What is Global Chemical Mechanical Polishing (CMP) Diamond Pad Conditioner Market?
The Global Chemical Mechanical Polishing (CMP) Diamond Pad Conditioner Market is a specialized segment within the semiconductor and electronics manufacturing industry. CMP is a critical process used to smooth and flatten surfaces at the microscopic level, essential for producing integrated circuits and other electronic components. Diamond pad conditioners are tools used in this process to maintain the effectiveness of polishing pads, ensuring consistent performance and longevity. These conditioners are embedded with diamond particles, which provide the necessary abrasiveness to keep the polishing pads in optimal condition. The market for these diamond pad conditioners is driven by the increasing demand for advanced electronic devices, which require precise and efficient manufacturing processes. As technology continues to evolve, the need for high-quality CMP processes becomes even more crucial, thereby fueling the demand for diamond pad conditioners. The market is characterized by continuous innovation, with manufacturers striving to develop more efficient and durable products to meet the growing needs of the semiconductor industry. The global reach of this market highlights its importance in the broader context of technological advancement and electronic manufacturing.
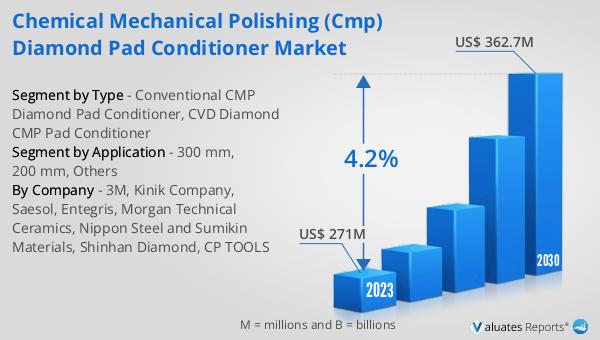
Conventional CMP Diamond Pad Conditioner, CVD Diamond CMP Pad Conditioner in the Global Chemical Mechanical Polishing (CMP) Diamond Pad Conditioner Market:
In the realm of the Global Chemical Mechanical Polishing (CMP) Diamond Pad Conditioner Market, two primary types of conditioners are prevalent: Conventional CMP Diamond Pad Conditioners and Chemical Vapor Deposition (CVD) Diamond CMP Pad Conditioners. Conventional CMP Diamond Pad Conditioners are typically made by embedding diamond particles onto a substrate using traditional methods. These conditioners are known for their reliability and cost-effectiveness, making them a popular choice for many manufacturers. They are designed to provide consistent performance, ensuring that the polishing pads remain effective over extended periods. However, they may require more frequent replacement compared to their CVD counterparts due to wear and tear. On the other hand, CVD Diamond CMP Pad Conditioners are produced using a more advanced technique known as chemical vapor deposition. This process involves depositing diamond films onto a substrate, resulting in a more uniform and durable product. CVD diamond conditioners are highly valued for their superior hardness and longevity, which translates to less frequent replacements and lower long-term costs. They are particularly suited for high-precision applications where consistency and durability are paramount. The choice between conventional and CVD diamond conditioners often depends on the specific requirements of the manufacturing process, including factors such as cost, precision, and the expected lifespan of the conditioner. As the semiconductor industry continues to advance, the demand for both types of diamond pad conditioners is expected to grow, driven by the need for more efficient and reliable CMP processes. Manufacturers are continually innovating to improve the performance and cost-effectiveness of these products, ensuring they meet the evolving needs of the market. The competition between conventional and CVD diamond conditioners is a testament to the dynamic nature of the CMP diamond pad conditioner market, where technological advancements and customer demands drive continuous improvement and innovation.
300 mm, 200 mm, Others in the Global Chemical Mechanical Polishing (CMP) Diamond Pad Conditioner Market:
The usage of Global Chemical Mechanical Polishing (CMP) Diamond Pad Conditioner Market is particularly significant in the context of different wafer sizes, namely 300 mm, 200 mm, and others. The 300 mm wafer size is the most prevalent in modern semiconductor manufacturing, as it allows for the production of more chips per wafer, thereby increasing efficiency and reducing costs. CMP diamond pad conditioners play a crucial role in maintaining the quality and consistency of the polishing process for these larger wafers. The demand for 300 mm wafers is driven by the need for high-performance electronic devices, which require advanced manufacturing techniques to achieve the desired level of precision and reliability. In contrast, the 200 mm wafer size is still widely used, particularly in the production of certain types of semiconductors and electronic components. CMP diamond pad conditioners are essential for ensuring the effectiveness of the polishing process for these wafers, which are often used in applications where cost-effectiveness is a primary consideration. The market for 200 mm wafers remains robust, supported by the ongoing demand for a wide range of electronic devices. Additionally, there are other wafer sizes used in niche applications, where CMP diamond pad conditioners are equally important. These may include smaller wafers used in specialized electronic components or larger wafers used in cutting-edge technologies. The versatility of CMP diamond pad conditioners makes them indispensable across various wafer sizes, ensuring that manufacturers can achieve the necessary level of precision and quality in their products. As the semiconductor industry continues to evolve, the demand for CMP diamond pad conditioners across different wafer sizes is expected to grow, driven by the need for more efficient and reliable manufacturing processes. The ability to adapt to different wafer sizes and applications is a key factor in the success of CMP diamond pad conditioners, highlighting their importance in the broader context of electronic manufacturing.
Global Chemical Mechanical Polishing (CMP) Diamond Pad Conditioner Market Outlook:
The global market for Chemical Mechanical Polishing (CMP) Diamond Pad Conditioner was valued at $320 million in 2024 and is anticipated to expand to a revised size of $506 million by 2031, reflecting a compound annual growth rate (CAGR) of 6.5% over the forecast period. The market is dominated by key players such as 3M, Kinik Company, Saesol, Entegris, Morgan Technical Ceramics, Nippon Steel & Sumikin Materials, Shinhan Diamond, and CP TOOLS, which collectively account for approximately 95% of the market share. Among the various segments, the CVD diamond CMP pad conditioner holds the largest share, exceeding 59%. This dominance is attributed to the superior performance and durability of CVD diamond conditioners, which are increasingly preferred in high-precision applications. The market's growth is driven by the rising demand for advanced electronic devices and the continuous innovation in semiconductor manufacturing processes. As technology advances, the need for efficient and reliable CMP processes becomes more critical, further fueling the demand for diamond pad conditioners. The competitive landscape of the market is characterized by ongoing innovation and development, as manufacturers strive to enhance the performance and cost-effectiveness of their products to meet the evolving needs of the semiconductor industry.
Report Metric | Details |
Report Name | Chemical Mechanical Polishing (CMP) Diamond Pad Conditioner Market |
Accounted market size in year | US$ 320 million |
Forecasted market size in 2031 | US$ 506 million |
CAGR | 6.5% |
Base Year | year |
Forecasted years | 2025 - 2031 |
Segment by Type |
|
Segment by Application |
|
Production by Region |
|
Consumption by Region |
|
By Company | 3M, Kinik Company, Saesol Diamond, Entegris, EHWA DIAMOND, Nippon Steel Chemical & Material, Shinhan Diamond, Abrasive Technology, BEST Engineering Surface Technologies, Xiamen Jiapin Diamond Industry |
Forecast units | USD million in value |
Report coverage | Revenue and volume forecast, company share, competitive landscape, growth factors and trends |