What is Global Rotary Friction Weldings Market?
The Global Rotary Friction Weldings Market refers to the worldwide industry that focuses on the production, distribution, and application of rotary friction welding technology. This technology is a solid-state welding process that joins materials, typically metals, by using rotational motion and pressure to generate heat through friction. The process does not require external heat sources, making it energy-efficient and environmentally friendly. Rotary friction welding is widely used in various industries due to its ability to produce high-quality, strong, and durable joints. The market encompasses different types of rotary friction welding techniques, including inertia, direct drive, and hybrid methods, each offering unique advantages for specific applications. The demand for rotary friction welding is driven by its efficiency, cost-effectiveness, and the growing need for advanced manufacturing solutions in sectors such as automotive, aerospace, and machinery. As industries continue to seek innovative ways to enhance production processes and product quality, the Global Rotary Friction Weldings Market is expected to experience steady growth.
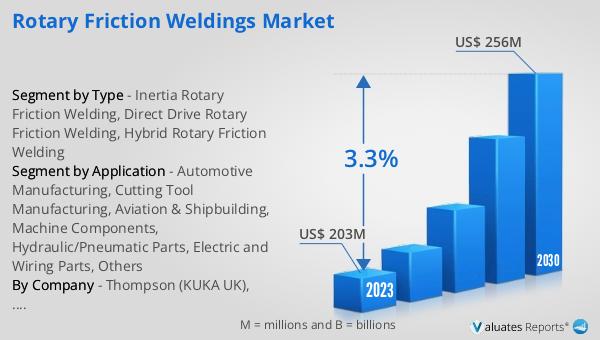
Inertia Rotary Friction Welding, Direct Drive Rotary Friction Welding, Hybrid Rotary Friction Welding in the Global Rotary Friction Weldings Market:
Inertia Rotary Friction Welding, Direct Drive Rotary Friction Welding, and Hybrid Rotary Friction Welding are three primary techniques within the Global Rotary Friction Weldings Market, each serving distinct purposes and applications. Inertia Rotary Friction Welding involves storing kinetic energy in a flywheel, which is then released to create frictional heat when the flywheel is brought into contact with the workpieces. This method is particularly effective for welding materials with different thermal properties and is commonly used in applications requiring high precision and strength. Direct Drive Rotary Friction Welding, on the other hand, uses a continuous rotational motion powered by an electric motor to generate the necessary frictional heat. This technique allows for greater control over the welding process, making it suitable for applications that demand consistent and repeatable results. It is often used in the automotive and aerospace industries where precision and reliability are paramount. Hybrid Rotary Friction Welding combines elements of both inertia and direct drive methods, offering a versatile solution that can adapt to various welding requirements. This approach provides the benefits of both techniques, such as the energy efficiency of inertia welding and the control of direct drive welding, making it ideal for complex and demanding applications. The hybrid method is particularly useful in industries where a wide range of materials and joint configurations are encountered. Overall, these three techniques within the Global Rotary Friction Weldings Market cater to diverse industrial needs, ensuring that manufacturers can achieve optimal results in their welding processes.
Automotive Manufacturing, Cutting Tool Manufacturing, Aviation & Shipbuilding, Machine Components, Hydraulic/Pneumatic Parts, Electric and Wiring Parts, Others in the Global Rotary Friction Weldings Market:
The Global Rotary Friction Weldings Market finds extensive usage across several key industries, each benefiting from the unique advantages of this welding technology. In the automotive manufacturing sector, rotary friction welding is employed to join various components such as drive shafts, gear parts, and engine valves. The process ensures strong, reliable joints that can withstand the high stresses and temperatures encountered in automotive applications. Cutting tool manufacturing also leverages rotary friction welding to produce durable and precise tools. The ability to join different materials, such as high-speed steel to carbide, enhances the performance and longevity of cutting tools. In the aviation and shipbuilding industries, rotary friction welding is used to assemble critical components like turbine blades, landing gear, and ship propellers. The technology's ability to create high-strength joints without compromising material integrity is crucial for the safety and performance of aircraft and ships. Machine components, including hydraulic and pneumatic parts, benefit from rotary friction welding's precision and strength, ensuring reliable operation in demanding environments. Electric and wiring parts, such as connectors and terminals, also utilize this welding method to achieve secure and efficient electrical connections. Beyond these specific applications, rotary friction welding is employed in various other industries where strong, durable joints are essential. The technology's versatility and efficiency make it a valuable tool for manufacturers seeking to improve product quality and production processes.
Global Rotary Friction Weldings Market Outlook:
The global Rotary Friction Weldings market was valued at US$ 203 million in 2023 and is anticipated to reach US$ 256 million by 2030, witnessing a CAGR of 3.3% during the forecast period from 2024 to 2030. This growth reflects the increasing demand for advanced welding solutions across various industries. The market is dominated by the top four manufacturers, who collectively hold a significant share of about 65%. These leading companies play a crucial role in driving innovation and setting industry standards. Their expertise and technological advancements contribute to the widespread adoption of rotary friction welding techniques. As the market continues to evolve, these manufacturers are expected to maintain their influential position, shaping the future of the Global Rotary Friction Weldings Market. The steady growth and competitive landscape highlight the importance of rotary friction welding in modern manufacturing, underscoring its role in enhancing product quality and production efficiency.
Report Metric | Details |
Report Name | Rotary Friction Weldings Market |
Accounted market size in 2023 | US$ 203 million |
Forecasted market size in 2030 | US$ 256 million |
CAGR | 3.3% |
Base Year | 2023 |
Forecasted years | 2024 - 2030 |
Segment by Type |
|
Segment by Application |
|
By Region |
|
By Company | Thompson (KUKA UK), MTI (USA), NITTO SEIKI (Japan), Izumi Machine (Japan), H&B OMEGA Europa GmbH(Symacon)(Germany), ETA (India), U-Jin Tech (Korea), Sakae Industries (Japan), Gatwick (UK), YUAN YU Industrial Co., Ltd. (Taiwan), An Gen Machine Mfg. (Taiwan), Jiangsu RCM Co. (China) |
Forecast units | USD million in value |
Report coverage | Revenue and volume forecast, company share, competitive landscape, growth factors and trends |