What is Global Residual Stress Measurement Market?
The Global Residual Stress Measurement Market is a specialized sector focused on the assessment of residual stresses within materials. Residual stress refers to the stress that remains in a material after it has been manufactured or processed. These stresses can significantly impact the performance, durability, and safety of materials and components used in various industries. The market for residual stress measurement encompasses a range of techniques and technologies designed to accurately measure these stresses. This includes methods such as X-ray diffraction, hole-drilling, and ultrasonic testing, among others. The primary goal is to ensure that materials meet the required specifications and performance standards, thereby preventing potential failures and extending the lifespan of components. The market serves a diverse array of industries, including aerospace, automotive, construction, and manufacturing, where the integrity and reliability of materials are of paramount importance. As industries continue to advance and demand higher performance from materials, the need for precise residual stress measurement is expected to grow, driving innovation and development within this market.
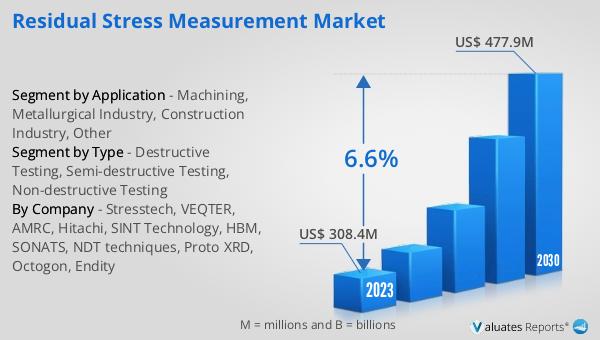
Destructive Testing, Semi-destructive Testing, Non-destructive Testing in the Global Residual Stress Measurement Market:
Destructive Testing, Semi-destructive Testing, and Non-destructive Testing are three primary methods used in the Global Residual Stress Measurement Market to evaluate the internal stresses within materials. Destructive Testing involves methods that permanently alter or destroy the sample being tested. One common technique is the sectioning method, where the material is cut into smaller pieces, and the resulting deformation is measured to determine the residual stress. This method provides highly accurate results but is limited by its invasive nature, making it unsuitable for finished products or critical components. Semi-destructive Testing, on the other hand, involves techniques that cause minimal damage to the material. The hole-drilling method is a popular semi-destructive technique where a small hole is drilled into the material, and the resulting deformation around the hole is measured to calculate the residual stress. This method strikes a balance between accuracy and preservation of the material's integrity, making it suitable for in-service components where some level of damage is acceptable. Non-destructive Testing (NDT) is the most preferred method in many industries due to its ability to assess residual stress without causing any damage to the material. Techniques such as X-ray diffraction (XRD) and ultrasonic testing fall under this category. XRD involves directing X-rays at the material and analyzing the diffraction patterns to determine the residual stress. This method is highly accurate and can be used on a wide range of materials, including metals and ceramics. Ultrasonic testing, on the other hand, uses high-frequency sound waves to detect internal stresses. The sound waves are transmitted through the material, and the reflected waves are analyzed to determine the stress distribution. NDT methods are particularly valuable in industries where maintaining the integrity of the material is crucial, such as aerospace and automotive sectors. Each of these testing methods has its own set of advantages and limitations, and the choice of method depends on factors such as the type of material, the required accuracy, and the specific application. As the demand for high-performance materials continues to rise, the Global Residual Stress Measurement Market is expected to see increased adoption of advanced testing techniques to ensure the reliability and safety of critical components.
Machining, Metallurgical Industry, Construction Industry, Other in the Global Residual Stress Measurement Market:
The Global Residual Stress Measurement Market finds extensive usage across various industries, including Machining, Metallurgical Industry, Construction Industry, and others. In the Machining sector, residual stress measurement is crucial for ensuring the precision and quality of machined components. Machining processes such as milling, turning, and grinding can introduce significant residual stresses into the material, which can affect the dimensional stability and performance of the final product. By accurately measuring and controlling these stresses, manufacturers can enhance the quality and reliability of machined parts, reduce the risk of failure, and extend the lifespan of components. In the Metallurgical Industry, residual stress measurement plays a vital role in the production and quality control of metals and alloys. Processes such as casting, forging, and welding can induce residual stresses that impact the mechanical properties and performance of the material. By employing residual stress measurement techniques, metallurgical engineers can optimize processing parameters, improve material properties, and ensure that the final products meet stringent quality standards. This is particularly important in industries such as aerospace and automotive, where the performance and safety of metal components are critical. The Construction Industry also benefits significantly from residual stress measurement. Construction materials such as concrete, steel, and composites are subjected to various stresses during manufacturing, transportation, and installation. Residual stress measurement helps in assessing the structural integrity and durability of these materials, ensuring that they can withstand the loads and environmental conditions they will encounter in service. This is essential for the safety and longevity of buildings, bridges, and other infrastructure projects. Additionally, residual stress measurement is used in other industries such as electronics, medical devices, and energy, where the performance and reliability of materials are of utmost importance. For instance, in the electronics industry, residual stress measurement is used to ensure the reliability of semiconductor devices and printed circuit boards. In the medical device industry, it helps in assessing the performance and safety of implants and surgical instruments. In the energy sector, residual stress measurement is used to evaluate the integrity of pipelines, pressure vessels, and other critical components. Overall, the Global Residual Stress Measurement Market plays a crucial role in ensuring the quality, performance, and safety of materials and components across a wide range of industries.
Global Residual Stress Measurement Market Outlook:
The global Residual Stress Measurement market was valued at US$ 308.4 million in 2023 and is anticipated to reach US$ 477.9 million by 2030, witnessing a CAGR of 6.6% during the forecast period 2024-2030. This market growth reflects the increasing demand for accurate and reliable residual stress measurement techniques across various industries. As industries continue to advance and require higher performance from materials, the need for precise residual stress measurement is expected to grow. The market encompasses a range of techniques and technologies designed to accurately measure residual stresses, including destructive, semi-destructive, and non-destructive testing methods. Each of these methods has its own set of advantages and limitations, and the choice of method depends on factors such as the type of material, the required accuracy, and the specific application. The market serves a diverse array of industries, including aerospace, automotive, construction, and manufacturing, where the integrity and reliability of materials are of paramount importance. As the demand for high-performance materials continues to rise, the Global Residual Stress Measurement Market is expected to see increased adoption of advanced testing techniques to ensure the reliability and safety of critical components.
Report Metric | Details |
Report Name | Residual Stress Measurement Market |
Accounted market size in 2023 | US$ 308.4 million |
Forecasted market size in 2030 | US$ 477.9 million |
CAGR | 6.6% |
Base Year | 2023 |
Forecasted years | 2024 - 2030 |
Segment by Type |
|
Segment by Application |
|
Production by Region |
|
Consumption by Region |
|
By Company | Stresstech, VEQTER, AMRC, Hitachi, SINT Technology, HBM, SONATS, NDT techniques, Proto XRD, Octogon, Endity |
Forecast units | USD million in value |
Report coverage | Revenue and volume forecast, company share, competitive landscape, growth factors and trends |