What is X-ray Inspection System for Secondary Battery - Global Market?
The X-ray Inspection System for Secondary Battery - Global Market is a specialized segment within the broader X-ray inspection industry, focusing on the quality assurance and safety of secondary batteries, particularly lithium-ion batteries. These systems are crucial for detecting internal defects, such as misalignments, foreign materials, or structural inconsistencies, which can compromise battery performance and safety. As the demand for lithium-ion batteries surges, driven by their widespread application in electric vehicles, consumer electronics, and renewable energy storage, the need for reliable inspection systems becomes paramount. X-ray inspection systems offer non-destructive testing capabilities, allowing manufacturers to ensure the integrity and reliability of their battery products without causing any damage. This market is characterized by technological advancements aimed at enhancing inspection accuracy, speed, and automation, catering to the high-volume production environments typical of battery manufacturing. The global market for these systems is poised for significant growth, reflecting the increasing emphasis on battery safety and quality in a rapidly electrifying world. As industries continue to innovate and expand their use of lithium-ion batteries, the role of X-ray inspection systems in maintaining high standards of quality and safety will only become more critical.
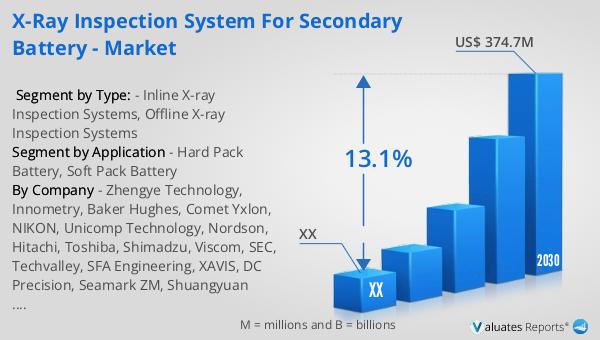
Inline X-ray Inspection Systems, Offline X-ray Inspection Systems in the X-ray Inspection System for Secondary Battery - Global Market:
Inline X-ray Inspection Systems and Offline X-ray Inspection Systems are two primary categories within the X-ray Inspection System for Secondary Battery - Global Market, each serving distinct roles in the battery manufacturing process. Inline X-ray Inspection Systems are integrated directly into the production line, providing real-time inspection of batteries as they are manufactured. This integration allows for immediate detection of defects, enabling manufacturers to address issues promptly and reduce the risk of defective products reaching the market. Inline systems are particularly beneficial in high-volume production settings, where speed and efficiency are crucial. They offer continuous monitoring and can be configured to automatically sort out defective units, thus streamlining the quality control process. On the other hand, Offline X-ray Inspection Systems are used for batch testing and quality assurance outside the main production line. These systems are typically employed for more detailed inspections, where batteries are sampled and analyzed in a controlled environment. Offline systems are ideal for conducting thorough investigations of specific battery batches, providing manufacturers with detailed insights into potential defects and areas for improvement. Both inline and offline systems utilize advanced imaging technologies to detect a wide range of defects, including internal misalignments, foreign objects, and structural inconsistencies. The choice between inline and offline systems often depends on the specific needs of the manufacturer, including production volume, desired inspection speed, and the level of detail required in the inspection process. As the demand for high-quality secondary batteries continues to grow, manufacturers are increasingly investing in both types of systems to ensure comprehensive quality assurance across their production processes. The integration of these systems into battery manufacturing not only enhances product quality but also helps manufacturers comply with stringent safety standards and regulations. By leveraging the capabilities of inline and offline X-ray inspection systems, manufacturers can achieve a higher level of precision and reliability in their battery products, ultimately contributing to the overall safety and performance of the end-use applications.
Hard Pack Battery, Soft Pack Battery in the X-ray Inspection System for Secondary Battery - Global Market:
The usage of X-ray Inspection Systems for Secondary Battery - Global Market is particularly significant in the production of Hard Pack and Soft Pack Batteries, each presenting unique challenges and requirements. Hard Pack Batteries, often used in applications requiring robust and durable power sources, benefit greatly from X-ray inspection due to their complex internal structures. These batteries typically consist of multiple cells encased in a rigid shell, making it essential to ensure that all components are correctly aligned and free from defects. X-ray inspection systems provide a non-invasive means of examining the internal configuration of hard pack batteries, allowing manufacturers to detect issues such as misaligned cells, foreign materials, or structural weaknesses that could compromise performance or safety. By identifying these defects early in the production process, manufacturers can take corrective actions to prevent defective products from reaching consumers, thereby enhancing product reliability and customer satisfaction. In contrast, Soft Pack Batteries, which are commonly used in portable electronic devices due to their lightweight and flexible design, present different inspection challenges. These batteries are typically encased in a soft, flexible pouch, making it crucial to ensure that the internal components are securely positioned and free from defects that could lead to leakage or failure. X-ray inspection systems are particularly effective in detecting issues such as swelling, misalignment, or foreign objects within soft pack batteries, providing manufacturers with the insights needed to maintain high standards of quality and safety. The ability to conduct thorough inspections without damaging the battery is a significant advantage, allowing manufacturers to ensure the integrity of their products while minimizing waste. As the demand for both hard pack and soft pack batteries continues to rise, driven by the proliferation of electronic devices and the growing emphasis on renewable energy solutions, the role of X-ray inspection systems in ensuring product quality and safety becomes increasingly important. By investing in advanced inspection technologies, manufacturers can enhance their production processes, reduce the risk of defects, and ultimately deliver safer, more reliable battery products to the market.
X-ray Inspection System for Secondary Battery - Global Market Outlook:
The global market for X-ray Inspection Systems for Secondary Batteries was valued at approximately $174 million in 2023 and is projected to grow to around $374.7 million by 2030, reflecting a compound annual growth rate (CAGR) of 13.1% during the forecast period from 2024 to 2030. This growth trajectory underscores the increasing importance of X-ray inspection systems in the battery manufacturing industry, driven by the expanding use of lithium-ion batteries across various sectors. As industries such as electric vehicles, consumer electronics, and renewable energy storage continue to rely heavily on lithium-ion batteries, the demand for reliable and efficient inspection systems is expected to rise. X-ray inspection systems play a crucial role in ensuring the quality and safety of these batteries by providing non-destructive testing capabilities that allow manufacturers to detect internal defects and inconsistencies. The market's growth is further fueled by ongoing innovations in X-ray inspection technology, aimed at enhancing inspection accuracy, speed, and automation. As manufacturers strive to meet the increasing demand for high-quality batteries, the adoption of advanced X-ray inspection systems is likely to become more widespread, contributing to the overall growth and development of the global market.
Report Metric | Details |
Report Name | X-ray Inspection System for Secondary Battery - Market |
Forecasted market size in 2030 | US$ 374.7 million |
CAGR | 13.1% |
Forecasted years | 2024 - 2030 |
Segment by Type: |
|
Segment by Application |
|
By Region |
|
By Company | Zhengye Technology, Innometry, Baker Hughes, Comet Yxlon, NIKON, Unicomp Technology, Nordson, Hitachi, Toshiba, Shimadzu, Viscom, SEC, Techvalley, SFA Engineering, XAVIS, DC Precision, Seamark ZM, Shuangyuan Technology |
Forecast units | USD million in value |
Report coverage | Revenue and volume forecast, company share, competitive landscape, growth factors and trends |