What is Global Laser Direct Writing (LDW) Equipment for IC Substrate Market?
Global Laser Direct Writing (LDW) Equipment for IC Substrate Market refers to the specialized machinery used in the semiconductor industry to create intricate patterns on integrated circuit (IC) substrates using laser technology. This equipment is crucial for the production of IC substrates, which are foundational components in electronic devices. The LDW process involves directing a laser beam to write or etch patterns directly onto the substrate material, allowing for high precision and flexibility in design. This technology is particularly valuable in the manufacturing of advanced electronic components, where traditional photolithography methods may fall short. The global market for LDW equipment is driven by the increasing demand for miniaturized and high-performance electronic devices, as well as the need for more efficient and cost-effective manufacturing processes. As the electronics industry continues to evolve, the role of LDW equipment in producing high-quality IC substrates becomes increasingly significant.
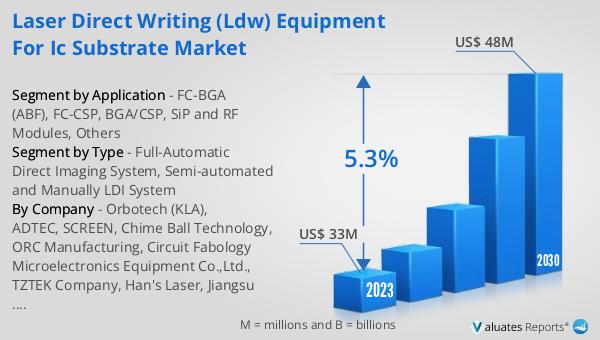
Full-Automatic Direct Imaging System, Semi-automated and Manually LDI System in the Global Laser Direct Writing (LDW) Equipment for IC Substrate Market:
The Full-Automatic Direct Imaging System, Semi-automated, and Manually LDI System are three distinct types of Laser Direct Writing (LDW) equipment used in the IC substrate market, each offering varying levels of automation and precision. The Full-Automatic Direct Imaging System is the most advanced among the three, providing complete automation in the imaging process. This system is designed to handle high-volume production with minimal human intervention, ensuring consistent quality and high throughput. It utilizes sophisticated software and hardware to precisely control the laser beam, enabling the creation of highly detailed patterns on the substrate. The full automation not only enhances productivity but also reduces the likelihood of human error, making it ideal for large-scale manufacturing environments. On the other hand, the Semi-automated LDI System offers a balance between automation and manual control. While it incorporates automated features for critical steps in the imaging process, it still requires some level of human oversight and intervention. This system is suitable for medium-scale production where flexibility and adaptability are essential. The semi-automated system allows operators to make adjustments and fine-tune the process as needed, providing a good compromise between efficiency and control. It is particularly useful in scenarios where production volumes are not as high, but precision and quality are still paramount. The Manually LDI System, as the name suggests, relies heavily on human operation. This system is typically used for low-volume production or prototyping, where the focus is on customization and precision rather than speed. Operators have full control over the imaging process, allowing for meticulous adjustments and fine-tuning. While this system may not be as efficient as its automated counterparts, it offers unparalleled flexibility and control, making it ideal for specialized applications and small-scale production runs. The manually operated system is often used in research and development settings, where the ability to experiment and iterate quickly is crucial. Each of these systems plays a vital role in the IC substrate market, catering to different production needs and scales. The choice between a Full-Automatic, Semi-automated, or Manually LDI System depends on various factors, including production volume, required precision, and available resources. As the demand for advanced electronic devices continues to grow, the need for versatile and efficient LDW equipment becomes increasingly important. These systems enable manufacturers to produce high-quality IC substrates with the precision and reliability needed to meet the evolving demands of the electronics industry.
FC-BGA (ABF), FC-CSP, BGA/CSP, SiP and RF Modules, Others in the Global Laser Direct Writing (LDW) Equipment for IC Substrate Market:
Global Laser Direct Writing (LDW) Equipment for IC Substrate Market finds extensive usage in various applications, including FC-BGA (ABF), FC-CSP, BGA/CSP, SiP, and RF Modules, among others. FC-BGA (Flip Chip Ball Grid Array) and FC-CSP (Flip Chip Chip Scale Package) are advanced packaging technologies used in high-performance electronic devices. LDW equipment is crucial in these applications as it allows for the precise patterning of substrates, which is essential for the reliable performance of flip-chip packages. The ability to create fine and accurate patterns ensures that the electrical connections between the chip and the substrate are robust, leading to improved device performance and reliability. In the case of BGA (Ball Grid Array) and CSP (Chip Scale Package), LDW equipment is used to create the intricate patterns required for these packaging technologies. BGA and CSP are widely used in various electronic devices, including smartphones, tablets, and computers. The precision offered by LDW equipment ensures that the substrates used in these packages meet the stringent quality standards required for high-performance applications. The ability to produce high-quality substrates with minimal defects is crucial in maintaining the overall performance and reliability of the final electronic products. SiP (System in Package) and RF (Radio Frequency) Modules are other significant applications of LDW equipment. SiP technology involves integrating multiple electronic components into a single package, which requires precise patterning of the substrate to ensure proper functionality. LDW equipment enables the creation of complex patterns needed for SiP applications, allowing for the integration of various components such as processors, memory, and sensors into a compact package. Similarly, RF Modules, which are used in wireless communication devices, require precise patterning to ensure optimal performance. LDW equipment plays a vital role in producing the high-quality substrates needed for these modules, ensuring reliable and efficient wireless communication. Apart from these specific applications, LDW equipment is also used in other areas of the IC substrate market. This includes the production of substrates for various electronic components and devices, where precision and quality are paramount. The versatility of LDW equipment allows manufacturers to cater to a wide range of applications, meeting the diverse needs of the electronics industry. As the demand for advanced electronic devices continues to grow, the importance of LDW equipment in producing high-quality IC substrates becomes increasingly evident. The ability to create precise and reliable patterns on substrates is crucial in ensuring the overall performance and reliability of electronic devices, making LDW equipment an indispensable tool in the semiconductor manufacturing process.
Global Laser Direct Writing (LDW) Equipment for IC Substrate Market Outlook:
The global market for Laser Direct Writing (LDW) Equipment for IC Substrate was valued at approximately $33 million in 2023. Projections indicate that this market is expected to grow, reaching an estimated value of $48 million by the year 2030. This growth trajectory represents a compound annual growth rate (CAGR) of 5.3% over the forecast period from 2024 to 2030. The increasing demand for advanced electronic devices and the need for more efficient manufacturing processes are key drivers of this market growth. As the electronics industry continues to evolve, the role of LDW equipment in producing high-quality IC substrates becomes increasingly significant. The precision and flexibility offered by LDW technology make it an essential tool in the semiconductor manufacturing process, enabling the production of intricate and reliable patterns on substrates. This market outlook highlights the growing importance of LDW equipment in meeting the evolving demands of the electronics industry and underscores the potential for continued growth in this sector.
Report Metric | Details |
Report Name | Laser Direct Writing (LDW) Equipment for IC Substrate Market |
Accounted market size in 2023 | US$ 33 million |
Forecasted market size in 2030 | US$ 48 million |
CAGR | 5.3% |
Base Year | 2023 |
Forecasted years | 2024 - 2030 |
Segment by Type |
|
Segment by Application |
|
Production by Region |
|
Consumption by Region |
|
By Company | Orbotech (KLA), ADTEC, SCREEN, Chime Ball Technology, ORC Manufacturing, Circuit Fabology Microelectronics Equipment Co.,Ltd., TZTEK Company, Han's Laser, Jiangsu Yingsu IC Equipment |
Forecast units | USD million in value |
Report coverage | Revenue and volume forecast, company share, competitive landscape, growth factors and trends |