What is Global Low Pressure Molding Adhesive Market?
The Global Low Pressure Molding Adhesive Market is a specialized segment within the broader adhesives industry, focusing on materials used for encapsulating and protecting electronic components. These adhesives are designed to operate under low pressure, making them ideal for sensitive applications where traditional high-pressure molding could damage delicate parts. The market is driven by the increasing demand for reliable and efficient encapsulation solutions in various industries, including electronics, automotive, and medical devices. Low pressure molding adhesives offer several advantages, such as excellent thermal stability, chemical resistance, and the ability to form a tight seal around components, protecting them from environmental factors like moisture and dust. As industries continue to innovate and develop more compact and complex electronic devices, the need for advanced adhesive solutions that can provide robust protection without compromising the integrity of the components is becoming increasingly critical. This market is characterized by continuous research and development efforts aimed at improving the performance and versatility of these adhesives to meet the evolving needs of different applications. The growth of this market is also supported by the rising trend of miniaturization in electronics, which requires more precise and reliable encapsulation methods.
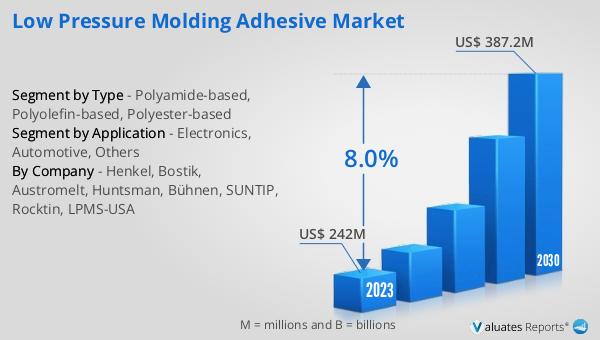
TPU, PO in the Global Low Pressure Molding Adhesive Market:
Thermoplastic Polyurethane (TPU) and Polyolefin (PO) are two key materials used in the Global Low Pressure Molding Adhesive Market, each offering unique properties that cater to specific application needs. TPU is known for its flexibility, durability, and resistance to abrasion, making it an excellent choice for applications that require a high degree of mechanical resilience. It is widely used in the automotive and consumer electronics industries, where components are often subjected to mechanical stress and environmental exposure. TPU-based adhesives provide a strong bond and can withstand significant temperature variations, which is crucial for automotive applications where components are exposed to both high and low temperatures. On the other hand, Polyolefin (PO) adhesives are valued for their excellent chemical resistance and low moisture absorption, making them ideal for applications in harsh environments. PO adhesives are commonly used in the medical device industry, where maintaining the integrity of the encapsulated components is critical for device performance and patient safety. These adhesives provide a reliable seal that protects sensitive components from moisture and other environmental factors, ensuring the longevity and reliability of the devices. The choice between TPU and PO adhesives often depends on the specific requirements of the application, such as the need for flexibility, chemical resistance, or thermal stability. In the consumer electronics industry, both TPU and PO adhesives are used to protect delicate components from damage during manufacturing and throughout the product's lifecycle. As electronic devices become more compact and feature-rich, the demand for adhesives that can provide robust protection without adding significant weight or bulk is increasing. TPU and PO adhesives offer the necessary properties to meet these demands, making them essential materials in the low pressure molding adhesive market. The versatility of these materials allows manufacturers to tailor their adhesive solutions to the specific needs of their applications, ensuring optimal performance and reliability. As the market continues to grow, ongoing research and development efforts are focused on enhancing the properties of TPU and PO adhesives to meet the evolving needs of various industries. This includes improving their thermal stability, chemical resistance, and mechanical properties to ensure they can withstand the increasingly demanding conditions of modern applications. The development of new formulations and technologies is expected to further expand the capabilities of TPU and PO adhesives, making them even more integral to the success of the Global Low Pressure Molding Adhesive Market.
Consumer electronics, Automotive, Medical Devices, Other in the Global Low Pressure Molding Adhesive Market:
The Global Low Pressure Molding Adhesive Market finds extensive usage across various sectors, including consumer electronics, automotive, medical devices, and others, each with unique requirements and challenges. In the consumer electronics industry, these adhesives are crucial for protecting sensitive components such as circuit boards, connectors, and sensors from environmental factors like moisture, dust, and mechanical stress. As electronic devices become more compact and feature-rich, the need for reliable encapsulation solutions that can provide robust protection without adding significant weight or bulk is increasing. Low pressure molding adhesives offer the necessary properties to meet these demands, ensuring the longevity and reliability of electronic products. In the automotive industry, low pressure molding adhesives are used to protect electronic components such as sensors, control units, and connectors from harsh environmental conditions, including temperature fluctuations, vibration, and exposure to chemicals. These adhesives provide a strong bond and excellent thermal stability, ensuring the components remain secure and functional throughout the vehicle's lifecycle. The medical device industry also relies heavily on low pressure molding adhesives to encapsulate and protect sensitive components from moisture and other environmental factors. These adhesives are used in a wide range of medical devices, including diagnostic equipment, monitoring devices, and implantable devices, where maintaining the integrity of the encapsulated components is critical for device performance and patient safety. The ability of these adhesives to provide a reliable seal that protects sensitive components from environmental factors is essential for ensuring the longevity and reliability of medical devices. In addition to these industries, low pressure molding adhesives are also used in other applications, such as telecommunications, aerospace, and industrial equipment, where reliable encapsulation solutions are needed to protect sensitive components from environmental factors. The versatility of these adhesives allows manufacturers to tailor their solutions to the specific needs of their applications, ensuring optimal performance and reliability. As the market continues to grow, ongoing research and development efforts are focused on enhancing the properties of low pressure molding adhesives to meet the evolving needs of various industries. This includes improving their thermal stability, chemical resistance, and mechanical properties to ensure they can withstand the increasingly demanding conditions of modern applications. The development of new formulations and technologies is expected to further expand the capabilities of low pressure molding adhesives, making them even more integral to the success of various industries.
Global Low Pressure Molding Adhesive Market Outlook:
The global market for Low Pressure Molding Adhesive was valued at $267 million in 2024 and is anticipated to grow significantly, reaching an estimated size of $455 million by 2031. This growth represents a compound annual growth rate (CAGR) of 8.0% over the forecast period. The market's expansion is driven by the increasing demand for reliable and efficient encapsulation solutions across various industries, including electronics, automotive, and medical devices. In 2022, the share of major manufacturers in this market exceeded 83%, highlighting the dominance of key players in driving innovation and meeting the evolving needs of different applications. The significant market share held by these manufacturers underscores their ability to provide high-quality adhesive solutions that cater to the specific requirements of various industries. As the market continues to grow, these manufacturers are expected to play a crucial role in shaping the future of the low pressure molding adhesive industry through ongoing research and development efforts aimed at enhancing the performance and versatility of their products. The increasing trend of miniaturization in electronics and the growing demand for advanced adhesive solutions that can provide robust protection without compromising the integrity of components are expected to further drive the market's growth. As industries continue to innovate and develop more compact and complex electronic devices, the need for advanced adhesive solutions that can provide robust protection without compromising the integrity of the components is becoming increasingly critical. This market is characterized by continuous research and development efforts aimed at improving the performance and versatility of these adhesives to meet the evolving needs of different applications. The growth of this market is also supported by the rising trend of miniaturization in electronics, which requires more precise and reliable encapsulation methods.
Report Metric | Details |
Report Name | Low Pressure Molding Adhesive Market |
Accounted market size in year | US$ 267 million |
Forecasted market size in 2031 | US$ 455 million |
CAGR | 8.0% |
Base Year | year |
Forecasted years | 2025 - 2031 |
by Type |
|
by Application |
|
Production by Region |
|
Consumption by Region |
|
By Company | Henkel, Bostik, Huntsman, SUNTIP, Liri New Chemical Materials, Bühnen, Darbond, KY Chemical |
Forecast units | USD million in value |
Report coverage | Revenue and volume forecast, company share, competitive landscape, growth factors and trends |