What is New Energy Vehicles Aluminum Casting - Global Market?
New Energy Vehicles Aluminum Casting refers to the process of creating aluminum components specifically for new energy vehicles (NEVs), which include electric and hybrid vehicles. This market is gaining traction globally due to the increasing demand for lightweight materials that enhance vehicle efficiency and performance. Aluminum casting is favored in the automotive industry because it offers a combination of strength, durability, and lightweight properties, which are crucial for improving the range and efficiency of NEVs. The global market for aluminum casting in NEVs is expanding as manufacturers seek to reduce vehicle weight and improve energy efficiency, thereby meeting stringent environmental regulations and consumer demand for sustainable transportation solutions. This market encompasses various casting methods, including die casting, permanent mold casting, and sand casting, each offering unique benefits and applications in the production of NEV components. As the automotive industry continues to shift towards electrification, the demand for aluminum casting in NEVs is expected to grow, driven by advancements in casting technologies and the increasing adoption of electric vehicles worldwide.
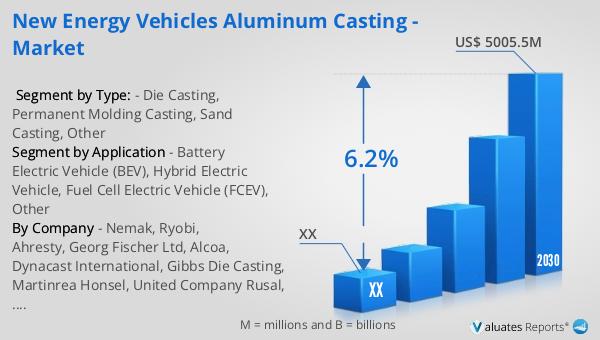
Die Casting, Permanent Molding Casting, Sand Casting, Other in the New Energy Vehicles Aluminum Casting - Global Market:
Die casting is a popular method in the New Energy Vehicles Aluminum Casting market due to its ability to produce high-precision and complex components with excellent surface finish and dimensional accuracy. This process involves forcing molten aluminum into a mold cavity under high pressure, allowing for rapid production of parts with consistent quality. Die casting is particularly suitable for producing components such as engine blocks, transmission cases, and structural parts in NEVs, where precision and strength are paramount. The process is highly efficient, reducing material waste and production time, which is crucial for meeting the growing demand for NEVs. Permanent mold casting, on the other hand, involves pouring molten aluminum into a reusable mold, typically made of metal. This method is ideal for producing medium to large-sized components with a good balance of mechanical properties and surface finish. Permanent mold casting is often used for manufacturing parts like wheels, suspension components, and other structural elements in NEVs. It offers advantages such as improved mechanical properties and reduced porosity compared to sand casting. Sand casting, a more traditional method, involves creating a mold from a sand mixture and pouring molten aluminum into the cavity. This process is versatile and cost-effective, making it suitable for producing large and complex components that do not require high precision. Sand casting is commonly used for manufacturing parts like battery housings, motor casings, and other non-critical components in NEVs. Despite its lower precision compared to die casting, sand casting offers flexibility in design and material selection, making it a valuable option for certain applications. Other casting methods, such as investment casting and centrifugal casting, are also used in the NEV aluminum casting market, albeit to a lesser extent. Investment casting, also known as lost-wax casting, is used for producing intricate and detailed components with excellent surface finish. This method is suitable for small to medium-sized parts that require high precision and complexity. Centrifugal casting, on the other hand, involves pouring molten aluminum into a rotating mold, allowing for the production of cylindrical components with uniform density and mechanical properties. This method is often used for manufacturing parts like bushings, bearings, and other rotational components in NEVs. Each casting method offers unique advantages and is selected based on the specific requirements of the component being produced, such as size, complexity, and mechanical properties. As the NEV market continues to evolve, advancements in casting technologies and materials are expected to further enhance the capabilities and applications of aluminum casting in the automotive industry.
Battery Electric Vehicle (BEV), Hybrid Electric Vehicle, Fuel Cell Electric Vehicle (FCEV), Other in the New Energy Vehicles Aluminum Casting - Global Market:
The usage of New Energy Vehicles Aluminum Casting in Battery Electric Vehicles (BEVs) is primarily focused on reducing vehicle weight to enhance energy efficiency and extend driving range. Aluminum components, such as battery housings, motor casings, and structural parts, are increasingly being used in BEVs to achieve these goals. The lightweight nature of aluminum helps to offset the weight of heavy battery packs, improving overall vehicle performance and efficiency. In Hybrid Electric Vehicles (HEVs), aluminum casting is used to produce components that require a balance of strength and weight reduction. Aluminum parts, such as engine blocks, transmission cases, and suspension components, are commonly used in HEVs to improve fuel efficiency and reduce emissions. The use of aluminum in these vehicles helps to optimize the performance of both the internal combustion engine and the electric motor, providing a seamless driving experience. Fuel Cell Electric Vehicles (FCEVs) also benefit from aluminum casting, particularly in the production of lightweight and durable components that can withstand the harsh operating conditions of fuel cells. Aluminum is used to manufacture parts such as fuel cell stacks, hydrogen storage tanks, and other structural components, contributing to the overall efficiency and performance of FCEVs. The lightweight properties of aluminum help to improve the vehicle's range and reduce energy consumption, making it an ideal material for FCEVs. In addition to these specific vehicle types, aluminum casting is also used in other areas of the NEV market, such as electric buses, trucks, and motorcycles. The versatility and adaptability of aluminum casting make it a valuable solution for a wide range of applications in the NEV market, supporting the industry's transition towards sustainable and efficient transportation solutions. As the demand for NEVs continues to grow, the usage of aluminum casting is expected to expand, driven by advancements in casting technologies and the increasing adoption of electric and hybrid vehicles worldwide.
New Energy Vehicles Aluminum Casting - Global Market Outlook:
The global market for New Energy Vehicles Aluminum Casting was valued at approximately $3,247.7 million in 2023. It is projected to grow to a revised size of $5,005.5 million by 2030, reflecting a compound annual growth rate (CAGR) of 6.2% during the forecast period from 2024 to 2030. Currently, over 90% of the world's automobiles are concentrated in Asia, Europe, and North America. Among these regions, Asia leads with 56% of global automobile production, followed by Europe at 20%, and North America at 16%. This distribution highlights the significant role these regions play in the automotive industry, particularly in the production and adoption of new energy vehicles. The increasing focus on reducing carbon emissions and enhancing fuel efficiency is driving the demand for lightweight materials like aluminum in vehicle manufacturing. As a result, the aluminum casting market for NEVs is poised for substantial growth, supported by technological advancements and the rising popularity of electric and hybrid vehicles. The market's expansion is further fueled by government initiatives and policies promoting the adoption of sustainable transportation solutions, making aluminum casting a critical component in the future of the automotive industry.
Report Metric | Details |
Report Name | New Energy Vehicles Aluminum Casting - Market |
Forecasted market size in 2030 | US$ 5005.5 million |
CAGR | 6.2% |
Forecasted years | 2024 - 2030 |
Segment by Type: |
|
Segment by Application |
|
By Region |
|
By Company | Nemak, Ryobi, Ahresty, Georg Fischer Ltd, Alcoa, Dynacast International, Gibbs Die Casting, Martinrea Honsel, United Company Rusal, Rockman Industries, Endurance, LTH, China Hongqiao, Guangdong Hongtu, Hongte, Wencan |
Forecast units | USD million in value |
Report coverage | Revenue and volume forecast, company share, competitive landscape, growth factors and trends |