What is Global Alumina-Carbon Brick Market?
The Global Alumina-Carbon Brick Market is a specialized segment within the broader refractory materials industry, focusing on the production and distribution of alumina-carbon bricks. These bricks are engineered to withstand extreme temperatures and harsh environments, making them essential in industries such as steelmaking, foundries, and other high-temperature applications. Alumina-carbon bricks are composed of alumina, carbon, and other additives, which provide them with excellent thermal shock resistance, high mechanical strength, and resistance to slag and erosion. The market for these bricks is driven by the demand from industries that require durable and reliable refractory materials to ensure the efficiency and longevity of their high-temperature processes. As industries continue to evolve and expand, the need for advanced refractory solutions like alumina-carbon bricks is expected to grow, further fueling the market's development. The global alumina-carbon brick market is characterized by a mix of established players and emerging companies, all striving to innovate and improve the performance of their products to meet the ever-changing demands of their customers. This dynamic market environment encourages continuous research and development, leading to the introduction of new and improved products that cater to the specific needs of various industrial applications.
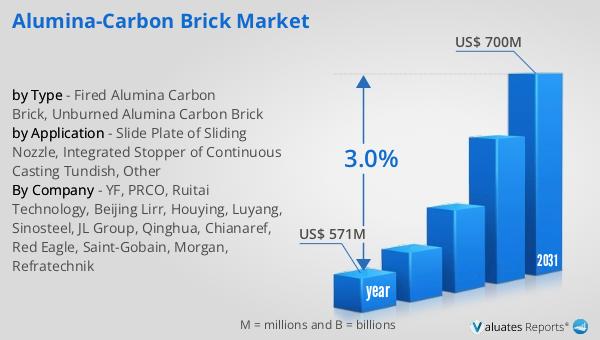
Fired Alumina Carbon Brick, Unburned Alumina Carbon Brick in the Global Alumina-Carbon Brick Market:
Fired alumina-carbon bricks and unburned alumina-carbon bricks are two primary types of products within the global alumina-carbon brick market, each with distinct characteristics and applications. Fired alumina-carbon bricks are manufactured through a process that involves mixing raw materials, forming the bricks, and then firing them at high temperatures. This firing process enhances the bricks' mechanical strength and thermal stability, making them suitable for use in environments where they are exposed to extreme heat and mechanical stress. These bricks are commonly used in the linings of steelmaking furnaces, ladles, and other high-temperature industrial equipment. The firing process also helps to reduce the porosity of the bricks, which improves their resistance to slag penetration and chemical attack, further extending their lifespan in demanding applications. On the other hand, unburned alumina-carbon bricks are produced without the high-temperature firing step, which results in a different set of properties. These bricks are typically formed by mixing raw materials with a binder, such as resin or pitch, and then allowing them to cure at room temperature. The absence of the firing process means that unburned alumina-carbon bricks generally have higher porosity and lower mechanical strength compared to their fired counterparts. However, they offer advantages in terms of cost and ease of production, making them an attractive option for certain applications where extreme thermal and mechanical stresses are not as prevalent. Unburned alumina-carbon bricks are often used in less demanding environments or as backup linings in conjunction with fired bricks to provide additional insulation and protection. Both fired and unburned alumina-carbon bricks play crucial roles in the global alumina-carbon brick market, catering to the diverse needs of industries that rely on refractory materials to maintain the efficiency and safety of their high-temperature processes. As the market continues to evolve, manufacturers are constantly exploring new formulations and production techniques to enhance the performance and cost-effectiveness of these bricks, ensuring that they remain a vital component of the industrial landscape.
Slide Plate of Sliding Nozzle, Integrated Stopper of Continuous Casting Tundish, Other in the Global Alumina-Carbon Brick Market:
The global alumina-carbon brick market finds its applications in various critical areas, including the slide plate of sliding nozzles, integrated stoppers of continuous casting tundishes, and other high-temperature industrial components. In the context of the slide plate of sliding nozzles, alumina-carbon bricks are used to construct the sliding mechanism that controls the flow of molten metal in steelmaking processes. The exceptional thermal shock resistance and mechanical strength of these bricks make them ideal for withstanding the rapid temperature changes and mechanical stresses encountered during the opening and closing of the nozzle. This ensures a smooth and controlled flow of molten metal, which is crucial for maintaining the quality and consistency of the final steel product. In the integrated stopper of continuous casting tundishes, alumina-carbon bricks play a vital role in regulating the flow of molten steel from the tundish to the mold. The bricks' resistance to thermal shock and erosion ensures that the stopper can effectively control the flow rate and prevent any unwanted interruptions or defects in the casting process. This is particularly important in continuous casting operations, where maintaining a steady and consistent flow of molten steel is essential for producing high-quality steel slabs or billets. Additionally, alumina-carbon bricks are used in other high-temperature industrial applications, such as linings for ladles, furnaces, and other equipment exposed to extreme heat and corrosive environments. Their ability to withstand harsh conditions and provide reliable performance makes them an indispensable component in industries that rely on high-temperature processes, such as steelmaking, foundries, and non-ferrous metal production. As the demand for high-quality refractory materials continues to grow, the global alumina-carbon brick market is expected to expand, driven by the need for advanced solutions that can meet the evolving requirements of these critical industrial applications.
Global Alumina-Carbon Brick Market Outlook:
In 2024, the global alumina-carbon brick market was valued at approximately $571 million. This market is anticipated to experience growth over the coming years, with projections indicating that it could reach a revised size of around $700 million by 2031. This growth trajectory represents a compound annual growth rate (CAGR) of 3.0% during the forecast period. The steady increase in market size reflects the rising demand for alumina-carbon bricks across various industries that require durable and efficient refractory materials. As industries such as steelmaking, foundries, and non-ferrous metal production continue to expand and modernize, the need for high-performance refractory solutions like alumina-carbon bricks is expected to grow. This demand is driven by the bricks' ability to withstand extreme temperatures, resist chemical attack, and provide reliable performance in harsh environments. The market's growth is also supported by ongoing research and development efforts aimed at enhancing the properties and cost-effectiveness of alumina-carbon bricks, ensuring that they remain a vital component in the industrial landscape. As a result, the global alumina-carbon brick market is poised for continued expansion, driven by the increasing need for advanced refractory materials in high-temperature applications.
Report Metric | Details |
Report Name | Alumina-Carbon Brick Market |
Accounted market size in year | US$ 571 million |
Forecasted market size in 2031 | US$ 700 million |
CAGR | 3.0% |
Base Year | year |
Forecasted years | 2025 - 2031 |
by Type |
|
by Application |
|
Production by Region |
|
Consumption by Region |
|
By Company | YF, PRCO, Ruitai Technology, Beijing Lirr, Houying, Luyang, Sinosteel, JL Group, Qinghua, Chianaref, Red Eagle, Saint-Gobain, Morgan, Refratechnik |
Forecast units | USD million in value |
Report coverage | Revenue and volume forecast, company share, competitive landscape, growth factors and trends |