What is Global Electroplated Diamond Wire for Photovoltaic Wafer Market?
The Global Electroplated Diamond Wire for Photovoltaic Wafer Market refers to the industry that produces and supplies diamond-coated wires used in the manufacturing of photovoltaic wafers. These wires are essential in the solar energy sector, as they are used to slice silicon ingots into thin wafers, which are then processed into solar cells. The diamond coating on the wire provides superior cutting efficiency, precision, and durability compared to traditional cutting methods. This market is driven by the increasing demand for solar energy, advancements in photovoltaic technology, and the need for more efficient and cost-effective manufacturing processes. The market encompasses various types of electroplated diamond wires, including long wires and ring wires, each designed for specific applications and cutting requirements. The growth of this market is also influenced by factors such as government policies promoting renewable energy, technological innovations, and the expansion of solar power installations worldwide.
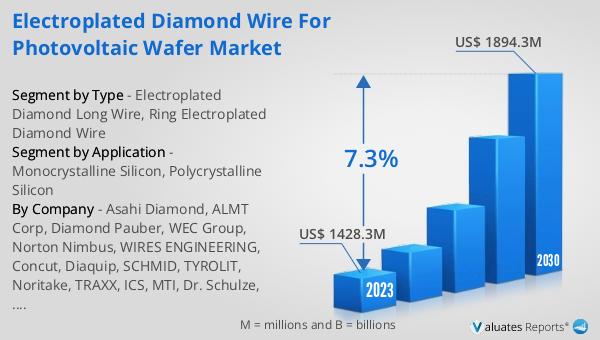
Electroplated Diamond Long Wire, Ring Electroplated Diamond Wire in the Global Electroplated Diamond Wire for Photovoltaic Wafer Market:
Electroplated Diamond Long Wire and Ring Electroplated Diamond Wire are two primary types of wires used in the Global Electroplated Diamond Wire for Photovoltaic Wafer Market. Electroplated Diamond Long Wire is a continuous wire coated with diamond particles, designed for high-precision cutting of silicon ingots into wafers. This type of wire is known for its durability, cutting speed, and ability to produce thin, uniform wafers with minimal material loss. The long wire is typically used in multi-wire saw machines, which can cut multiple wafers simultaneously, increasing production efficiency and reducing costs. On the other hand, Ring Electroplated Diamond Wire is a circular wire with a diamond coating, used in single-wire saw machines. This type of wire is ideal for cutting smaller ingots or for applications where high precision and minimal kerf loss are critical. The ring wire offers excellent cutting performance, reduced vibration, and longer tool life, making it suitable for high-precision applications in the photovoltaic industry. Both types of wires play a crucial role in the manufacturing of photovoltaic wafers, contributing to the overall efficiency and cost-effectiveness of solar cell production. The choice between long wire and ring wire depends on the specific requirements of the cutting process, including the size and type of silicon ingots, desired wafer thickness, and production volume. As the demand for solar energy continues to grow, the need for advanced cutting technologies like electroplated diamond wires will also increase, driving further innovation and development in this market.
Monocrystalline Silicon, Polycrystalline Silicon in the Global Electroplated Diamond Wire for Photovoltaic Wafer Market:
The usage of Global Electroplated Diamond Wire for Photovoltaic Wafer Market in Monocrystalline Silicon and Polycrystalline Silicon applications is significant. Monocrystalline silicon, known for its high efficiency and superior performance, is widely used in the production of high-quality solar cells. Electroplated diamond wire is essential in slicing monocrystalline silicon ingots into thin wafers with high precision and minimal material loss. The diamond coating on the wire ensures smooth and accurate cuts, reducing the risk of wafer breakage and improving the overall yield. This precision is crucial for maintaining the integrity and performance of monocrystalline solar cells, which are often used in residential and commercial solar installations. On the other hand, Polycrystalline silicon, which is less expensive and easier to produce, is commonly used in large-scale solar power projects. Electroplated diamond wire is also used in cutting polycrystalline silicon ingots into wafers, providing similar benefits of high precision and efficiency. The ability to produce thin, uniform wafers with minimal kerf loss is particularly important in polycrystalline applications, where cost-effectiveness and high production volumes are key considerations. The use of electroplated diamond wire in both monocrystalline and polycrystalline silicon applications highlights its versatility and importance in the photovoltaic industry. By enabling efficient and precise wafer cutting, these wires contribute to the overall cost reduction and performance improvement of solar cells, supporting the growth and adoption of solar energy worldwide.
Global Electroplated Diamond Wire for Photovoltaic Wafer Market Outlook:
The global Electroplated Diamond Wire for Photovoltaic Wafer market was valued at US$ 1428.3 million in 2023 and is anticipated to reach US$ 1894.3 million by 2030, witnessing a CAGR of 7.3% during the forecast period 2024-2030. This market growth reflects the increasing demand for efficient and cost-effective solutions in the photovoltaic industry. The use of electroplated diamond wire in wafer cutting processes offers significant advantages, including higher precision, reduced material loss, and improved production efficiency. These benefits are driving the adoption of diamond wire technology in the manufacturing of solar cells, contributing to the overall expansion of the market. The projected growth also indicates the ongoing advancements in photovoltaic technology and the rising importance of renewable energy sources in addressing global energy needs. As the market continues to evolve, the development of new and improved diamond wire products will play a crucial role in meeting the demands of the solar energy sector and supporting the transition to a more sustainable energy future.
Report Metric | Details |
Report Name | Electroplated Diamond Wire for Photovoltaic Wafer Market |
Accounted market size in 2023 | US$ 1428.3 million |
Forecasted market size in 2030 | US$ 1894.3 million |
CAGR | 7.3% |
Base Year | 2023 |
Forecasted years | 2024 - 2030 |
Segment by Type |
|
Segment by Application |
|
Production by Region |
|
Consumption by Region |
|
By Company | Asahi Diamond, ALMT Corp, Diamond Pauber, WEC Group, Norton Nimbus, WIRES ENGINEERING, Concut, Diaquip, SCHMID, TYROLIT, Noritake, TRAXX, ICS, MTI, Dr. Schulze, Diat New Material, Fusen, Nanjing Sanchao Diamond Tool, Yangling Metron New Material, Qingdao Gaoce Technology, Changsha Dialine New Material, Jiangsu Resource Fusion Diamond Technology |
Forecast units | USD million in value |
Report coverage | Revenue and volume forecast, company share, competitive landscape, growth factors and trends |