What is Global Medical Wire Grinding Market?
The Global Medical Wire Grinding Market is a specialized segment within the broader medical device industry, focusing on the precision grinding of medical wires used in various medical applications. These wires are essential components in numerous medical devices, including catheters, guidewires, and surgical instruments. The grinding process ensures that the wires meet stringent quality standards, offering the necessary precision, smoothness, and durability required for medical applications. The market encompasses various grinding techniques, such as centerless grinding, electro-chemical grinding, and point grinding, each catering to specific requirements and materials. The demand for high-quality medical wires is driven by the increasing prevalence of chronic diseases, advancements in medical technology, and the growing need for minimally invasive surgical procedures. As a result, the Global Medical Wire Grinding Market plays a crucial role in ensuring the reliability and effectiveness of medical devices, ultimately contributing to improved patient outcomes and healthcare quality.
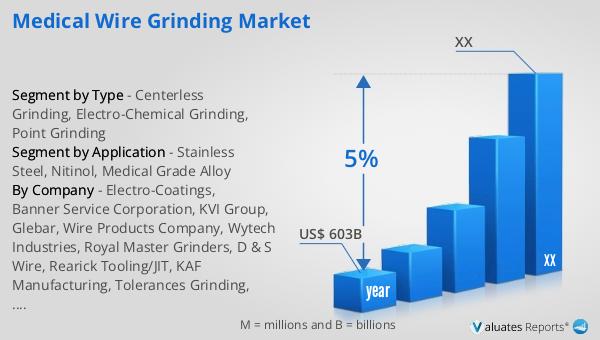
Centerless Grinding, Electro-Chemical Grinding, Point Grinding in the Global Medical Wire Grinding Market:
Centerless grinding, electro-chemical grinding, and point grinding are three critical techniques used in the Global Medical Wire Grinding Market, each offering unique advantages for different applications. Centerless grinding is a widely used method that involves the removal of material from the outer surface of a wire without the need for a spindle or fixture to hold the wire in place. This technique is highly efficient and capable of producing wires with precise diameters and smooth surfaces, making it ideal for high-volume production. The process involves feeding the wire through a grinding wheel and a regulating wheel, which work together to remove material and achieve the desired dimensions. Centerless grinding is particularly suitable for producing long, thin wires used in catheters and guidewires, where consistency and precision are paramount. Electro-chemical grinding (ECG) is another important technique in the medical wire grinding market. ECG combines electro-chemical machining with conventional grinding to remove material from the wire. This process involves passing an electric current through the wire and a conductive grinding wheel, which causes a chemical reaction that dissolves the material. The grinding wheel then removes the dissolved material, resulting in a smooth and precise finish. ECG is particularly advantageous for grinding hard materials, such as stainless steel and medical-grade alloys, as it minimizes heat generation and reduces the risk of thermal damage to the wire. This technique is also known for its ability to produce complex shapes and fine details, making it suitable for specialized medical devices that require intricate wire designs. Point grinding, on the other hand, is a technique used to create sharp, precise points on medical wires. This process is essential for producing needles, guidewires, and other medical instruments that require a pointed tip for insertion into the body. Point grinding involves using a grinding wheel to shape the tip of the wire to the desired angle and sharpness. The process requires a high level of precision and control to ensure that the points are consistent and meet the required specifications. Point grinding is often used in conjunction with other grinding techniques to produce medical wires with both precise diameters and sharp points, ensuring that they are suitable for their intended applications. Each of these grinding techniques plays a vital role in the Global Medical Wire Grinding Market, catering to different materials and applications. Centerless grinding is ideal for high-volume production of long, thin wires with consistent diameters, while electro-chemical grinding is well-suited for hard materials and complex shapes. Point grinding is essential for creating sharp, precise points on medical wires, ensuring that they can be used effectively in various medical procedures. Together, these techniques enable the production of high-quality medical wires that meet the stringent requirements of the medical device industry, ultimately contributing to improved patient care and outcomes.
Stainless Steel, Nitinol, Medical Grade Alloy in the Global Medical Wire Grinding Market:
The Global Medical Wire Grinding Market finds extensive usage in the processing of various materials, including stainless steel, nitinol, and medical-grade alloys, each offering unique properties and benefits for medical applications. Stainless steel is one of the most commonly used materials in the medical wire industry due to its excellent mechanical properties, corrosion resistance, and biocompatibility. Medical wires made from stainless steel are used in a wide range of applications, including catheters, guidewires, and surgical instruments. The grinding process ensures that stainless steel wires have smooth surfaces and precise dimensions, which are crucial for their performance and reliability in medical procedures. Centerless grinding is particularly effective for processing stainless steel wires, as it can produce wires with consistent diameters and high surface quality, making them suitable for various medical devices. Nitinol, a nickel-titanium alloy, is another important material in the Global Medical Wire Grinding Market. Nitinol is known for its unique properties, including shape memory and superelasticity, which make it highly suitable for medical applications. Shape memory allows nitinol wires to return to their original shape after being deformed, while superelasticity enables them to undergo significant deformation without permanent damage. These properties are particularly valuable in minimally invasive surgical procedures, where flexibility and precision are essential. Electro-chemical grinding is often used to process nitinol wires, as it can effectively remove material without generating excessive heat, which could alter the alloy's properties. The grinding process ensures that nitinol wires have smooth surfaces and precise dimensions, enhancing their performance and reliability in medical devices such as stents, guidewires, and orthodontic appliances. Medical-grade alloys, including cobalt-chromium and titanium alloys, are also widely used in the medical wire industry due to their excellent mechanical properties, biocompatibility, and corrosion resistance. These alloys are often used in applications that require high strength and durability, such as orthopedic implants, cardiovascular devices, and dental instruments. The grinding process is essential for ensuring that medical-grade alloy wires meet the stringent quality standards required for medical applications. Electro-chemical grinding is particularly effective for processing these hard materials, as it can produce smooth surfaces and precise dimensions without causing thermal damage. Point grinding is also commonly used to create sharp, precise points on medical-grade alloy wires, ensuring that they can be used effectively in various medical procedures. The usage of the Global Medical Wire Grinding Market in processing stainless steel, nitinol, and medical-grade alloys highlights the importance of precision grinding techniques in the medical device industry. Each material offers unique properties and benefits, making them suitable for different medical applications. The grinding process ensures that medical wires made from these materials have the necessary precision, smoothness, and durability required for their intended use. By catering to the specific requirements of each material, the Global Medical Wire Grinding Market plays a crucial role in the production of high-quality medical wires, ultimately contributing to improved patient care and outcomes.
Global Medical Wire Grinding Market Outlook:
According to our research, the global market for medical devices is projected to reach approximately US$ 603 billion by the year 2023, with an anticipated growth rate of 5% annually over the next six years. This significant market size underscores the critical role that medical devices play in modern healthcare, addressing a wide range of medical needs from diagnostics to treatment and rehabilitation. The steady growth rate reflects ongoing advancements in medical technology, increasing prevalence of chronic diseases, and the rising demand for minimally invasive surgical procedures. As the medical device market expands, the demand for high-quality components, such as precision-ground medical wires, is also expected to rise. These components are essential for the functionality and reliability of various medical devices, including catheters, guidewires, and surgical instruments. The Global Medical Wire Grinding Market, therefore, stands to benefit from the overall growth of the medical device industry, as it provides the necessary precision and quality required for these critical components. By ensuring that medical wires meet stringent quality standards, the Global Medical Wire Grinding Market contributes to the development of reliable and effective medical devices, ultimately enhancing patient care and outcomes.
Report Metric | Details |
Report Name | Medical Wire Grinding Market |
Accounted market size in year | US$ 603 billion |
CAGR | 5% |
Base Year | year |
Segment by Type |
|
Segment by Application |
|
By Region |
|
By Company | Electro-Coatings, Banner Service Corporation, KVI Group, Glebar, Wire Products Company, Wytech Industries, Royal Master Grinders, D & S Wire, Rearick Tooling/JIT, KAF Manufacturing, Tolerances Grinding, Component Supply, IKER Manufacturing, Lapco LLC |
Forecast units | USD million in value |
Report coverage | Revenue and volume forecast, company share, competitive landscape, growth factors and trends |