What is Global Metal Injection Molding Parts (MIM Parts) Market?
The Global Metal Injection Molding Parts (MIM Parts) Market is a rapidly evolving sector that combines the versatility of plastic injection molding with the strength and integrity of metal. This market focuses on producing small, intricate metal parts using a process that involves mixing metal powders with a binder material to create a feedstock. This feedstock is then injected into a mold, forming the desired shape. After molding, the binder is removed, and the part is sintered to achieve its final density and strength. This method is particularly advantageous for producing complex geometries that would be challenging or costly to achieve through traditional manufacturing techniques. The MIM process is highly efficient, allowing for mass production of high-quality metal components with minimal waste. As industries continue to demand more precise and durable parts, the MIM market is poised for significant growth, driven by its ability to meet these needs with cost-effective solutions. The market's expansion is supported by advancements in material science and technology, which enhance the properties and applications of MIM parts across various sectors.
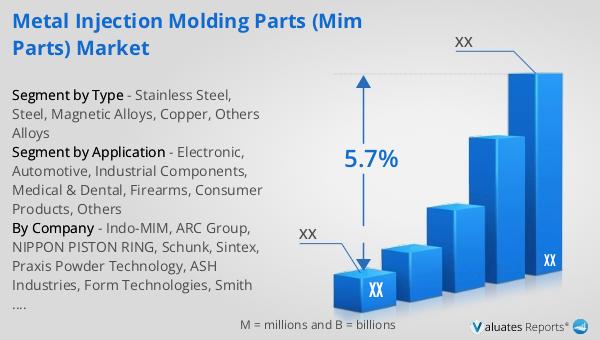
Stainless Steel, Steel, Magnetic Alloys, Copper, Others Alloys in the Global Metal Injection Molding Parts (MIM Parts) Market:
In the Global Metal Injection Molding Parts (MIM Parts) Market, a variety of materials are utilized, each offering unique properties that cater to specific applications. Stainless steel is one of the most commonly used materials due to its excellent corrosion resistance, strength, and aesthetic appeal. It is ideal for applications requiring durability and a high-quality finish, such as in the medical, automotive, and consumer electronics industries. Steel, in general, is favored for its strength and cost-effectiveness, making it suitable for a wide range of industrial components and automotive parts. Magnetic alloys are another critical material in the MIM market, used primarily in applications that require magnetic properties, such as sensors and electronic devices. These alloys are engineered to provide specific magnetic characteristics, enhancing the performance of the components in which they are used. Copper and its alloys are valued for their excellent electrical and thermal conductivity, making them indispensable in the electronics industry. They are often used in connectors, heat sinks, and other components where efficient heat dissipation is crucial. Other alloys, including titanium and nickel-based alloys, are also employed in the MIM process. Titanium alloys are known for their high strength-to-weight ratio and biocompatibility, making them suitable for aerospace and medical applications. Nickel-based alloys offer exceptional heat and corrosion resistance, ideal for high-temperature environments and demanding industrial applications. The choice of material in the MIM process is critical, as it directly impacts the performance, durability, and cost of the final product. Manufacturers must carefully consider the specific requirements of each application to select the most appropriate material, balancing factors such as mechanical properties, environmental resistance, and production costs. As the MIM market continues to grow, ongoing research and development in material science are expected to expand the range of available materials, further enhancing the capabilities and applications of MIM parts. This continuous innovation is essential for meeting the evolving demands of various industries and maintaining the competitiveness of the MIM market on a global scale.
Electronic, Automotive, Industrial Components, Medical & Dental, Firearms, Consumer Products, Others in the Global Metal Injection Molding Parts (MIM Parts) Market:
The Global Metal Injection Molding Parts (MIM Parts) Market finds extensive usage across several key industries, each benefiting from the unique advantages offered by the MIM process. In the electronics sector, MIM parts are used to produce small, intricate components such as connectors, housings, and heat sinks. The precision and repeatability of the MIM process ensure that these components meet the stringent quality standards required in electronic devices. In the automotive industry, MIM parts are utilized in the production of various components, including gears, turbocharger parts, and fuel system components. The ability to produce complex shapes with high strength and durability makes MIM an attractive option for automotive manufacturers looking to enhance performance and reduce weight. Industrial components also benefit from the MIM process, with applications ranging from machinery parts to tools and fasteners. The versatility of MIM allows for the production of components with specific mechanical properties tailored to the demands of industrial applications. In the medical and dental fields, MIM parts are used to manufacture surgical instruments, orthodontic brackets, and implantable devices. The biocompatibility and precision of MIM materials make them ideal for medical applications where safety and accuracy are paramount. The firearms industry also utilizes MIM parts for producing components such as triggers, hammers, and other small parts that require high strength and precision. In the consumer products sector, MIM is used to create components for items such as watches, eyeglasses, and kitchen appliances, where aesthetics and functionality are equally important. Other industries, including aerospace and defense, also leverage the benefits of MIM technology to produce high-performance components that meet rigorous standards. The widespread adoption of MIM parts across these diverse sectors underscores the versatility and efficiency of the MIM process, driving continued growth and innovation in the market. As industries continue to seek cost-effective solutions for producing high-quality metal components, the demand for MIM parts is expected to rise, further solidifying the market's position as a key player in the global manufacturing landscape.
Global Metal Injection Molding Parts (MIM Parts) Market Outlook:
In 2024, the global market size for Metal Injection Molding Parts (MIM Parts) was valued at approximately US$ 2,622 million. This market is projected to grow significantly, reaching an estimated value of around US$ 3,845 million by 2031. This growth is expected to occur at a compound annual growth rate (CAGR) of 5.7% during the forecast period from 2025 to 2031. The market's expansion is driven by the increasing demand for high-quality, cost-effective metal components across various industries. Notably, the top five manufacturers in the global MIM market hold a combined market share of about 20%, indicating a competitive landscape with significant opportunities for growth and innovation. As industries continue to evolve and demand more complex and durable components, the MIM market is well-positioned to meet these needs with its advanced manufacturing capabilities. The ongoing advancements in material science and technology are expected to further enhance the properties and applications of MIM parts, contributing to the market's robust growth trajectory. This positive outlook reflects the MIM market's potential to play a crucial role in the future of manufacturing, offering solutions that combine precision, efficiency, and sustainability.
Report Metric | Details |
Report Name | Metal Injection Molding Parts (MIM Parts) Market |
CAGR | 5.7% |
Segment by Type |
|
Segment by Application |
|
By Region |
|
By Company | Indo-MIM, ARC Group, NIPPON PISTON RING, Schunk, Sintex, Praxis Powder Technology, ASH Industries, Form Technologies, Smith Metal Products, CMG Technologies, MPP, AMT, Dou Yee Technologies, Shin Zu Shing, GIAN, Future High-tech, CN Innovations |
Forecast units | USD million in value |
Report coverage | Revenue and volume forecast, company share, competitive landscape, growth factors and trends |