What is Global Wafer Heaters for Semiconductor Equipment Market?
The global Wafer Heaters for Semiconductor Equipment market is a specialized segment within the semiconductor industry that focuses on the production and distribution of wafer heaters. These heaters are essential components in semiconductor manufacturing equipment, playing a critical role in processes such as chemical vapor deposition (CVD), physical vapor deposition (PVD), atomic layer deposition (ALD), etching, and ashing. Wafer heaters ensure precise temperature control, which is crucial for the successful fabrication of semiconductor devices. The market for these heaters is driven by the increasing demand for semiconductors in various applications, including consumer electronics, automotive, and telecommunications. As technology advances, the need for more sophisticated and efficient wafer heaters continues to grow, making this market an integral part of the semiconductor manufacturing ecosystem.
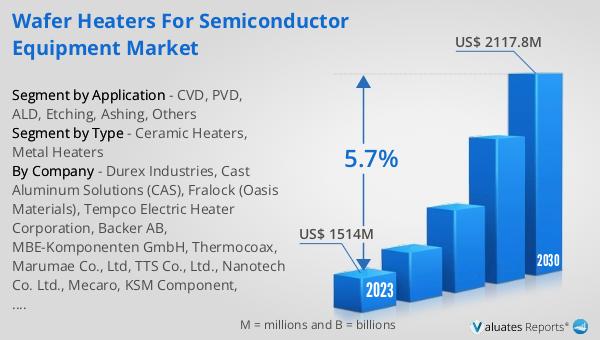
Ceramic Heaters, Metal Heaters in the Global Wafer Heaters for Semiconductor Equipment Market:
Ceramic heaters and metal heaters are two primary types of wafer heaters used in the semiconductor equipment market. Ceramic heaters are known for their excellent thermal conductivity, high-temperature stability, and resistance to thermal shock. They are typically made from materials such as aluminum nitride (AlN) or silicon carbide (SiC), which provide uniform heating and rapid thermal response. These properties make ceramic heaters ideal for applications that require precise temperature control and quick heating cycles, such as CVD and ALD processes. On the other hand, metal heaters are usually made from materials like stainless steel or Inconel, which offer durability and resistance to oxidation and corrosion. Metal heaters are often used in environments where mechanical strength and longevity are critical, such as in PVD and etching processes. Both types of heaters play a vital role in ensuring the efficiency and reliability of semiconductor manufacturing equipment. The choice between ceramic and metal heaters depends on the specific requirements of the application, including temperature range, thermal uniformity, and environmental conditions. As the semiconductor industry continues to evolve, the demand for advanced wafer heaters that can meet the stringent requirements of modern manufacturing processes is expected to increase.
CVD, PVD, ALD, Etching, Ashing, Others in the Global Wafer Heaters for Semiconductor Equipment Market:
Wafer heaters are extensively used in various semiconductor manufacturing processes, including CVD, PVD, ALD, etching, and ashing. In CVD, wafer heaters are crucial for maintaining the precise temperatures needed to deposit thin films of materials onto the wafer surface. This process is essential for creating high-quality semiconductor devices with uniform properties. In PVD, wafer heaters help in the physical deposition of materials onto the wafer through processes like sputtering and evaporation. The heaters ensure that the wafer remains at the optimal temperature for material adhesion and uniform coating. ALD is another process that relies heavily on wafer heaters. In ALD, thin films are deposited one atomic layer at a time, requiring extremely precise temperature control to achieve the desired film thickness and uniformity. Wafer heaters in ALD systems provide the necessary thermal stability to ensure consistent deposition rates and high-quality films. Etching processes, which involve the removal of material from the wafer surface to create patterns, also benefit from the use of wafer heaters. The heaters help maintain the wafer at the correct temperature to ensure precise etching and prevent damage to the wafer. Ashing, a process used to remove photoresist or other organic materials from the wafer surface, relies on wafer heaters to achieve the high temperatures needed for efficient removal. In all these processes, wafer heaters play a critical role in ensuring the quality and reliability of semiconductor devices.
Global Wafer Heaters for Semiconductor Equipment Market Outlook:
The global Wafer Heaters for Semiconductor Equipment market was valued at US$ 1514 million in 2023 and is anticipated to reach US$ 2117.8 million by 2030, witnessing a CAGR of 5.7% during the forecast period 2024-2030. According to SEMI, worldwide sales of semiconductor manufacturing equipment increased by 5% from $102.6 billion in 2021 to an all-time record of $107.6 billion in 2022. For the third consecutive year, China remained the largest semiconductor equipment market in 2022, despite a 5% slowdown in the pace of investments in the region year over year, accounting for $28.3 billion in billings. This growth in the semiconductor equipment market highlights the increasing demand for advanced wafer heaters, which are essential for the efficient and reliable operation of semiconductor manufacturing processes. As the industry continues to expand, the need for high-performance wafer heaters that can meet the stringent requirements of modern semiconductor fabrication will continue to drive market growth.
Report Metric | Details |
Report Name | Wafer Heaters for Semiconductor Equipment Market |
Accounted market size in 2023 | US$ 1514 million |
Forecasted market size in 2030 | US$ 2117.8 million |
CAGR | 5.7% |
Base Year | 2023 |
Forecasted years | 2024 - 2030 |
Segment by Type |
|
Segment by Application |
|
Production by Region |
|
Consumption by Region |
|
By Company | Durex Industries, Cast Aluminum Solutions (CAS), Fralock (Oasis Materials), Tempco Electric Heater Corporation, Backer AB, MBE-Komponenten GmbH, Thermocoax, Marumae Co., Ltd, TTS Co., Ltd., Nanotech Co. Ltd., Mecaro, KSM Component, CoorsTek, SemiXicon, NGK Insulators (NTK Ceratec), Kyocera, Shinko Electric Industries, MiCo Ceramics, 住友电气工业, Momentive Technologies, Shin-Etsu MicroSi, BACH Resistor Ceramics, Technetics Semi, Duratek Technology Co., Ltd., Sprint Precision Technologies Co., Ltd, Tolerance, Zhejiang Longji Lier Semiconductor Technology, Sanyue Semiconductor Technology, Suzhou KemaTek,Inc., KFMI, BoBoo, Shing Tai Cheng Ent. Co., Ltd., AK Tech Co.,Ltd |
Forecast units | USD million in value |
Report coverage | Revenue and volume forecast, company share, competitive landscape, growth factors and trends |