What is Global Orbital Welding for the Semiconductor Market?
Global Orbital Welding for the Semiconductor Market is a specialized welding technique used to join pipes and tubes in the semiconductor industry. This method involves the use of a mechanized system that rotates the welding arc around a stationary workpiece, ensuring a high degree of precision and consistency. The semiconductor industry demands extremely high levels of cleanliness and precision, as even the smallest impurities can affect the performance of semiconductor devices. Orbital welding meets these stringent requirements by providing a clean, controlled environment that minimizes contamination. This technique is particularly useful for welding materials like stainless steel and other high-purity metals, which are commonly used in semiconductor manufacturing. The process is automated, reducing the risk of human error and ensuring uniform welds. This is crucial for maintaining the integrity of the semiconductor devices, which are often used in critical applications such as computers, smartphones, and medical equipment. Overall, Global Orbital Welding is an essential technology for the semiconductor market, enabling the production of high-quality, reliable semiconductor devices.
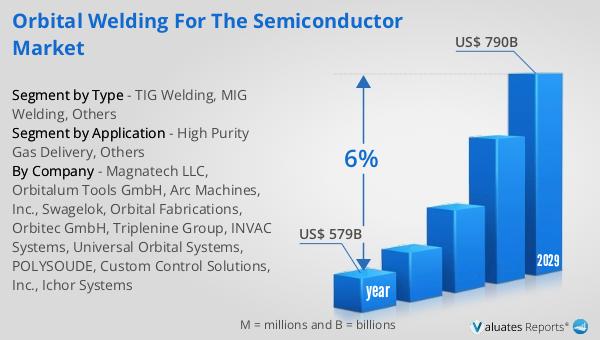
TIG Welding, MIG Welding, Others in the Global Orbital Welding for the Semiconductor Market:
TIG Welding, MIG Welding, and other welding techniques play significant roles in the Global Orbital Welding for the Semiconductor Market. TIG (Tungsten Inert Gas) Welding is known for its precision and control, making it ideal for applications requiring high-quality welds. In TIG welding, a tungsten electrode is used to produce the weld, and an inert gas, usually argon, is used to shield the weld area from contamination. This method is particularly effective for welding thin materials and is commonly used in the semiconductor industry for its ability to produce clean, precise welds. On the other hand, MIG (Metal Inert Gas) Welding is a faster process that uses a continuous wire feed as an electrode and an inert gas to protect the weld pool. While MIG welding is generally less precise than TIG welding, it is more efficient for larger-scale projects and thicker materials. In the context of the semiconductor market, MIG welding can be used for constructing larger components that do not require the same level of precision as smaller, more intricate parts. Other welding techniques, such as laser welding and electron beam welding, also have their place in the semiconductor industry. Laser welding uses a focused beam of light to melt the materials being joined, offering high precision and minimal heat-affected zones. This is particularly useful for delicate components that could be damaged by excessive heat. Electron beam welding, on the other hand, uses a beam of high-velocity electrons to join materials. This method is highly efficient and can produce deep welds with minimal distortion, making it suitable for thick materials and complex geometries. Each of these welding techniques has its own set of advantages and limitations, and the choice of method often depends on the specific requirements of the application. For instance, TIG welding might be chosen for its precision in creating high-purity gas delivery systems, while MIG welding could be used for constructing larger structural components. Laser and electron beam welding might be selected for their ability to produce high-quality welds with minimal thermal distortion. The semiconductor industry often requires a combination of these techniques to meet its diverse needs. The integration of these various welding methods into the orbital welding process further enhances the capabilities of the semiconductor manufacturing sector. By leveraging the strengths of each technique, manufacturers can produce high-quality, reliable components that meet the stringent demands of the semiconductor market. Overall, the use of TIG, MIG, and other welding techniques in Global Orbital Welding for the Semiconductor Market is essential for maintaining the high standards of quality and precision required in this industry.
High Purity Gas Delivery, Others in the Global Orbital Welding for the Semiconductor Market:
The usage of Global Orbital Welding for the Semiconductor Market is particularly prominent in areas such as High Purity Gas Delivery and other critical applications. High Purity Gas Delivery systems are essential in the semiconductor industry, as they ensure the supply of ultra-clean gases required for various manufacturing processes. These gases are used in processes like chemical vapor deposition, etching, and doping, all of which are crucial for creating semiconductor devices. Orbital welding is ideal for constructing these gas delivery systems because it provides a high level of precision and cleanliness. The automated nature of orbital welding ensures that each weld is consistent and free from contaminants, which is vital for maintaining the purity of the gases being delivered. This is especially important in the semiconductor industry, where even the smallest impurities can lead to defects in the final product. In addition to High Purity Gas Delivery, orbital welding is used in other critical applications within the semiconductor market. For example, it is employed in the construction of vacuum systems, which are used to create the controlled environments necessary for semiconductor manufacturing. These systems require airtight seals to maintain the vacuum, and orbital welding provides the precision needed to achieve these seals. Another application is in the fabrication of process piping, which transports various chemicals and gases used in semiconductor manufacturing. The high level of precision offered by orbital welding ensures that these pipes are free from leaks and contamination, which is crucial for maintaining the integrity of the manufacturing process. Furthermore, orbital welding is used in the assembly of cleanroom equipment, which is essential for maintaining the controlled environments required for semiconductor production. Cleanrooms must be free from contaminants, and the precision of orbital welding helps to ensure that the equipment used in these environments meets the necessary standards. Overall, the usage of Global Orbital Welding in the semiconductor market is vital for maintaining the high levels of precision and cleanliness required in this industry. Whether it is in High Purity Gas Delivery systems, vacuum systems, process piping, or cleanroom equipment, orbital welding provides the reliability and consistency needed to produce high-quality semiconductor devices.
Global Orbital Welding for the Semiconductor Market Outlook:
The global market for semiconductors was valued at approximately US$ 579 billion in 2022 and is anticipated to reach around US$ 790 billion by 2029, growing at a compound annual growth rate (CAGR) of 6% during the forecast period. This significant growth underscores the increasing demand for semiconductor devices across various industries, including consumer electronics, automotive, telecommunications, and healthcare. The semiconductor market is driven by advancements in technology, such as the development of smaller, more efficient chips and the growing adoption of artificial intelligence and the Internet of Things (IoT). These advancements are fueling the need for high-quality, reliable semiconductor devices, which in turn drives the demand for precision manufacturing techniques like Global Orbital Welding. As the semiconductor industry continues to evolve, the importance of maintaining high standards of quality and precision in manufacturing processes becomes even more critical. This is where Global Orbital Welding plays a crucial role, ensuring that the components used in semiconductor devices meet the stringent requirements of the industry. The projected growth of the semiconductor market highlights the need for continued innovation and investment in advanced manufacturing technologies, including orbital welding, to support the production of next-generation semiconductor devices.
Report Metric | Details |
Report Name | Orbital Welding for the Semiconductor Market |
Accounted market size in year | US$ 579 billion |
Forecasted market size in 2029 | US$ 790 billion |
CAGR | 6% |
Base Year | year |
Forecasted years | 2024 - 2029 |
Segment by Type |
|
Segment by Application |
|
By Region |
|
By Company | Magnatech LLC, Orbitalum Tools GmbH, Arc Machines, Inc., Swagelok, Orbital Fabrications, Orbitec GmbH, Triplenine Group, INVAC Systems, Universal Orbital Systems, POLYSOUDE, Custom Control Solutions, Inc., Ichor Systems |
Forecast units | USD million in value |
Report coverage | Revenue and volume forecast, company share, competitive landscape, growth factors and trends |