What is Factory Automation System - Global Market?
Factory automation systems are revolutionizing the way industries operate by integrating advanced technologies to streamline production processes. These systems encompass a wide range of technologies, including robotics, control systems, and information technologies, to automate manufacturing tasks. The global market for factory automation systems is driven by the need for increased productivity, efficiency, and safety in manufacturing environments. By reducing human intervention, these systems minimize errors, enhance precision, and ensure consistent product quality. Moreover, they enable manufacturers to respond swiftly to market demands and reduce operational costs. As industries across the globe strive to remain competitive, the adoption of factory automation systems is becoming increasingly essential. This market is characterized by rapid technological advancements and innovations, which are continually expanding the capabilities and applications of automation systems. As a result, businesses are investing heavily in these systems to gain a competitive edge and meet the evolving needs of their customers. The global market for factory automation systems is poised for significant growth as more industries recognize the benefits of automation in enhancing their operational efficiency and overall productivity.
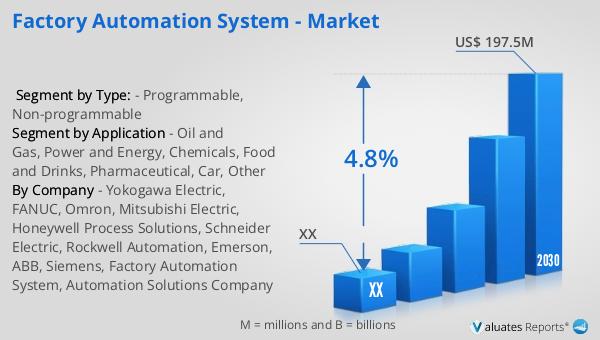
Programmable, Non-programmable in the Factory Automation System - Global Market:
In the realm of factory automation systems, programmable and non-programmable systems play crucial roles in enhancing manufacturing processes. Programmable automation systems are designed to be flexible and adaptable, allowing manufacturers to easily modify production processes to accommodate different products or changes in production volume. These systems are typically controlled by programmable logic controllers (PLCs) or computers, which can be reprogrammed to perform a variety of tasks. This flexibility makes programmable systems ideal for industries that require frequent changes in production, such as automotive manufacturing, where different models and variants are produced on the same assembly line. On the other hand, non-programmable automation systems are designed for repetitive tasks that do not require frequent changes. These systems are often used in industries where the production process is stable and consistent, such as in the production of consumer goods or food and beverages. Non-programmable systems are typically less expensive than their programmable counterparts, making them an attractive option for manufacturers looking to automate specific tasks without the need for frequent adjustments. Both programmable and non-programmable systems have their unique advantages and are chosen based on the specific needs and requirements of the manufacturing process. As technology continues to advance, the capabilities of both types of systems are expanding, offering manufacturers more options and greater flexibility in automating their production processes. The global market for factory automation systems is witnessing a growing demand for both programmable and non-programmable systems as industries seek to enhance their operational efficiency and remain competitive in an increasingly dynamic market. The choice between programmable and non-programmable systems often depends on factors such as the complexity of the production process, the need for flexibility, and the cost considerations. Programmable systems, with their ability to be easily reconfigured, are particularly beneficial for industries that experience frequent changes in production requirements. These systems allow manufacturers to quickly adapt to new product designs or changes in production volume, ensuring that they can meet customer demands without significant downtime or retooling costs. In contrast, non-programmable systems are well-suited for industries with stable production processes, where the focus is on achieving high levels of efficiency and consistency. These systems are often used in applications where the production tasks are repetitive and do not require frequent changes, such as in the packaging of consumer goods or the assembly of electronic components. The cost-effectiveness of non-programmable systems makes them an attractive option for manufacturers looking to automate specific tasks without the need for extensive customization or reprogramming. As the global market for factory automation systems continues to evolve, manufacturers are increasingly looking for solutions that offer the right balance of flexibility, efficiency, and cost-effectiveness. This has led to the development of hybrid systems that combine the benefits of both programmable and non-programmable systems, providing manufacturers with greater versatility and control over their production processes. These hybrid systems are designed to offer the flexibility of programmable systems while maintaining the cost advantages of non-programmable systems, making them an ideal choice for industries with diverse production needs. The growing demand for factory automation systems is also being driven by the increasing adoption of Industry 4.0 technologies, which emphasize the integration of digital technologies and data analytics into manufacturing processes. This trend is leading to the development of more advanced automation systems that can seamlessly integrate with other digital technologies, such as the Internet of Things (IoT), artificial intelligence (AI), and machine learning. These advanced systems offer manufacturers the ability to collect and analyze data in real-time, enabling them to make more informed decisions and optimize their production processes for greater efficiency and productivity. As the global market for factory automation systems continues to expand, manufacturers are increasingly recognizing the importance of investing in advanced automation solutions that can help them stay competitive in a rapidly changing market. The choice between programmable and non-programmable systems, as well as the adoption of hybrid solutions, will continue to play a critical role in shaping the future of factory automation and driving the growth of the global market.
Oil and Gas, Power and Energy, Chemicals, Food and Drinks, Pharmaceutical, Car, Other in the Factory Automation System - Global Market:
Factory automation systems are being increasingly utilized across various industries, including oil and gas, power and energy, chemicals, food and drinks, pharmaceuticals, automotive, and others, to enhance operational efficiency and productivity. In the oil and gas industry, automation systems are used to monitor and control complex processes, ensuring safety and efficiency in operations. These systems help in managing the extraction, refining, and distribution processes, reducing the risk of human error and enhancing overall productivity. In the power and energy sector, automation systems are employed to optimize the generation, transmission, and distribution of energy. They enable real-time monitoring and control of power plants, ensuring efficient energy production and minimizing downtime. In the chemical industry, automation systems are used to control chemical processes, ensuring precision and consistency in production. These systems help in maintaining the quality of chemical products and reducing waste, leading to cost savings and improved environmental sustainability. In the food and drinks industry, automation systems are used to streamline production processes, ensuring consistent product quality and safety. They help in managing the entire production process, from raw material handling to packaging, reducing the risk of contamination and ensuring compliance with food safety regulations. In the pharmaceutical industry, automation systems are used to enhance the precision and efficiency of drug manufacturing processes. They help in maintaining the quality and consistency of pharmaceutical products, ensuring compliance with stringent regulatory requirements. In the automotive industry, automation systems are used to enhance the efficiency and precision of manufacturing processes, enabling the production of high-quality vehicles at a lower cost. These systems help in managing the entire production process, from assembly to quality control, ensuring that vehicles meet the highest standards of quality and safety. In other industries, such as electronics and consumer goods, automation systems are used to enhance production efficiency and product quality. They help in managing complex production processes, ensuring consistency and precision in manufacturing. The global market for factory automation systems is witnessing significant growth as industries across the globe recognize the benefits of automation in enhancing operational efficiency and productivity. As technology continues to advance, the capabilities and applications of factory automation systems are expanding, offering industries more options and greater flexibility in automating their production processes. The adoption of factory automation systems is becoming increasingly essential for industries looking to remain competitive in an increasingly dynamic market. By investing in advanced automation solutions, industries can enhance their operational efficiency, reduce costs, and improve product quality, ensuring their long-term success in the global market.
Factory Automation System - Global Market Outlook:
The global market for factory automation systems was valued at approximately $142.3 million in 2023. This market is projected to grow significantly, reaching an estimated size of $197.5 million by 2030. This growth is expected to occur at a compound annual growth rate (CAGR) of 4.8% during the forecast period from 2024 to 2030. The increasing demand for automation solutions across various industries is a key driver of this market growth. As industries strive to enhance their operational efficiency and productivity, the adoption of factory automation systems is becoming increasingly essential. These systems offer numerous benefits, including improved precision, reduced human error, and enhanced product quality, making them an attractive investment for manufacturers. The market is characterized by rapid technological advancements and innovations, which are continually expanding the capabilities and applications of automation systems. As a result, businesses are investing heavily in these systems to gain a competitive edge and meet the evolving needs of their customers. The global market for factory automation systems is poised for significant growth as more industries recognize the benefits of automation in enhancing their operational efficiency and overall productivity. This growth is expected to be driven by the increasing adoption of Industry 4.0 technologies, which emphasize the integration of digital technologies and data analytics into manufacturing processes. As the market continues to evolve, manufacturers are increasingly recognizing the importance of investing in advanced automation solutions that can help them stay competitive in a rapidly changing market. The projected growth of the global market for factory automation systems reflects the increasing demand for automation solutions across various industries and the growing recognition of the benefits of automation in enhancing operational efficiency and productivity.
Report Metric | Details |
Report Name | Factory Automation System - Market |
Forecasted market size in 2030 | US$ 197.5 million |
CAGR | 4.8% |
Forecasted years | 2024 - 2030 |
Segment by Type: |
|
Segment by Application |
|
By Region |
|
By Company | Yokogawa Electric, FANUC, Omron, Mitsubishi Electric, Honeywell Process Solutions, Schneider Electric, Rockwell Automation, Emerson, ABB, Siemens, Factory Automation System, Automation Solutions Company |
Forecast units | USD million in value |
Report coverage | Revenue and volume forecast, company share, competitive landscape, growth factors and trends |