What is Isolators for Aseptic Processing - Global Market?
Isolators for aseptic processing are specialized containment systems designed to maintain a sterile environment for various applications, primarily in the pharmaceutical and biotechnology industries. These isolators are crucial for ensuring that products are manufactured in a contamination-free environment, which is essential for maintaining product safety and efficacy. The global market for these isolators is driven by the increasing demand for sterile manufacturing processes, stringent regulatory requirements, and the growing focus on patient safety. Isolators provide a controlled environment that prevents the entry of contaminants, thereby reducing the risk of product contamination. They are used in various stages of drug development and manufacturing, including formulation, filling, and packaging. The market is characterized by technological advancements, such as the integration of automation and robotics, which enhance the efficiency and reliability of aseptic processing. Additionally, the rising prevalence of chronic diseases and the increasing demand for biologics and biosimilars are expected to drive the growth of the isolators for aseptic processing market. As the pharmaceutical industry continues to evolve, the need for advanced containment solutions like isolators will remain critical to ensuring the safety and quality of pharmaceutical products.
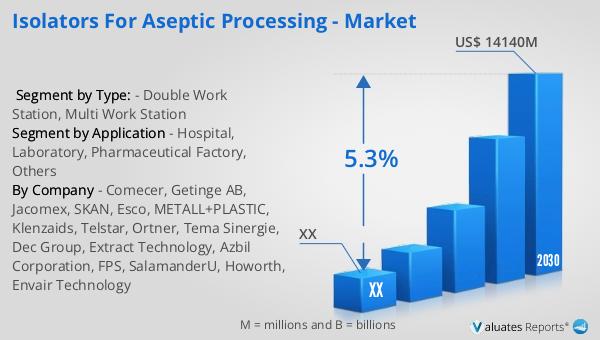
Double Work Station, Multi Work Station in the Isolators for Aseptic Processing - Global Market:
Double work station and multi work station isolators are integral components of the isolators for aseptic processing market, each serving distinct purposes based on the scale and complexity of operations. Double work station isolators are designed to accommodate two operators simultaneously, allowing for increased productivity and efficiency in aseptic processing tasks. These isolators are particularly beneficial in environments where space is limited, yet the demand for high throughput is essential. They enable operators to perform tasks such as filling, capping, and inspection in a sterile environment, minimizing the risk of contamination. The ergonomic design of double work station isolators ensures that operators can work comfortably and efficiently, reducing fatigue and the potential for errors. On the other hand, multi work station isolators are designed to accommodate multiple operators and processes simultaneously, making them ideal for large-scale manufacturing operations. These isolators are equipped with advanced features such as integrated automation systems, which enhance the precision and consistency of aseptic processing tasks. Multi work station isolators are often used in pharmaceutical manufacturing facilities where complex processes require the coordination of multiple operators and equipment. They provide a flexible and scalable solution for aseptic processing, allowing manufacturers to adapt to changing production demands. The use of multi work station isolators can significantly reduce the risk of cross-contamination, as each work station is isolated from the others, ensuring that different processes do not interfere with one another. Both double and multi work station isolators are designed with safety and compliance in mind, adhering to stringent regulatory standards to ensure the highest levels of product quality and safety. The choice between double and multi work station isolators depends on various factors, including the scale of operations, the complexity of processes, and the specific requirements of the manufacturing environment. As the demand for sterile manufacturing processes continues to grow, the adoption of double and multi work station isolators is expected to increase, driven by the need for efficient and reliable containment solutions. These isolators play a crucial role in ensuring the safety and efficacy of pharmaceutical products, making them an essential component of modern aseptic processing facilities.
Hospital, Laboratory, Pharmaceutical Factory, Others in the Isolators for Aseptic Processing - Global Market:
Isolators for aseptic processing are utilized in various settings, including hospitals, laboratories, pharmaceutical factories, and other environments where maintaining a sterile environment is critical. In hospitals, isolators are used to prepare sterile medications, such as intravenous drugs and chemotherapy agents, ensuring that they are free from contaminants before administration to patients. This is particularly important in oncology departments, where the preparation of cytotoxic drugs requires a high level of sterility to protect both patients and healthcare workers. In laboratories, isolators are used for research and development activities, including the handling of hazardous materials and the cultivation of cell cultures. They provide a controlled environment that prevents contamination and ensures the integrity of experimental results. Laboratory isolators are often equipped with advanced features such as HEPA filtration and automated decontamination systems, which enhance their effectiveness in maintaining sterility. In pharmaceutical factories, isolators are used throughout the drug manufacturing process, from formulation to packaging. They play a crucial role in ensuring that products are manufactured in compliance with regulatory standards, reducing the risk of contamination and ensuring product safety. Pharmaceutical isolators are designed to accommodate a wide range of processes, including filling, capping, and inspection, providing a versatile solution for aseptic processing. In addition to hospitals, laboratories, and pharmaceutical factories, isolators are also used in other industries where maintaining a sterile environment is essential. For example, in the food and beverage industry, isolators are used to ensure the sterility of products such as dairy and infant formula, preventing contamination and ensuring product safety. Similarly, in the cosmetics industry, isolators are used to manufacture sterile products such as creams and lotions, ensuring that they are free from harmful microorganisms. The versatility and effectiveness of isolators for aseptic processing make them an essential tool in a wide range of industries, providing a reliable solution for maintaining sterility and ensuring product quality.
Isolators for Aseptic Processing - Global Market Outlook:
The global market for isolators used in aseptic processing was valued at approximately $10,220 million in 2023. This market is projected to grow significantly, reaching an estimated value of $14,140 million by the year 2030. This growth represents a compound annual growth rate (CAGR) of 5.3% over the forecast period from 2024 to 2030. The increasing demand for sterile manufacturing processes, driven by the growing focus on patient safety and stringent regulatory requirements, is a key factor contributing to this market expansion. As pharmaceutical companies continue to innovate and develop new products, the need for advanced containment solutions like isolators becomes increasingly important. These isolators play a crucial role in ensuring the safety and efficacy of pharmaceutical products by providing a controlled environment that prevents contamination. The market is also influenced by technological advancements, such as the integration of automation and robotics, which enhance the efficiency and reliability of aseptic processing. As the global healthcare landscape continues to evolve, the demand for isolators for aseptic processing is expected to grow, driven by the need for safe and effective pharmaceutical products. This market outlook highlights the significant opportunities for growth and innovation in the isolators for aseptic processing market, as companies strive to meet the increasing demand for sterile manufacturing solutions.
Report Metric | Details |
Report Name | Isolators for Aseptic Processing - Market |
Forecasted market size in 2030 | US$ 14140 million |
CAGR | 5.3% |
Forecasted years | 2024 - 2030 |
Segment by Type: |
|
Segment by Application |
|
By Region |
|
By Company | Comecer, Getinge AB, Jacomex, SKAN, Esco, METALL+PLASTIC, Klenzaids, Telstar, Ortner, Tema Sinergie, Dec Group, Extract Technology, Azbil Corporation, FPS, SalamanderU, Howorth, Envair Technology |
Forecast units | USD million in value |
Report coverage | Revenue and volume forecast, company share, competitive landscape, growth factors and trends |