What is Global Food and Powder Gravity Feed Metal Detection Market?
The Global Food and Powder Gravity Feed Metal Detection Market is a specialized segment within the broader metal detection industry, focusing on the detection of metal contaminants in food and powder products. This market is crucial for ensuring the safety and quality of consumable goods, as metal contaminants can pose significant health risks to consumers and lead to costly recalls for manufacturers. Gravity feed metal detectors are designed to inspect bulk products as they flow through a production line, using gravity to move the product through the detection system. These detectors are highly sensitive and capable of identifying even the smallest metal particles, ensuring that contaminated products are identified and removed before reaching the consumer. The market for these detectors is driven by stringent food safety regulations and the increasing demand for high-quality, contaminant-free products. As consumer awareness of food safety continues to grow, manufacturers are investing in advanced detection technologies to maintain compliance and protect their brand reputation. The Global Food and Powder Gravity Feed Metal Detection Market is characterized by continuous innovation, with manufacturers developing more sophisticated and efficient detection systems to meet the evolving needs of the industry.
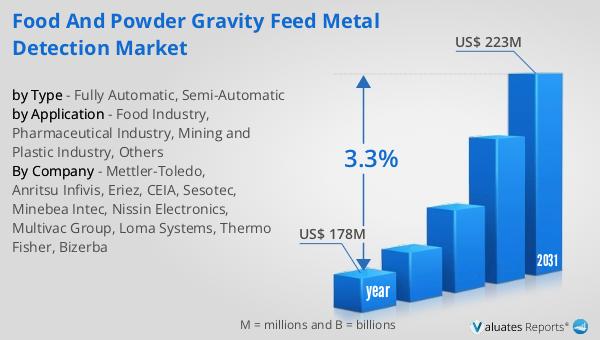
Fully Automatic, Semi-Automatic in the Global Food and Powder Gravity Feed Metal Detection Market:
In the Global Food and Powder Gravity Feed Metal Detection Market, the distinction between fully automatic and semi-automatic systems is significant, as it influences the efficiency, cost, and operational complexity of the detection process. Fully automatic metal detection systems are designed to operate with minimal human intervention, offering a seamless integration into production lines. These systems are equipped with advanced sensors and software that allow them to automatically adjust to different product types and flow rates, ensuring consistent detection accuracy. The primary advantage of fully automatic systems is their ability to handle large volumes of product with high speed and precision, making them ideal for large-scale manufacturing operations. They also reduce the risk of human error, as the system can automatically reject contaminated products without the need for manual inspection. However, the initial investment for fully automatic systems can be substantial, which may be a consideration for smaller manufacturers. On the other hand, semi-automatic metal detection systems require some level of human intervention, typically in the form of manual adjustments or inspections. These systems are often more affordable than their fully automatic counterparts, making them accessible to smaller businesses or those with limited budgets. Semi-automatic systems offer flexibility, as operators can manually adjust settings to accommodate different product types or production conditions. This can be advantageous in environments where product variability is high, or where production volumes do not justify the cost of a fully automatic system. However, the reliance on human intervention can introduce variability in detection accuracy, as the effectiveness of the system is partly dependent on the skill and attentiveness of the operator. Both fully automatic and semi-automatic systems have their place in the Global Food and Powder Gravity Feed Metal Detection Market, with the choice between the two largely dependent on the specific needs and resources of the manufacturer. For large-scale operations with high production volumes and a focus on efficiency, fully automatic systems offer a compelling solution. These systems can significantly reduce labor costs and improve throughput, making them a valuable investment for companies looking to optimize their production processes. Conversely, for smaller operations or those with more variable production requirements, semi-automatic systems provide a cost-effective alternative that still offers reliable detection capabilities. The decision between fully automatic and semi-automatic systems also involves considerations of maintenance and technical support. Fully automatic systems, with their advanced technology, may require more specialized maintenance and support, which can add to the overall cost of ownership. Manufacturers must weigh these factors against the potential benefits of increased efficiency and reduced labor costs. In contrast, semi-automatic systems, with their simpler design, may be easier to maintain and repair, offering a lower total cost of ownership over time. Ultimately, the choice between fully automatic and semi-automatic metal detection systems in the Global Food and Powder Gravity Feed Metal Detection Market is a strategic decision that depends on a variety of factors, including production volume, budget, and the specific requirements of the manufacturing process. Both types of systems play a crucial role in ensuring product safety and quality, helping manufacturers meet regulatory standards and protect their brand reputation. As the market continues to evolve, manufacturers will need to carefully evaluate their options to select the system that best aligns with their operational goals and resources.
Food Industry, Pharmaceutical Industry, Mining and Plastic Industry, Others in the Global Food and Powder Gravity Feed Metal Detection Market:
The Global Food and Powder Gravity Feed Metal Detection Market finds its application across various industries, each with unique requirements and challenges. In the food industry, metal detection is critical for ensuring product safety and compliance with stringent regulatory standards. Food manufacturers use gravity feed metal detectors to inspect bulk products such as grains, powders, and other dry goods for metal contaminants. These detectors help prevent contaminated products from reaching consumers, thereby protecting public health and minimizing the risk of costly recalls. The ability to detect even the smallest metal particles is essential in maintaining the integrity of food products and upholding brand reputation. In the pharmaceutical industry, the use of gravity feed metal detectors is equally important. Pharmaceutical manufacturers must adhere to strict quality control standards to ensure the safety and efficacy of their products. Metal contamination in pharmaceuticals can have serious health implications, making detection systems a vital component of the production process. Gravity feed metal detectors are used to inspect powders and granules, ensuring that any metal contaminants are identified and removed before the products are packaged and distributed. The precision and reliability of these detectors are crucial in maintaining the high standards required in pharmaceutical manufacturing. The mining industry also benefits from the use of gravity feed metal detection systems. In this sector, metal detectors are used to identify and separate valuable metal ores from unwanted materials. Gravity feed systems are particularly effective in processing bulk materials, allowing for efficient sorting and extraction of metals. This not only enhances the efficiency of mining operations but also contributes to the sustainability of the industry by reducing waste and optimizing resource utilization. The ability to accurately detect and separate metals is essential for maximizing the yield and profitability of mining activities. In the plastic industry, gravity feed metal detectors play a role in ensuring the quality and safety of plastic products. Metal contaminants in plastic can compromise the integrity and performance of the final product, leading to defects and potential safety hazards. By using metal detection systems, manufacturers can identify and remove metal particles from raw materials before they are processed, ensuring that the final products meet quality standards. This is particularly important in industries where plastic components are used in critical applications, such as automotive or medical devices. Beyond these industries, gravity feed metal detection systems are used in various other sectors where the detection of metal contaminants is necessary. This includes the chemical industry, where metal detection is used to ensure the purity of chemical compounds, and the textile industry, where metal detectors help prevent damage to machinery and ensure product quality. The versatility and effectiveness of gravity feed metal detection systems make them an invaluable tool across a wide range of applications, helping manufacturers maintain high standards of safety and quality in their products.
Global Food and Powder Gravity Feed Metal Detection Market Outlook:
The global market for Food and Powder Gravity Feed Metal Detection was valued at $178 million in 2024, with projections indicating a growth to $223 million by 2031. This growth represents a compound annual growth rate (CAGR) of 3.3% over the forecast period. This market expansion reflects the increasing demand for advanced metal detection technologies across various industries, driven by the need for enhanced product safety and compliance with regulatory standards. As manufacturers strive to meet consumer expectations for high-quality, contaminant-free products, the adoption of gravity feed metal detection systems is expected to rise. These systems offer a reliable solution for detecting metal contaminants in bulk products, ensuring that only safe and high-quality goods reach the market. The projected growth of the market also highlights the ongoing innovation and development within the industry. Manufacturers are continually advancing their detection technologies to improve sensitivity, accuracy, and efficiency, catering to the evolving needs of different sectors. This includes the development of more sophisticated software and sensor technologies that enhance the performance of metal detection systems. As a result, companies are better equipped to address the challenges of metal contamination, reducing the risk of recalls and protecting their brand reputation. Furthermore, the market's growth is supported by the increasing awareness of food safety among consumers and the stringent regulations imposed by governments and industry bodies. These factors are compelling manufacturers to invest in state-of-the-art detection systems to ensure compliance and maintain consumer trust. As the market continues to expand, it presents significant opportunities for manufacturers and suppliers of gravity feed metal detection systems to capitalize on the growing demand for advanced detection solutions.
Report Metric | Details |
Report Name | Food and Powder Gravity Feed Metal Detection Market |
Accounted market size in year | US$ 178 million |
Forecasted market size in 2031 | US$ 223 million |
CAGR | 3.3% |
Base Year | year |
Forecasted years | 2025 - 2031 |
by Type |
|
by Application |
|
Production by Region |
|
Consumption by Region |
|
By Company | Mettler-Toledo, Anritsu Infivis, Eriez, CEIA, Sesotec, Minebea Intec, Nissin Electronics, Multivac Group, Loma Systems, Thermo Fisher, Bizerba |
Forecast units | USD million in value |
Report coverage | Revenue and volume forecast, company share, competitive landscape, growth factors and trends |