What is Global Ultrasonic Welder Market?
The Global Ultrasonic Welder Market refers to the worldwide industry focused on the production and sale of ultrasonic welding machines. These machines use high-frequency ultrasonic acoustic vibrations to create solid-state welds between materials, typically plastics or metals, without the need for additional adhesives or soldering materials. Ultrasonic welding is a highly efficient and precise method, making it popular in various industries such as automotive, electronics, medical, and packaging. The market encompasses a wide range of products, from small handheld devices to large industrial machines, catering to different applications and scales of production. The growth of this market is driven by the increasing demand for lightweight, durable, and environmentally friendly products, as well as advancements in technology that enhance the efficiency and capabilities of ultrasonic welding machines.
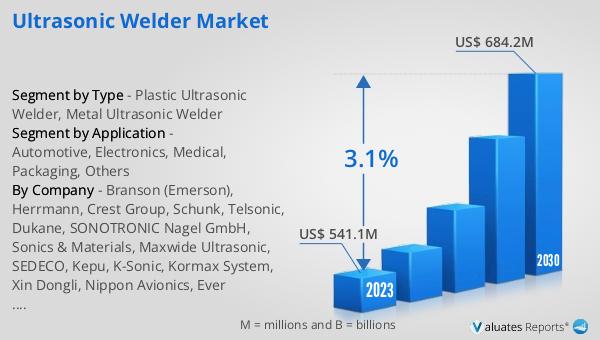
Plastic Ultrasonic Welder, Metal Ultrasonic Welder in the Global Ultrasonic Welder Market:
Plastic ultrasonic welders and metal ultrasonic welders are two primary segments within the Global Ultrasonic Welder Market. Plastic ultrasonic welders are designed specifically for joining thermoplastic materials. They work by applying high-frequency vibrations to the plastic parts being joined, causing the material to melt and fuse together at the interface. This method is widely used in the automotive industry for assembling components like dashboards, door panels, and air filters. It is also prevalent in the electronics industry for manufacturing items such as mobile phone housings, battery cases, and circuit boards. The medical industry utilizes plastic ultrasonic welders for producing items like IV catheters, blood filters, and medical tubing, ensuring strong, leak-proof seals without introducing contaminants. In the packaging sector, these welders are used to create airtight seals on blister packs, clamshell packaging, and other plastic containers, preserving product integrity and extending shelf life. On the other hand, metal ultrasonic welders are designed for joining metal components. They operate on a similar principle as plastic ultrasonic welders but are capable of handling the higher energy requirements needed to weld metals. These machines are commonly used in the automotive industry for tasks such as welding wire harnesses, battery terminals, and aluminum body panels. In the electronics sector, metal ultrasonic welders are employed to join delicate components like microcircuits, connectors, and sensors, ensuring reliable electrical connections without damaging sensitive parts. The medical industry benefits from metal ultrasonic welding in the production of surgical instruments, implantable devices, and metal tubing, where precision and cleanliness are paramount. Additionally, the packaging industry uses metal ultrasonic welders for sealing metal foils and creating tamper-evident seals on pharmaceutical and food products. Both plastic and metal ultrasonic welders offer numerous advantages, including fast processing times, strong and consistent welds, and the elimination of the need for additional materials like adhesives or solder. These benefits contribute to the growing adoption of ultrasonic welding technology across various industries. As manufacturers continue to seek ways to improve efficiency, reduce costs, and meet stringent quality standards, the demand for advanced ultrasonic welding solutions is expected to rise. The ongoing development of new materials and the increasing complexity of modern products further drive the need for versatile and reliable welding technologies, solidifying the importance of both plastic and metal ultrasonic welders in the global market.
Automotive, Electronics, Medical, Packaging, Others in the Global Ultrasonic Welder Market:
The Global Ultrasonic Welder Market finds extensive usage across several key industries, including automotive, electronics, medical, packaging, and others. In the automotive industry, ultrasonic welding is employed to assemble a wide range of components, from interior parts like dashboards and door panels to under-the-hood applications such as air filters and fluid reservoirs. The technology's ability to create strong, durable bonds without the need for additional adhesives or fasteners makes it ideal for producing lightweight and fuel-efficient vehicles. Additionally, ultrasonic welding is used to join electrical components like wire harnesses and battery terminals, ensuring reliable connections that can withstand the harsh conditions of automotive environments. In the electronics industry, ultrasonic welding is crucial for manufacturing various devices and components. It is used to assemble items such as mobile phone housings, battery cases, and circuit boards, where precision and reliability are essential. The technology's ability to create secure, high-quality welds without damaging sensitive electronic parts makes it a preferred choice for producing consumer electronics, medical devices, and other high-tech products. Ultrasonic welding also plays a vital role in the production of microcircuits, connectors, and sensors, ensuring that these components function correctly and maintain their integrity over time. The medical industry relies on ultrasonic welding for the production of a wide range of devices and components. This includes items like IV catheters, blood filters, and medical tubing, where strong, leak-proof seals are critical for patient safety and product performance. Ultrasonic welding is also used to manufacture surgical instruments, implantable devices, and other medical equipment, where precision and cleanliness are paramount. The technology's ability to create sterile, contamination-free welds without the need for additional materials makes it an ideal choice for medical applications. In the packaging industry, ultrasonic welding is used to create airtight seals on various types of packaging, including blister packs, clamshell packaging, and other plastic containers. This helps to preserve product integrity, extend shelf life, and ensure that products remain safe and secure during transportation and storage. Ultrasonic welding is also used to create tamper-evident seals on pharmaceutical and food products, providing an additional layer of security and protection for consumers. The technology's ability to create strong, reliable seals quickly and efficiently makes it a valuable tool for packaging manufacturers looking to improve their production processes and meet stringent quality standards. Beyond these primary industries, ultrasonic welding is also used in a variety of other applications. This includes the production of textiles, where ultrasonic welding is used to create seams and bonds without the need for stitching or adhesives. It is also used in the assembly of consumer goods, such as toys, household appliances, and sporting equipment, where strong, durable bonds are essential for product performance and longevity. The versatility and efficiency of ultrasonic welding make it a valuable technology for manufacturers across a wide range of industries, driving its continued growth and adoption in the global market.
Global Ultrasonic Welder Market Outlook:
The global Ultrasonic Welder market is anticipated to expand from US$ 569 million in 2024 to US$ 684.2 million by 2030, reflecting a Compound Annual Growth Rate (CAGR) of 3.1% over the forecast period. The top five manufacturers globally hold a significant share, exceeding 40% of the market. When it comes to product segmentation, plastic ultrasonic welders dominate the market, accounting for approximately 90% of the total share. This substantial market presence underscores the widespread adoption and preference for plastic ultrasonic welding technology across various industries. The growth trajectory of the market is driven by the increasing demand for efficient, reliable, and environmentally friendly welding solutions. As industries continue to evolve and seek advanced manufacturing technologies, the role of ultrasonic welding in enhancing production efficiency and product quality becomes increasingly critical. The market's expansion is also fueled by ongoing technological advancements and the development of new materials, which further enhance the capabilities and applications of ultrasonic welding machines.
Report Metric | Details |
Report Name | Ultrasonic Welder Market |
Accounted market size in 2024 | US$ 569 million |
Forecasted market size in 2030 | US$ 684.2 million |
CAGR | 3.1 |
Base Year | 2024 |
Forecasted years | 2024 - 2030 |
Segment by Type |
|
Segment by Application |
|
Production by Region |
|
Sales by Region |
|
By Company | Branson (Emerson), Herrmann, Crest Group, Schunk, Telsonic, Dukane, SONOTRONIC Nagel GmbH, Sonics & Materials, Maxwide Ultrasonic, SEDECO, Kepu, K-Sonic, Kormax System, Xin Dongli, Nippon Avionics, Ever Ultrasonic, Hornwell, Sonobond, Ultrasonic Engineering Co.,Ltd, Shanghai Chenfeng, Dongho, Topstar |
Forecast units | USD million in value |
Report coverage | Revenue and volume forecast, company share, competitive landscape, growth factors and trends |