What is Global Aerospace & Defense Composite Ducting Market?
The Global Aerospace & Defense Composite Ducting Market is a specialized segment within the aerospace and defense industry that focuses on the production and application of composite ducting systems. These systems are integral to the efficient functioning of aircraft and defense equipment, providing pathways for air, fluids, and other essential elements. Composite ducting is favored over traditional materials due to its lightweight nature, durability, and resistance to corrosion and extreme temperatures. This market is driven by the increasing demand for fuel-efficient and lightweight aircraft, as well as advancements in composite technology. The use of composite materials in ducting systems helps reduce the overall weight of aircraft, leading to improved fuel efficiency and reduced emissions. Additionally, the defense sector benefits from these materials due to their ability to withstand harsh environments and enhance the performance of military equipment. As the aerospace and defense industries continue to evolve, the demand for advanced composite ducting solutions is expected to grow, driven by technological innovations and the need for sustainable and efficient systems.
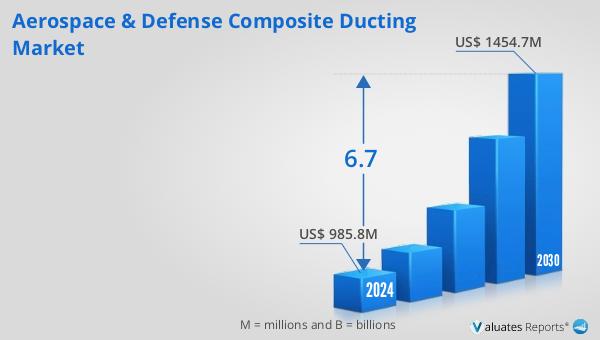
Glass Composites, Carbon Composites, Other Composites in the Global Aerospace & Defense Composite Ducting Market:
In the Global Aerospace & Defense Composite Ducting Market, various types of composites are utilized, each offering unique properties and benefits. Glass composites, for instance, are widely used due to their excellent insulation properties and cost-effectiveness. These composites are made from fine glass fibers embedded in a resin matrix, providing a balance of strength and flexibility. Glass composites are particularly suitable for applications where thermal insulation and electrical resistance are crucial, making them ideal for certain aerospace and defense applications. On the other hand, carbon composites are known for their exceptional strength-to-weight ratio and high stiffness. These composites are made from carbon fibers, which are renowned for their strength and lightweight characteristics. Carbon composites are extensively used in the aerospace industry to manufacture components that require high structural integrity and reduced weight, such as wings, fuselage sections, and control surfaces. The use of carbon composites in ducting systems helps enhance the overall performance of aircraft by reducing weight and improving fuel efficiency. Additionally, carbon composites offer excellent resistance to fatigue and environmental factors, making them suitable for demanding military applications. Other composites, such as aramid and ceramic composites, also play a significant role in the aerospace and defense sectors. Aramid composites, known for their impact resistance and thermal stability, are used in applications where high strength and durability are required. Ceramic composites, on the other hand, offer exceptional heat resistance and are used in high-temperature environments, such as engine components and exhaust systems. The choice of composite material depends on the specific requirements of the application, including factors such as weight, strength, thermal resistance, and cost. As the aerospace and defense industries continue to advance, the development and utilization of innovative composite materials are expected to drive the growth of the composite ducting market, offering enhanced performance and efficiency in various applications.
Commercial, Military, Other in the Global Aerospace & Defense Composite Ducting Market:
The Global Aerospace & Defense Composite Ducting Market finds extensive usage across various sectors, including commercial, military, and other specialized applications. In the commercial aviation sector, composite ducting systems are integral to the design and operation of modern aircraft. These systems are used to transport air, fluids, and other essential elements throughout the aircraft, ensuring optimal performance and passenger comfort. The use of composite materials in ducting systems helps reduce the overall weight of the aircraft, leading to improved fuel efficiency and reduced emissions. This is particularly important in the commercial aviation industry, where airlines are constantly seeking ways to reduce operational costs and minimize their environmental impact. Additionally, composite ducting systems offer enhanced durability and resistance to corrosion, ensuring long-term reliability and reduced maintenance requirements. In the military sector, composite ducting systems are used in a wide range of applications, from fighter jets and helicopters to naval vessels and ground vehicles. The lightweight and durable nature of composite materials make them ideal for military applications, where performance and reliability are critical. Composite ducting systems help enhance the maneuverability and speed of military aircraft, while also providing protection against harsh environmental conditions and enemy threats. Furthermore, the use of composite materials in military applications helps reduce the overall weight of equipment, allowing for increased payload capacity and improved fuel efficiency. Beyond commercial and military applications, composite ducting systems are also used in other specialized areas, such as space exploration and unmanned aerial vehicles (UAVs). In space exploration, composite materials are used to construct lightweight and durable ducting systems that can withstand the extreme conditions of space travel. Similarly, in UAVs, composite ducting systems help reduce weight and improve flight performance, enabling longer flight times and increased operational capabilities. As the aerospace and defense industries continue to evolve, the demand for advanced composite ducting solutions is expected to grow, driven by technological innovations and the need for sustainable and efficient systems across various sectors.
Global Aerospace & Defense Composite Ducting Market Outlook:
In 2024, the global market size for Aerospace & Defense Composite Ducting was estimated to be valued at approximately US$ 1,045 million. This market is projected to experience significant growth, reaching around US$ 1,635 million by 2031, with a compound annual growth rate (CAGR) of 6.7% during the forecast period from 2025 to 2031. The market is characterized by a competitive landscape, with the top five manufacturers holding a combined market share of about 20%. Among the various product segments, carbon composites stand out as the largest, accounting for approximately 65% of the market share. This dominance is attributed to the superior properties of carbon composites, such as their high strength-to-weight ratio and excellent durability, which make them ideal for aerospace and defense applications. The increasing demand for lightweight and fuel-efficient aircraft, coupled with advancements in composite technology, is expected to drive the growth of the Aerospace & Defense Composite Ducting Market in the coming years. As the industry continues to evolve, manufacturers are focusing on developing innovative composite solutions to meet the growing demand for sustainable and efficient systems.
Report Metric | Details |
Report Name | Aerospace & Defense Composite Ducting Market |
Forecasted market size in 2031 | approximately US$ 1635 million |
CAGR | 6.7% |
Forecasted years | 2025 - 2031 |
Segment by Type |
|
Segment by Application |
|
By Region |
|
By Company | Senior Plc, AIM Aerospace, Arrowhead Products, Triumph, STELIA Aerospace, ITT, Flexfab, Parker Hannifin, Hutchinson, Unitech Aerospace, Royal Engineered Composites, avs-sys, Kitsap Composites |
Forecast units | USD million in value |
Report coverage | Revenue and volume forecast, company share, competitive landscape, growth factors and trends |