What is Global Welded Spiral Heat Exchangers Market?
The Global Welded Spiral Heat Exchangers Market is a specialized segment within the broader heat exchanger industry, focusing on devices that facilitate efficient heat transfer between two fluids. These exchangers are uniquely designed with a spiral configuration, which enhances their ability to handle high temperatures and pressures, making them ideal for demanding industrial applications. The spiral design allows for a compact structure, reducing the space required for installation while maximizing heat transfer efficiency. This market is driven by the increasing demand for energy-efficient solutions across various industries, including petrochemicals, pharmaceuticals, and food processing. The welded construction of these heat exchangers ensures durability and reliability, even in harsh operating conditions. As industries continue to seek ways to optimize energy use and reduce operational costs, the demand for welded spiral heat exchangers is expected to grow. Additionally, the global push towards sustainable and environmentally friendly technologies further propels the market, as these exchangers contribute to energy conservation and reduced emissions. Overall, the Global Welded Spiral Heat Exchangers Market represents a critical component in the industrial landscape, offering solutions that align with modern efficiency and sustainability goals.
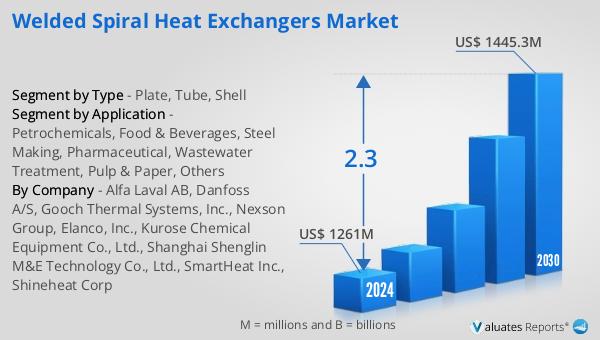
Plate, Tube, Shell in the Global Welded Spiral Heat Exchangers Market:
In the context of the Global Welded Spiral Heat Exchangers Market, the components such as plates, tubes, and shells play pivotal roles in the functionality and efficiency of these devices. Plates in heat exchangers are typically used in plate heat exchangers, where they are arranged in a series to create multiple channels for fluid flow. The design of these plates is crucial as it determines the heat transfer efficiency and pressure drop across the exchanger. In welded spiral heat exchangers, plates are often spirally wound to form a compact unit, allowing for efficient heat transfer in a smaller footprint. This design is particularly beneficial in applications where space is limited, and high thermal performance is required. Tubes, on the other hand, are more commonly associated with shell and tube heat exchangers. In the context of welded spiral heat exchangers, tubes may be used in hybrid designs where the benefits of both spiral and tubular configurations are desired. Tubes provide a robust pathway for fluid flow and are often used in applications involving high pressure and temperature. The material selection for these tubes is critical, as it must withstand the operational conditions while ensuring optimal heat transfer. Shells serve as the outer casing for the heat exchanger, housing the plates or tubes and providing structural support. In welded spiral heat exchangers, the shell is typically designed to accommodate the spiral configuration, ensuring that the fluids are directed through the spiral channels efficiently. The shell must be constructed from materials that can withstand the environmental conditions of the application, such as corrosion resistance in chemical processing or high-temperature tolerance in power generation. The integration of plates, tubes, and shells in welded spiral heat exchangers allows for a versatile and efficient heat transfer solution that can be tailored to meet the specific needs of various industries. The choice between using plates, tubes, or a combination thereof depends on factors such as the nature of the fluids being processed, the required thermal performance, and the physical constraints of the installation site. As the demand for energy-efficient and compact heat exchangers continues to rise, the innovation in the design and materials of plates, tubes, and shells will play a crucial role in advancing the capabilities of welded spiral heat exchangers.
Petrochemicals, Food & Beverages, Steel Making, Pharmaceutical, Wastewater Treatment, Pulp & Paper, Others in the Global Welded Spiral Heat Exchangers Market:
Welded spiral heat exchangers find extensive usage across a variety of industries due to their efficient heat transfer capabilities and compact design. In the petrochemical industry, these exchangers are essential for processes that involve high temperatures and pressures, such as the distillation of crude oil and the production of chemicals. Their ability to handle corrosive fluids and maintain thermal efficiency under extreme conditions makes them invaluable in this sector. In the food and beverages industry, welded spiral heat exchangers are used for pasteurization, sterilization, and other thermal processes that require precise temperature control. Their compact design allows for easy integration into existing production lines, while their efficient heat transfer capabilities ensure consistent product quality. In steel making, these exchangers are used to recover waste heat from exhaust gases, contributing to energy savings and reduced emissions. The pharmaceutical industry relies on welded spiral heat exchangers for processes such as fermentation and crystallization, where maintaining specific temperatures is crucial for product quality and efficacy. In wastewater treatment, these exchangers are used to recover heat from treated effluent, reducing energy consumption and operational costs. The pulp and paper industry utilizes welded spiral heat exchangers for processes such as bleaching and pulping, where efficient heat transfer is essential for maintaining production efficiency. Other industries, such as power generation and HVAC, also benefit from the use of these exchangers, as they provide reliable and efficient heat transfer solutions that contribute to overall system performance. The versatility and efficiency of welded spiral heat exchangers make them a preferred choice for industries seeking to optimize energy use and reduce operational costs. As the demand for sustainable and energy-efficient technologies continues to grow, the usage of welded spiral heat exchangers is expected to expand across various sectors, further solidifying their role as a critical component in modern industrial processes.
Global Welded Spiral Heat Exchangers Market Outlook:
The outlook for the Global Welded Spiral Heat Exchangers Market indicates a steady growth trajectory over the coming years. Starting from a valuation of approximately US$ 1261 million in 2024, the market is anticipated to reach around US$ 1445.3 million by 2030. This growth is projected to occur at a Compound Annual Growth Rate (CAGR) of 2.3% during the forecast period. This steady increase reflects the rising demand for energy-efficient and compact heat transfer solutions across various industries. The market's expansion is driven by the need for sustainable technologies that can help industries reduce energy consumption and operational costs. As industries continue to prioritize efficiency and sustainability, the demand for welded spiral heat exchangers is expected to grow. The market's growth is also supported by advancements in materials and design, which enhance the performance and durability of these exchangers. As a result, the Global Welded Spiral Heat Exchangers Market is poised to play a significant role in the industrial landscape, offering solutions that align with modern efficiency and sustainability goals. The projected growth underscores the importance of these exchangers in meeting the evolving needs of industries worldwide.
Report Metric | Details |
Report Name | Welded Spiral Heat Exchangers Market |
Accounted market size in 2024 | US$ 1261 million |
Forecasted market size in 2030 | US$ 1445.3 million |
CAGR | 2.3 |
Base Year | 2024 |
Forecasted years | 2025 - 2030 |
Segment by Type |
|
Segment by Application |
|
Production by Region |
|
Sales by Region |
|
By Company | Alfa Laval AB, Danfoss A/S, Gooch Thermal Systems, Inc., Nexson Group, Elanco, Inc., Kurose Chemical Equipment Co., Ltd., Shanghai Shenglin M&E Technology Co., Ltd., SmartHeat Inc., Shineheat Corp |
Forecast units | USD million in value |
Report coverage | Revenue and volume forecast, company share, competitive landscape, growth factors and trends |