What is Lithium Battery X-ray Inspection Systems - Global Market?
Lithium Battery X-ray Inspection Systems are specialized tools used to ensure the quality and safety of lithium batteries, which are widely used in various applications such as electric vehicles, consumer electronics, and renewable energy storage. These systems utilize X-ray technology to inspect the internal structure of lithium batteries without causing any damage. By doing so, they help in identifying defects such as misalignments, foreign materials, and other anomalies that could potentially lead to battery failure or safety hazards. The global market for these systems is expanding due to the increasing demand for lithium-ion batteries, driven by the growth in electric vehicles and renewable energy sectors. As manufacturers strive to meet stringent safety and quality standards, the adoption of X-ray inspection systems is becoming more prevalent. These systems not only enhance the reliability of lithium batteries but also contribute to the overall safety of products that rely on them. The market is characterized by continuous innovation, with companies investing in advanced technologies to improve the accuracy and efficiency of these inspection systems. As a result, the global market for Lithium Battery X-ray Inspection Systems is poised for significant growth in the coming years.
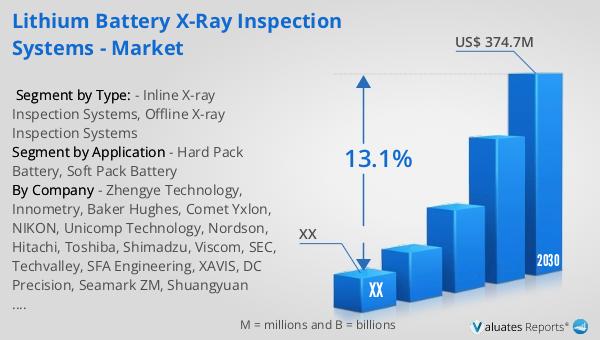
Inline X-ray Inspection Systems, Offline X-ray Inspection Systems in the Lithium Battery X-ray Inspection Systems - Global Market:
Inline X-ray Inspection Systems and Offline X-ray Inspection Systems are two primary types of inspection systems used in the global market for lithium battery X-ray inspection. Inline X-ray Inspection Systems are integrated directly into the production line, allowing for real-time inspection of lithium batteries as they are being manufactured. This integration ensures that any defects or anomalies are detected immediately, enabling manufacturers to address issues promptly and maintain high-quality standards. Inline systems are particularly beneficial for high-volume production environments where speed and efficiency are crucial. They help in reducing waste and improving overall production efficiency by catching defects early in the manufacturing process. On the other hand, Offline X-ray Inspection Systems are standalone units that are used to inspect lithium batteries after they have been manufactured. These systems are typically used for batch inspections or quality control checks, providing a more detailed analysis of the battery's internal structure. Offline systems offer flexibility as they can be used to inspect batteries from different production lines or even from different manufacturers. They are ideal for applications where a thorough inspection is required, such as in research and development or for quality assurance purposes. Both Inline and Offline X-ray Inspection Systems play a critical role in ensuring the safety and reliability of lithium batteries. They help manufacturers comply with industry standards and regulations, which is essential for gaining consumer trust and maintaining a competitive edge in the market. As the demand for lithium batteries continues to grow, the need for efficient and accurate inspection systems becomes increasingly important. Manufacturers are investing in advanced technologies to enhance the capabilities of these systems, such as incorporating artificial intelligence and machine learning algorithms to improve defect detection and analysis. This ongoing innovation is driving the growth of the global market for lithium battery X-ray inspection systems, making them an indispensable tool for manufacturers worldwide.
Hard Pack Battery, Soft Pack Battery in the Lithium Battery X-ray Inspection Systems - Global Market:
Lithium Battery X-ray Inspection Systems are used extensively in the inspection of both Hard Pack and Soft Pack Batteries. Hard Pack Batteries are typically encased in a rigid outer shell, providing structural support and protection against physical damage. These batteries are commonly used in applications where durability and robustness are essential, such as in electric vehicles and industrial equipment. X-ray inspection systems are crucial for Hard Pack Batteries as they allow manufacturers to inspect the internal components without dismantling the outer casing. This non-destructive testing method helps in identifying defects such as misaligned cells, foreign objects, or internal damage that could compromise the battery's performance or safety. By ensuring the integrity of Hard Pack Batteries, X-ray inspection systems help manufacturers meet stringent safety standards and enhance the reliability of their products. Soft Pack Batteries, on the other hand, are encased in a flexible, lightweight pouch, making them ideal for applications where weight and space are critical considerations, such as in consumer electronics and portable devices. The flexible nature of Soft Pack Batteries poses unique challenges for inspection, as the internal components are more susceptible to movement and misalignment. X-ray inspection systems are essential for Soft Pack Batteries as they provide a detailed view of the internal structure, allowing manufacturers to detect any anomalies that could affect the battery's performance or safety. These systems help in ensuring that Soft Pack Batteries meet the required quality standards and perform reliably in their intended applications. The use of X-ray inspection systems in both Hard Pack and Soft Pack Batteries is driven by the need for high-quality, reliable, and safe lithium batteries. As the demand for these batteries continues to grow, manufacturers are increasingly relying on advanced inspection technologies to ensure the quality and safety of their products. This trend is contributing to the growth of the global market for lithium battery X-ray inspection systems, making them an essential tool for manufacturers in the industry.
Lithium Battery X-ray Inspection Systems - Global Market Outlook:
The global market for Lithium Battery X-ray Inspection Systems was valued at approximately US$ 174 million in 2023. It is projected to grow to a revised size of US$ 374.7 million by 2030, reflecting a compound annual growth rate (CAGR) of 13.1% during the forecast period from 2024 to 2030. This growth is largely driven by the increasing adoption of lithium-ion batteries across various industries, including automotive, consumer electronics, and renewable energy. As the demand for these batteries continues to rise, manufacturers are investing in advanced inspection systems to ensure the quality and safety of their products. X-ray inspection systems play a crucial role in this process by providing non-destructive testing capabilities that allow manufacturers to detect defects and anomalies in lithium batteries. This capability is essential for meeting industry standards and regulations, which are becoming increasingly stringent as the use of lithium-ion batteries expands. The market is characterized by continuous innovation, with companies developing new technologies to enhance the accuracy and efficiency of X-ray inspection systems. This innovation is driving the growth of the market, making it an essential component of the lithium battery manufacturing process. As a result, the global market for Lithium Battery X-ray Inspection Systems is expected to experience significant growth in the coming years, driven by the expanding use of lithium-ion batteries across various industries.
Report Metric | Details |
Report Name | Lithium Battery X-ray Inspection Systems - Market |
Forecasted market size in 2030 | US$ 374.7 million |
CAGR | 13.1% |
Forecasted years | 2024 - 2030 |
Segment by Type: |
|
Segment by Application |
|
By Region |
|
By Company | Zhengye Technology, Innometry, Baker Hughes, Comet Yxlon, NIKON, Unicomp Technology, Nordson, Hitachi, Toshiba, Shimadzu, Viscom, SEC, Techvalley, SFA Engineering, XAVIS, DC Precision, Seamark ZM, Shuangyuan Technology, Guangzhou Haozhi Imaging Technology |
Forecast units | USD million in value |
Report coverage | Revenue and volume forecast, company share, competitive landscape, growth factors and trends |