What is Global Yttria Thermal Spray Powders for Semiconductor Coatings Market?
The global Yttria Thermal Spray Powders for Semiconductor Coatings market is a specialized segment within the broader semiconductor industry. Yttria, or yttrium oxide, is a high-purity ceramic material known for its excellent thermal and chemical stability. These properties make it ideal for use in thermal spray coatings, which are applied to semiconductor manufacturing equipment to protect against wear, corrosion, and high temperatures. The market for these powders is driven by the increasing demand for semiconductors in various applications, including consumer electronics, automotive, and industrial sectors. As semiconductor devices become more advanced and miniaturized, the need for high-performance coatings to ensure the longevity and efficiency of manufacturing equipment becomes even more critical. This market is characterized by continuous innovation and development to meet the stringent requirements of the semiconductor industry.
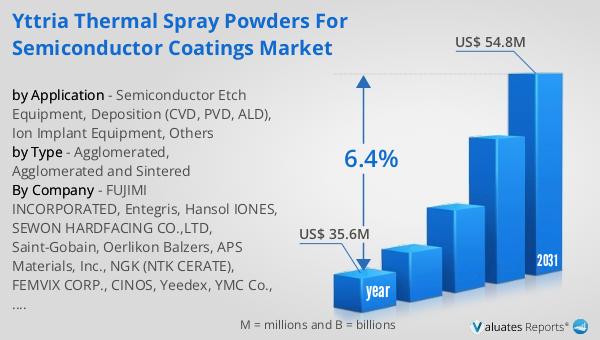
Agglomerated, Agglomerated and Sintered in the Global Yttria Thermal Spray Powders for Semiconductor Coatings Market:
Agglomerated and agglomerated and sintered yttria thermal spray powders are two primary types used in the semiconductor coatings market. Agglomerated powders are created by clustering fine particles together into larger, more manageable granules. This process enhances the flowability and consistency of the powder, making it easier to apply as a coating. These powders are typically used in applications where a uniform and smooth coating is essential. On the other hand, agglomerated and sintered powders undergo an additional sintering process, where the agglomerated particles are heated to a temperature below their melting point, causing them to bond together more firmly. This results in a denser and more durable coating, which is particularly beneficial in high-wear and high-temperature environments. The choice between agglomerated and agglomerated and sintered powders depends on the specific requirements of the application, such as the desired coating thickness, hardness, and thermal stability. Both types of powders play a crucial role in enhancing the performance and lifespan of semiconductor manufacturing equipment.
Semiconductor Etch Equipment, Deposition (CVD, PVD, ALD), Ion Implant Equipment, Others in the Global Yttria Thermal Spray Powders for Semiconductor Coatings Market:
The usage of global yttria thermal spray powders for semiconductor coatings spans several critical areas, including semiconductor etch equipment, deposition processes like Chemical Vapor Deposition (CVD), Physical Vapor Deposition (PVD), and Atomic Layer Deposition (ALD), ion implant equipment, and other specialized applications. In semiconductor etch equipment, yttria coatings are used to protect the internal components from the harsh chemical environments encountered during the etching process. These coatings help maintain the precision and efficiency of the etching process by preventing corrosion and wear. In deposition processes such as CVD, PVD, and ALD, yttria coatings are applied to the chamber walls and other components to protect them from the high temperatures and reactive gases used in these processes. This ensures the purity and quality of the deposited films, which is crucial for the performance of the semiconductor devices. Ion implant equipment, which is used to introduce dopants into semiconductor wafers, also benefits from yttria coatings. These coatings protect the equipment from the high-energy ions and the resulting wear and tear, thereby extending the equipment's lifespan and maintaining its performance. Other specialized applications of yttria thermal spray powders include protective coatings for wafer handling tools and other critical components in the semiconductor manufacturing process. These coatings help reduce particle contamination and improve the overall yield and reliability of the semiconductor devices.
Global Yttria Thermal Spray Powders for Semiconductor Coatings Market Outlook:
The global Yttria Thermal Spray Powders for Semiconductor Coatings market was valued at US$ 31 million in 2023 and is anticipated to reach US$ 49 million by 2030, witnessing a CAGR of 6.4% during the forecast period 2024-2030. According to SEMI, worldwide sales of semiconductor manufacturing equipment increased 5% from $102.6 billion in 2021 to an all-time record of $107.6 billion in 2022. For the third consecutive year, China remained the largest semiconductor equipment market in 2022, despite a 5% slowdown in the pace of investments in the region year over year, accounting for $28.3 billion in billings.
Report Metric | Details |
Report Name | Yttria Thermal Spray Powders for Semiconductor Coatings Market |
Accounted market size in 2023 | US$ 31 million |
Forecasted market size in 2030 | US$ 49 million |
CAGR | 6.4% |
Base Year | 2023 |
Forecasted years | 2024 - 2030 |
Segment by Type |
|
Segment by Application |
|
Production by Region |
|
Consumption by Region |
|
By Company | FUJIMI INCORPORATED, Entegris, Hansol IONES, SEWON HARDFACING CO.,LTD, Saint-Gobain, Oerlikon Balzers, APS Materials, Inc., NGK (NTK CERATE), FEMVIX CORP., CINOS, Yeedex, YMC Co., Ltd., Treibacher Industrie AG, Nano Research Elements, Coorstek, Shin-Etsu Rare Earths |
Forecast units | USD million in value |
Report coverage | Revenue and volume forecast, company share, competitive landscape, growth factors and trends |