What is Global Protective Coating for Semiconductor Fabrication Equipment Market?
The global Protective Coating for Semiconductor Fabrication Equipment market is a specialized segment within the semiconductor industry that focuses on providing protective coatings for equipment used in semiconductor fabrication. These coatings are essential for protecting the delicate and expensive machinery involved in the semiconductor manufacturing process from wear, corrosion, and contamination. The market for these protective coatings is driven by the increasing demand for semiconductors in various applications such as consumer electronics, automotive, and industrial sectors. As semiconductor technology advances, the need for more sophisticated and durable protective coatings also rises. These coatings not only extend the lifespan of the equipment but also enhance their performance and reliability, thereby reducing downtime and maintenance costs. The market is characterized by continuous innovation and development of new materials and coating techniques to meet the evolving needs of the semiconductor industry.
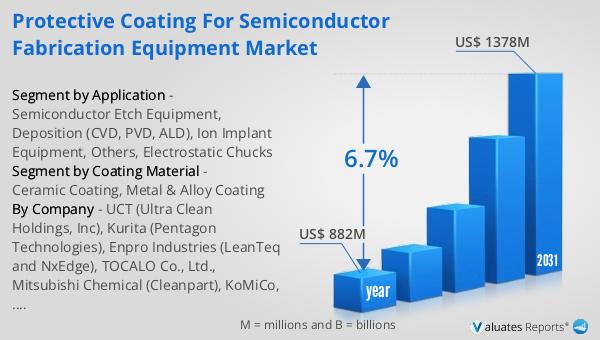
in the Global Protective Coating for Semiconductor Fabrication Equipment Market:
In the Global Protective Coating for Semiconductor Fabrication Equipment Market, various types of coatings are used by different customers based on their specific requirements. One of the most common types is the anti-corrosion coating, which is designed to protect equipment from the harsh chemicals and gases used in semiconductor fabrication. These coatings are typically made from materials like fluoropolymers, which offer excellent resistance to corrosion and chemical attack. Another popular type is the wear-resistant coating, which is used to protect equipment from mechanical wear and tear. These coatings are often made from hard materials like ceramics or diamond-like carbon, which provide a durable and long-lasting protective layer. Additionally, there are anti-contamination coatings, which are used to prevent the buildup of particles and other contaminants on the equipment. These coatings are usually made from materials that are easy to clean and maintain, such as silicone or Teflon. Furthermore, there are thermal barrier coatings, which are used to protect equipment from high temperatures. These coatings are typically made from materials like zirconia or alumina, which have excellent thermal insulation properties. Each type of coating has its own unique set of properties and benefits, and the choice of coating depends on the specific needs and requirements of the customer. For example, a customer who operates in a highly corrosive environment may opt for an anti-corrosion coating, while a customer who deals with high temperatures may choose a thermal barrier coating. The market for these protective coatings is highly competitive, with numerous companies offering a wide range of products to meet the diverse needs of the semiconductor industry. Companies are constantly investing in research and development to create new and improved coatings that offer better performance and durability. This has led to the development of advanced coatings that can withstand extreme conditions and provide superior protection for semiconductor fabrication equipment. Overall, the Global Protective Coating for Semiconductor Fabrication Equipment Market is a dynamic and rapidly evolving market, driven by the continuous advancements in semiconductor technology and the increasing demand for high-performance protective coatings.
Semiconductor Etch Equipment, Deposition (CVD, PVD, ALD), Ion Implant Equipment, Others, Electrostatic Chucks in the Global Protective Coating for Semiconductor Fabrication Equipment Market:
The usage of Global Protective Coating for Semiconductor Fabrication Equipment Market spans several critical areas, including Semiconductor Etch Equipment, Deposition (CVD, PVD, ALD), Ion Implant Equipment, Others, and Electrostatic Chucks. In Semiconductor Etch Equipment, protective coatings are essential for shielding the equipment from the aggressive chemicals and plasma used in the etching process. These coatings help to prevent corrosion and wear, ensuring the longevity and reliability of the equipment. In the Deposition processes such as Chemical Vapor Deposition (CVD), Physical Vapor Deposition (PVD), and Atomic Layer Deposition (ALD), protective coatings play a crucial role in maintaining the integrity of the equipment. These processes involve high temperatures and reactive gases, which can cause significant damage to the equipment if not properly protected. The coatings used in these applications are typically made from materials that can withstand high temperatures and resist chemical attack. In Ion Implant Equipment, protective coatings are used to protect the equipment from the high-energy ions that are implanted into the semiconductor wafers. These coatings help to prevent erosion and contamination, ensuring the accuracy and precision of the ion implantation process. Other areas where protective coatings are used include cleaning and maintenance equipment, where they help to prevent the buildup of contaminants and reduce the frequency of maintenance. Electrostatic Chucks, which are used to hold semiconductor wafers in place during processing, also benefit from protective coatings. These coatings help to prevent wear and tear on the chucks, ensuring a secure and stable hold on the wafers. Overall, the usage of protective coatings in these areas is critical for maintaining the performance and reliability of semiconductor fabrication equipment, reducing downtime, and minimizing maintenance costs.
Global Protective Coating for Semiconductor Fabrication Equipment Market Outlook:
The global Protective Coating for Semiconductor Fabrication Equipment market was valued at US$ 766 million in 2023 and is anticipated to reach US$ 1217.1 million by 2030, witnessing a CAGR of 7.0% during the forecast period 2024-2030. According to SEMI, worldwide sales of semiconductor manufacturing equipment increased 5% from $102.6 billion in 2021 to an all-time record of $107.6 billion in 2022. For the third consecutive year, China remained the largest semiconductor equipment market in 2022, despite a 5% slowdown in the pace of investments in the region year over year, accounting for $28.3 billion in billings. This growth in the semiconductor equipment market highlights the increasing demand for protective coatings, as manufacturers seek to enhance the durability and performance of their equipment. The continuous advancements in semiconductor technology and the growing need for high-performance protective coatings are expected to drive the market's growth in the coming years.
Report Metric | Details |
Report Name | Protective Coating for Semiconductor Fabrication Equipment Market |
Accounted market size in 2023 | US$ 766 million |
Forecasted market size in 2030 | US$ 1217.1 million |
CAGR | 7.0% |
Base Year | 2023 |
Forecasted years | 2024 - 2030 |
Segment by Coating Material |
|
Segment by Application |
|
By Region |
|
By Company | UCT (Ultra Clean Holdings, Inc), Pentagon Technologies, Enpro Industries, TOCALO Co., Ltd., Mitsubishi Chemical (Cleanpart), KoMiCo, Cinos, Hansol IONES, WONIK QnC, DFtech, TOPWINTECH, FEMVIX, SEWON HARDFACING CO.,LTD, Frontken Corporation Berhad, Value Engineering Co., Ltd, KERTZ HIGH TECH, Hung Jie Technology Corporation, Oerlikon Balzers, Beneq, APS Materials, Inc., SilcoTek, Alumiplate, Alcadyne, ASSET Solutions, Inc., Jiangsu Kaiweitesi Semiconductor Technology Co., Ltd., HCUT Co., Ltd, Ferrotec (Anhui) Technology Development Co., Ltd, Shanghai Companion |
Forecast units | USD million in value |
Report coverage | Revenue and volume forecast, company share, competitive landscape, growth factors and trends |