 |
Segment by Type |
|
Segment by Application |
|
Production by Region |
|
Consumption by Region |
|
By Company | JEL Corporation, Kensington Laboratories, Nidec (Genmark Automation), Innovative Robotics, isel Germany AG, Mechatronic Systemtechnik GmbH, CoreFlow, Shen-Yueh Technology, Coorstek, NGK SPARK PLUG, ASUZAC Fine Ceramics, Astel Srl - Semisyn division, CeramTec, Mindox Techno, Kyocera, Morgan Advanced Materials, Japan Fine Ceramics Co., Ltd. (JFC), 3M, Ferrotec, St.Cera Co., Ltd, SANWA ENGINEERING CORP., Shanghai Companion, Sanzer (Shanghai) New Materials Technology |
Forecast units | USD million in value |
Report coverage | Revenue and volume forecast, company share, competitive landscape, growth factors and trends |