What is Precision Ultrasonic Flaw Detector - Global Market?
Precision Ultrasonic Flaw Detectors are advanced tools used in non-destructive testing to identify defects in materials without causing any damage. These devices utilize high-frequency sound waves to detect imperfections such as cracks, voids, or inclusions in a variety of materials, including metals, plastics, and composites. The global market for these detectors is expanding due to their critical role in ensuring the safety and reliability of products across various industries. They are particularly valued in sectors where material integrity is crucial, such as aerospace, automotive, and manufacturing. The precision ultrasonic flaw detector market is driven by technological advancements that enhance detection capabilities, making them more accurate and efficient. As industries continue to prioritize quality assurance and safety, the demand for these detectors is expected to grow. The market is characterized by a mix of established players and new entrants, each striving to innovate and offer more sophisticated solutions. This competitive landscape encourages continuous improvement and adaptation to meet the evolving needs of end-users. Overall, precision ultrasonic flaw detectors are indispensable tools in modern quality control processes, contributing significantly to the safety and performance of various products and structures.
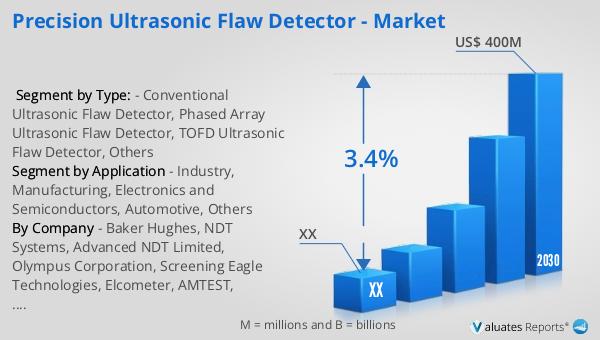
Conventional Ultrasonic Flaw Detector, Phased Array Ultrasonic Flaw Detector, TOFD Ultrasonic Flaw Detector, Others in the Precision Ultrasonic Flaw Detector - Global Market:
Conventional Ultrasonic Flaw Detectors are the traditional form of ultrasonic testing equipment. They operate by sending high-frequency sound waves into a material and analyzing the reflected waves to detect any discontinuities. These detectors are widely used due to their reliability and cost-effectiveness. They are suitable for a range of applications, from simple thickness measurements to more complex inspections of welds and castings. However, their effectiveness can be limited by the skill of the operator and the complexity of the material being tested. Phased Array Ultrasonic Flaw Detectors represent a more advanced technology. They use multiple elements in an array to steer, focus, and scan beams of sound waves, providing a more detailed and accurate image of the material being inspected. This technology allows for faster inspections and the ability to detect smaller flaws, making it ideal for critical applications in industries such as aerospace and energy. Time of Flight Diffraction (TOFD) Ultrasonic Flaw Detectors are another sophisticated option. They measure the time it takes for sound waves to travel through a material and reflect back, providing precise information about the size and location of flaws. TOFD is particularly effective for inspecting welds and is often used in conjunction with other methods to provide a comprehensive assessment. Other types of ultrasonic flaw detectors include portable and handheld devices, which offer flexibility and convenience for on-site inspections. These devices are essential for industries that require frequent testing in various locations, such as construction and maintenance. Each type of ultrasonic flaw detector has its strengths and limitations, and the choice of which to use depends on the specific requirements of the inspection task. As technology continues to evolve, these detectors are becoming more sophisticated, offering enhanced capabilities and greater ease of use. The global market for ultrasonic flaw detectors is diverse, with a range of products available to meet the needs of different industries and applications. Manufacturers are continually innovating to improve the performance and functionality of these devices, ensuring they remain an essential tool in non-destructive testing.
Industry, Manufacturing, Electronics and Semiconductors, Automotive, Others in the Precision Ultrasonic Flaw Detector - Global Market:
Precision Ultrasonic Flaw Detectors are utilized across a wide range of industries due to their ability to ensure the integrity and safety of materials and structures. In the industrial sector, these detectors are crucial for inspecting components and assemblies to detect any defects that could compromise performance or safety. They are used in the manufacturing process to ensure that products meet quality standards and are free from defects. This is particularly important in industries where safety is paramount, such as aerospace and automotive, where even minor flaws can have catastrophic consequences. In the electronics and semiconductor industries, precision ultrasonic flaw detectors are used to inspect delicate components and assemblies. These industries require high levels of precision and reliability, and ultrasonic testing provides a non-invasive method to ensure that products meet stringent quality standards. The automotive industry also relies heavily on ultrasonic flaw detectors to inspect critical components such as engine parts, transmissions, and chassis. These detectors help identify defects that could lead to failures, ensuring the safety and reliability of vehicles. In addition to these industries, precision ultrasonic flaw detectors are used in a variety of other applications, including construction, energy, and oil and gas. In construction, they are used to inspect concrete structures and welds, ensuring that buildings and infrastructure are safe and sound. In the energy sector, ultrasonic testing is used to inspect pipelines, turbines, and other critical components to prevent failures and ensure efficient operation. The oil and gas industry also relies on ultrasonic flaw detectors to inspect pipelines and other infrastructure, helping to prevent leaks and other issues that could have serious environmental and safety implications. Overall, precision ultrasonic flaw detectors are an essential tool in ensuring the safety and reliability of products and structures across a wide range of industries. Their ability to detect defects without causing damage makes them invaluable in quality control and assurance processes. As industries continue to prioritize safety and quality, the demand for these detectors is expected to grow, driving further innovation and development in the field.
Precision Ultrasonic Flaw Detector - Global Market Outlook:
The global market for Precision Ultrasonic Flaw Detectors was valued at approximately $315 million in 2023. It is projected to grow to around $400 million by 2030, with a compound annual growth rate (CAGR) of 3.4% during the forecast period from 2024 to 2030. The market is predominantly controlled by a few key players, with the top five manufacturers accounting for over 54% of the global market share. In terms of application, ultrasonic flaw detectors are most commonly used in the manufacturing and machinery sectors, which account for about 22% of the market. Other significant application areas include energy, aerospace, oil and gas, and automotive, each contributing approximately 15% to the market. This distribution highlights the widespread adoption of ultrasonic flaw detectors across various industries, driven by the need for reliable and efficient non-destructive testing solutions. As industries continue to prioritize safety and quality, the demand for precision ultrasonic flaw detectors is expected to grow, further solidifying their position as an essential tool in modern quality control processes. The competitive landscape of the market encourages continuous innovation and improvement, ensuring that these detectors remain at the forefront of non-destructive testing technology.
Report Metric | Details |
Report Name | Precision Ultrasonic Flaw Detector - Market |
Forecasted market size in 2030 | US$ 400 million |
CAGR | 3.4% |
Forecasted years | 2024 - 2030 |
Segment by Type: |
|
Segment by Application |
|
By Region |
|
By Company | Baker Hughes, NDT Systems, Advanced NDT Limited, Olympus Corporation, Screening Eagle Technologies, Elcometer, AMTEST, HUATEC Group, Sino Age Development Technology, Proceq, Beijing Cap High Technology Co.,Ltd., Beijing TIME High Technology Ltd, Jinan Hensgrand Instrument Co., Ltd, Wuxi Jiebo Electrical Technology Co., Ltd., Dragon Electronics Co, Shantou Institute of Ultrasonic Instruments Co., Ltd, ACS, Sonatest |
Forecast units | USD million in value |
Report coverage | Revenue and volume forecast, company share, competitive landscape, growth factors and trends |