What is Global Ceramic Susceptors for Semiconductor Equipment Market?
The global Ceramic Susceptors for Semiconductor Equipment market is a specialized segment within the semiconductor industry that focuses on the production and utilization of ceramic susceptors. These susceptors are critical components used in semiconductor manufacturing equipment, particularly in processes that require precise temperature control and uniform heating. Ceramic susceptors are typically made from materials like silicon carbide (SiC), silicon (Si), and graphite, which are often coated with other materials to enhance their performance. These susceptors play a vital role in processes such as epitaxial growth, where a thin layer of semiconductor material is deposited onto a substrate, and single crystal growth, which is essential for producing high-quality semiconductor wafers. The market for ceramic susceptors is driven by the increasing demand for advanced semiconductor devices, which require highly controlled manufacturing environments to ensure the quality and performance of the final products. As the semiconductor industry continues to evolve, the need for more efficient and reliable susceptors is expected to grow, making this market an important area of focus for manufacturers and researchers alike.
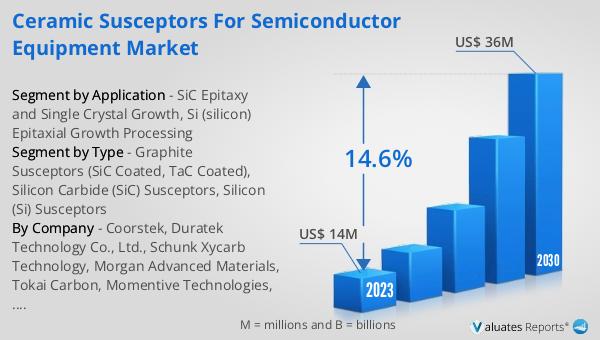
Graphite Susceptors (SiC Coated, TaC Coated), Silicon Carbide (SiC) Susceptors, Silicon (Si) Susceptors in the Global Ceramic Susceptors for Semiconductor Equipment Market:
Graphite susceptors, often coated with silicon carbide (SiC) or tantalum carbide (TaC), are widely used in the semiconductor industry due to their excellent thermal conductivity and stability at high temperatures. SiC-coated graphite susceptors are particularly valued for their ability to withstand extreme temperatures and corrosive environments, making them ideal for processes like chemical vapor deposition (CVD) and physical vapor deposition (PVD). TaC-coated graphite susceptors offer similar benefits but with enhanced resistance to chemical attack, which is crucial in certain semiconductor manufacturing processes. Silicon carbide (SiC) susceptors, on the other hand, are known for their high thermal conductivity, low thermal expansion, and excellent mechanical strength. These properties make SiC susceptors suitable for high-temperature applications and processes that require precise thermal management. Silicon (Si) susceptors are also used in the semiconductor industry, particularly in processes that involve silicon epitaxial growth. Si susceptors provide a stable and uniform heating environment, which is essential for producing high-quality silicon wafers. The choice of susceptor material depends on the specific requirements of the semiconductor manufacturing process, including temperature, chemical environment, and desired material properties. Each type of susceptor offers unique advantages and is selected based on its ability to meet the stringent demands of semiconductor production. As the semiconductor industry continues to advance, the development and optimization of susceptors will remain a critical area of research and innovation.
SiC Epitaxy and Single Crystal Growth, Si (silicon) Epitaxial Growth Processing in the Global Ceramic Susceptors for Semiconductor Equipment Market:
In the context of SiC epitaxy and single crystal growth, ceramic susceptors play a crucial role in ensuring the quality and consistency of the final semiconductor products. SiC epitaxy involves the deposition of a thin layer of silicon carbide onto a substrate, which is a critical step in the production of high-power and high-frequency electronic devices. Ceramic susceptors, particularly those made from SiC or SiC-coated graphite, provide the necessary thermal stability and uniform heating required for this process. The uniform heating ensures that the epitaxial layer is deposited evenly, resulting in a high-quality crystalline structure. Similarly, in single crystal growth, which is essential for producing semiconductor wafers with minimal defects, ceramic susceptors are used to maintain a stable and controlled thermal environment. This process often involves the use of high temperatures and precise thermal gradients, which ceramic susceptors can effectively manage. In Si epitaxial growth processing, silicon susceptors are commonly used due to their compatibility with silicon substrates and their ability to provide a uniform heating environment. This uniformity is crucial for achieving the desired thickness and quality of the epitaxial layer. Overall, the use of ceramic susceptors in these processes is vital for ensuring the performance and reliability of semiconductor devices, making them an indispensable component in the semiconductor manufacturing industry.
Global Ceramic Susceptors for Semiconductor Equipment Market Outlook:
The global Ceramic Susceptors for Semiconductor Equipment market was valued at US$ 14 million in 2023 and is anticipated to reach US$ 36 million by 2030, witnessing a CAGR of 14.6% during the forecast period 2024-2030. According to SEMI, worldwide sales of semiconductor manufacturing equipment increased 5% from $102.6 billion in 2021 to an all-time record of $107.6 billion in 2022. For the third consecutive year, China remained the largest semiconductor equipment market in 2022, despite a 5% slowdown in the pace of investments in the region year over year, accounting for $28.3 billion in billings. This growth in the semiconductor equipment market underscores the increasing demand for advanced manufacturing technologies, including ceramic susceptors, which are essential for producing high-quality semiconductor devices. The continued investment in semiconductor manufacturing infrastructure, particularly in key markets like China, highlights the importance of ceramic susceptors in supporting the industry's growth and innovation. As the semiconductor industry continues to expand, the demand for efficient and reliable susceptors is expected to rise, driving further advancements in this specialized market segment.
Report Metric | Details |
Report Name | Ceramic Susceptors for Semiconductor Equipment Market |
Accounted market size in 2023 | US$ 14 million |
Forecasted market size in 2030 | US$ 36 million |
CAGR | 14.6% |
Base Year | 2023 |
Forecasted years | 2024 - 2030 |
Segment by Type |
|
Segment by Application |
|
Production by Region |
|
Consumption by Region |
|
By Company | Coorstek, Duratek Technology Co., Ltd., Schunk Xycarb Technology, Morgan Advanced Materials, Tokai Carbon, Momentive Technologies, TOYO TANSO, SGL Carbon, Ningbo HIPER Technologies, Hunan Xingsheng, LIUFANG TECH, Shenzhen Zhicheng Semiconductor Materials |
Forecast units | USD million in value |
Report coverage | Revenue and volume forecast, company share, competitive landscape, growth factors and trends |