What is Global PU Release Agent For Automotive Seats Market?
The Global PU Release Agent for Automotive Seats Market is a specialized segment within the broader automotive industry, focusing on the production and application of release agents specifically designed for polyurethane (PU) automotive seats. These release agents are crucial in the manufacturing process, as they facilitate the easy removal of molded PU seats from their molds without damaging the seats or the molds themselves. This market is driven by the increasing demand for high-quality, durable, and comfortable seating in vehicles, which in turn requires efficient and effective manufacturing processes. The release agents used in this market are formulated to provide optimal performance, ensuring that the seats maintain their integrity and finish throughout the production process. As the automotive industry continues to evolve with advancements in technology and materials, the demand for specialized release agents that can meet the stringent requirements of modern manufacturing processes is expected to grow. This market is characterized by a range of products tailored to different types of PU formulations and manufacturing conditions, highlighting the importance of innovation and customization in meeting the diverse needs of automotive manufacturers.
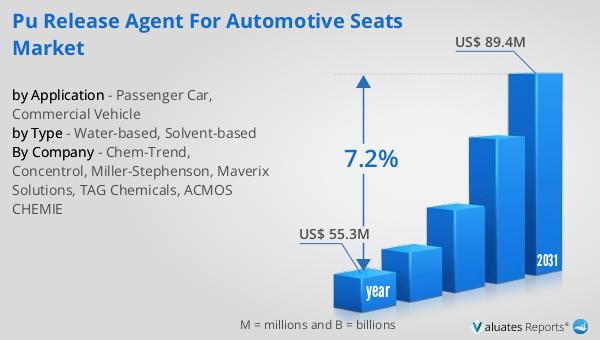
Water-based, Solvent-based in the Global PU Release Agent For Automotive Seats Market:
In the Global PU Release Agent for Automotive Seats Market, two primary types of release agents are commonly used: water-based and solvent-based. Each type has its own set of characteristics, advantages, and challenges, making them suitable for different applications and manufacturing environments. Water-based release agents are formulated with water as the primary carrier, making them more environmentally friendly compared to their solvent-based counterparts. They are designed to reduce volatile organic compound (VOC) emissions, which is a significant consideration for manufacturers aiming to comply with environmental regulations and reduce their carbon footprint. Water-based agents are generally non-flammable, reducing the risk of fire hazards in the manufacturing environment. They are also easier to clean up, as they do not leave behind oily residues that can interfere with subsequent processes or affect the quality of the finished product. However, water-based release agents may require more precise application techniques and conditions to ensure optimal performance, as they can be sensitive to humidity and temperature variations. On the other hand, solvent-based release agents use organic solvents as their primary carrier, which can offer superior performance in certain applications. These agents are known for their excellent release properties, providing a smooth and consistent finish on the molded PU seats. Solvent-based agents are often preferred in situations where rapid drying and curing are essential, as they tend to evaporate quickly, allowing for faster production cycles. They are also less sensitive to environmental conditions, making them more versatile in different manufacturing settings. However, the use of solvent-based agents comes with challenges, particularly concerning environmental and safety regulations. The presence of VOCs in these agents can contribute to air pollution and pose health risks to workers, necessitating the implementation of strict safety measures and ventilation systems in manufacturing facilities. Additionally, the flammable nature of many solvents requires careful handling and storage to prevent accidents. Despite these challenges, solvent-based release agents remain popular in the industry due to their proven effectiveness and reliability. Manufacturers often choose between water-based and solvent-based release agents based on their specific production needs, regulatory requirements, and environmental considerations. The choice of release agent can significantly impact the efficiency and quality of the manufacturing process, making it a critical decision for automotive seat producers. As the industry continues to prioritize sustainability and innovation, there is ongoing research and development aimed at improving the performance and environmental profile of both water-based and solvent-based release agents. This includes the development of hybrid formulations that combine the benefits of both types, offering enhanced performance while minimizing environmental impact. The Global PU Release Agent for Automotive Seats Market is thus characterized by a dynamic interplay between technological advancements, regulatory pressures, and evolving consumer preferences, driving continuous innovation and adaptation in the industry.
Passenger Car, Commercial Vehicle in the Global PU Release Agent For Automotive Seats Market:
The usage of Global PU Release Agent for Automotive Seats Market is particularly significant in the production of seats for passenger cars and commercial vehicles, each with its own set of requirements and challenges. In the passenger car segment, the focus is often on comfort, aesthetics, and durability, as these factors play a crucial role in consumer satisfaction and brand perception. PU release agents are essential in ensuring that the seats meet these high standards, as they facilitate the production of seats with smooth surfaces, consistent textures, and precise dimensions. The use of high-quality release agents helps prevent defects such as surface blemishes, uneven textures, or dimensional inaccuracies, which can compromise the comfort and appearance of the seats. In addition to aesthetic considerations, passenger car seats must also meet stringent safety and durability standards, as they are subject to regular use and wear. Release agents contribute to the structural integrity of the seats by ensuring that the PU foam is properly molded and cured, providing the necessary support and resilience. In the commercial vehicle segment, the emphasis is often on durability, functionality, and cost-effectiveness, as these vehicles are typically used for business purposes and are subject to more demanding conditions. PU release agents play a critical role in the production of seats that can withstand heavy use, exposure to harsh environments, and frequent cleaning. The release agents used in this segment are formulated to provide excellent release properties, ensuring that the seats can be produced efficiently and with minimal defects. This is particularly important in commercial applications, where downtime and production delays can have significant financial implications. Moreover, the use of effective release agents helps extend the lifespan of the molds, reducing maintenance costs and improving overall production efficiency. As the demand for commercial vehicles continues to grow, driven by factors such as e-commerce expansion and urbanization, the need for reliable and cost-effective seating solutions is expected to increase. The Global PU Release Agent for Automotive Seats Market is thus poised to play a vital role in supporting the production of high-quality seats for both passenger cars and commercial vehicles, catering to the diverse needs of manufacturers and consumers alike.
Global PU Release Agent For Automotive Seats Market Outlook:
In 2024, the global market for PU Release Agent for Automotive Seats was valued at approximately $55.3 million. This market is anticipated to experience significant growth over the coming years, with projections indicating that it will reach an estimated size of $89.4 million by 2031. This growth trajectory represents a compound annual growth rate (CAGR) of 7.2% during the forecast period. The expansion of this market can be attributed to several factors, including the increasing demand for high-quality automotive seating solutions, advancements in manufacturing technologies, and the growing emphasis on sustainability and environmental compliance. As automotive manufacturers strive to enhance the comfort, durability, and aesthetic appeal of their vehicles, the need for specialized release agents that can facilitate efficient and defect-free production processes becomes increasingly important. Additionally, the rising awareness of environmental issues and the implementation of stricter regulations regarding VOC emissions are driving the adoption of more sustainable release agent solutions, such as water-based formulations. This shift towards environmentally friendly products is expected to further propel the growth of the market, as manufacturers seek to align their operations with global sustainability goals. Overall, the Global PU Release Agent for Automotive Seats Market is poised for robust growth, driven by a combination of technological innovation, regulatory pressures, and evolving consumer preferences.
Report Metric | Details |
Report Name | PU Release Agent For Automotive Seats Market |
Accounted market size in year | US$ 55.3 million |
Forecasted market size in 2031 | US$ 89.4 million |
CAGR | 7.2% |
Base Year | year |
Forecasted years | 2025 - 2031 |
by Type |
|
by Application |
|
Production by Region |
|
Consumption by Region |
|
By Company | Chem-Trend, Concentrol, Miller-Stephenson, Maverix Solutions, TAG Chemicals, ACMOS CHEMIE |
Forecast units | USD million in value |
Report coverage | Revenue and volume forecast, company share, competitive landscape, growth factors and trends |