What is Laser Plastic Welding Equipment - Global Market?
Laser plastic welding equipment is a specialized technology that utilizes laser energy to fuse plastic components together. This process is gaining traction globally due to its precision, efficiency, and ability to create strong, clean welds without the need for additional materials or adhesives. The global market for laser plastic welding equipment was valued at approximately US$ 290 million in 2023. It is projected to grow to a revised size of US$ 436.1 million by 2030, reflecting a compound annual growth rate (CAGR) of 6.0% during the forecast period from 2024 to 2030. This growth is driven by increasing demand across various industries such as automotive, electronics, and medical devices, where the need for reliable and high-quality plastic joining solutions is paramount. The technology's ability to provide precise control over the welding process, coupled with its adaptability to different plastic materials and complex geometries, makes it an attractive option for manufacturers looking to enhance product quality and production efficiency. As industries continue to innovate and seek sustainable manufacturing solutions, laser plastic welding equipment is poised to play a crucial role in meeting these evolving needs.
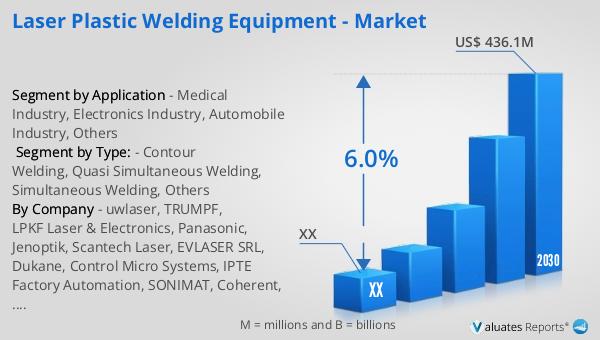
Contour Welding, Quasi Simultaneous Welding, Simultaneous Welding, Others in the Laser Plastic Welding Equipment - Global Market:
Laser plastic welding encompasses several techniques, each offering unique advantages and applications. Contour welding is one such method, where a laser beam follows a predefined path along the joint line of the plastic parts. This technique is particularly beneficial for welding complex shapes and geometries, as it allows for precise control over the weld path. The laser beam's movement can be adjusted to accommodate intricate designs, making contour welding ideal for applications requiring high precision and aesthetic appeal. Quasi-simultaneous welding, on the other hand, involves rapidly moving the laser beam over the entire weld seam multiple times. This method ensures uniform heat distribution and minimizes the risk of thermal distortion, making it suitable for welding large or irregularly shaped components. By rapidly scanning the weld area, quasi-simultaneous welding achieves a consistent and strong bond, even in challenging applications. Simultaneous welding takes a different approach by using multiple laser beams to heat the entire weld seam simultaneously. This technique is highly efficient and reduces cycle times, making it ideal for high-volume production environments. Simultaneous welding is often used in applications where speed and efficiency are critical, such as in the automotive industry. Other laser plastic welding methods include mask welding and through-transmission welding. Mask welding involves using a mask to selectively expose certain areas of the plastic to the laser beam, allowing for precise control over the weld pattern. This technique is useful for applications requiring intricate designs or patterns. Through-transmission welding, on the other hand, involves passing the laser beam through one of the plastic parts to reach the joint interface. This method is effective for welding transparent or translucent plastics, as it allows the laser energy to penetrate the material and create a strong bond. Each of these laser plastic welding techniques offers distinct advantages and can be tailored to meet specific application requirements. As industries continue to demand more efficient and reliable plastic joining solutions, the versatility and adaptability of laser plastic welding make it an increasingly popular choice for manufacturers worldwide.
Medical Industry, Electronics Industry, Automobile Industry, Others in the Laser Plastic Welding Equipment - Global Market:
Laser plastic welding equipment finds extensive use across various industries, each benefiting from its unique capabilities. In the medical industry, the precision and cleanliness of laser plastic welding are paramount. Medical devices often require sterile and reliable joints, and laser welding provides a non-contact method that minimizes contamination risks. This technology is used to assemble components such as fluid containers, filters, and diagnostic devices, where maintaining the integrity of the weld is crucial for patient safety. In the electronics industry, laser plastic welding is employed to join delicate components without causing thermal damage. The ability to precisely control the heat input ensures that sensitive electronic parts remain unharmed during the welding process. This makes laser welding ideal for assembling components like sensors, connectors, and housings, where precision and reliability are essential. The automotive industry also benefits significantly from laser plastic welding equipment. As vehicles become more complex and lightweight materials are increasingly used, the need for strong and reliable plastic joints grows. Laser welding provides the strength and durability required for components such as fuel tanks, lighting systems, and interior parts. The technology's ability to create aesthetically pleasing welds without additional finishing processes is an added advantage in the automotive sector. Beyond these industries, laser plastic welding is also utilized in areas such as consumer goods, packaging, and textiles. In consumer goods, the technology is used to assemble products like household appliances and toys, where durability and appearance are important. In packaging, laser welding ensures airtight seals for products such as food containers and medical packaging, enhancing product safety and shelf life. In the textile industry, laser welding is used to join synthetic fabrics, providing strong and flexible seams for products like outdoor gear and sportswear. The versatility and adaptability of laser plastic welding equipment make it a valuable tool across a wide range of applications, driving its adoption in diverse industries worldwide.
Laser Plastic Welding Equipment - Global Market Outlook:
The global market for laser plastic welding equipment was valued at approximately US$ 290 million in 2023, with projections indicating a growth to US$ 436.1 million by 2030. This represents a compound annual growth rate (CAGR) of 6.0% during the forecast period from 2024 to 2030. Laser plastic welding equipment is a cutting-edge technology that employs laser energy to join plastic parts seamlessly. This method is gaining popularity due to its precision, efficiency, and ability to produce strong, clean welds without the need for additional materials or adhesives. The increasing demand for reliable and high-quality plastic joining solutions across various industries, such as automotive, electronics, and medical devices, is a significant driver of this market growth. The technology's capability to provide precise control over the welding process, along with its adaptability to different plastic materials and complex geometries, makes it an attractive option for manufacturers aiming to enhance product quality and production efficiency. As industries continue to innovate and seek sustainable manufacturing solutions, laser plastic welding equipment is poised to play a crucial role in meeting these evolving needs. The market's expansion is further supported by advancements in laser technology, which continue to improve the efficiency and effectiveness of plastic welding processes.
Report Metric | Details |
Report Name | Laser Plastic Welding Equipment - Market |
Forecasted market size in 2030 | US$ 436.1 million |
CAGR | 6.0% |
Forecasted years | 2024 - 2030 |
Segment by Type: |
|
Segment by Application |
|
By Region |
|
By Company | uwlaser, TRUMPF, LPKF Laser & Electronics, Panasonic, Jenoptik, Scantech Laser, EVLASER SRL, Dukane, Control Micro Systems, IPTE Factory Automation, SONIMAT, Coherent, Emerson, Nippon Avionics, bielomatik, Leister Technologies |
Forecast units | USD million in value |
Report coverage | Revenue and volume forecast, company share, competitive landscape, growth factors and trends |