What is Global Low-pressure Injection Ceramic Market?
The Global Low-pressure Injection Ceramic Market is a specialized segment within the broader ceramics industry, focusing on the production of high-precision ceramic components through low-pressure injection molding techniques. This market is driven by the demand for complex, high-performance ceramic parts that are difficult to manufacture using traditional methods. Low-pressure injection molding allows for the creation of intricate shapes and fine details, making it ideal for applications requiring high dimensional accuracy and superior mechanical properties. The process involves injecting a ceramic slurry into a mold at low pressure, which reduces the risk of defects and ensures uniformity in the final product. This technique is particularly beneficial for producing components used in high-stress environments, such as aerospace, medical, and electronic industries. The market is characterized by continuous innovation and advancements in material science, which are expanding the range of applications for low-pressure injection ceramics. As industries increasingly seek materials that offer high strength, thermal stability, and resistance to wear and corrosion, the demand for low-pressure injection ceramic components is expected to grow.
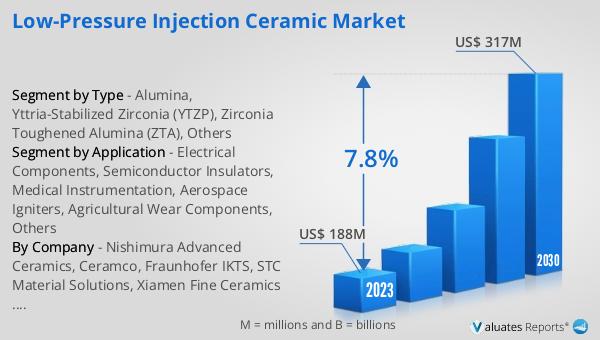
Alumina, Yttria-Stabilized Zirconia (YTZP), Zirconia Toughened Alumina (ZTA), Others in the Global Low-pressure Injection Ceramic Market:
Alumina, Yttria-Stabilized Zirconia (YTZP), Zirconia Toughened Alumina (ZTA), and other materials play crucial roles in the Global Low-pressure Injection Ceramic Market. Alumina, or aluminum oxide, is one of the most widely used ceramic materials due to its excellent mechanical properties, high thermal conductivity, and resistance to wear and corrosion. It is commonly used in applications that require high strength and durability, such as cutting tools, wear-resistant components, and electrical insulators. Yttria-Stabilized Zirconia (YTZP) is another important material in this market. It is known for its exceptional toughness, high fracture resistance, and thermal stability, making it ideal for applications in the medical field, such as dental implants and prosthetics, as well as in the aerospace industry for components that must withstand extreme conditions. Zirconia Toughened Alumina (ZTA) combines the best properties of both alumina and zirconia, offering enhanced toughness and strength. This material is often used in applications where both high mechanical performance and resistance to thermal shock are required, such as in cutting tools and wear-resistant parts. Other materials used in the low-pressure injection ceramic market include silicon carbide, silicon nitride, and various composite materials. These materials are selected based on their specific properties and the requirements of the application. Silicon carbide, for example, is known for its high hardness and thermal conductivity, making it suitable for high-temperature applications and abrasive environments. Silicon nitride offers excellent thermal shock resistance and mechanical strength, making it ideal for use in engine components and cutting tools. Composite materials, which combine different ceramic phases, are designed to offer a balance of properties tailored to specific applications. The choice of material in the low-pressure injection ceramic market is critical, as it directly impacts the performance, durability, and reliability of the final product. Manufacturers continuously research and develop new materials and formulations to meet the evolving demands of various industries. The ability to produce complex shapes and fine details with low-pressure injection molding further enhances the versatility and applicability of these advanced ceramic materials. As a result, the Global Low-pressure Injection Ceramic Market is poised for growth, driven by the increasing demand for high-performance materials in a wide range of applications.
Electrical Components, Semiconductor Insulators, Medical Instrumentation, Aerospace Igniters, Agricultural Wear Components, Others in the Global Low-pressure Injection Ceramic Market:
The Global Low-pressure Injection Ceramic Market finds extensive usage across various industries, including electrical components, semiconductor insulators, medical instrumentation, aerospace igniters, agricultural wear components, and others. In the field of electrical components, low-pressure injection ceramics are used to manufacture insulators, substrates, and other critical parts that require high dielectric strength, thermal stability, and resistance to electrical and thermal shocks. These properties make ceramics ideal for use in high-voltage and high-frequency applications, ensuring reliable performance and longevity. In the semiconductor industry, low-pressure injection ceramics are used to produce insulators and other components that must withstand high temperatures and corrosive environments. The precision and uniformity offered by low-pressure injection molding are essential for maintaining the performance and reliability of semiconductor devices. Medical instrumentation is another key area where low-pressure injection ceramics are widely used. The biocompatibility, strength, and wear resistance of ceramics make them suitable for a range of medical applications, including dental implants, prosthetics, and surgical instruments. The ability to produce complex shapes and fine details with low-pressure injection molding allows for the creation of customized medical components that meet the specific needs of patients and healthcare providers. In the aerospace industry, low-pressure injection ceramics are used to manufacture igniters, sensors, and other components that must operate under extreme conditions. The high thermal stability, mechanical strength, and resistance to wear and corrosion of ceramics make them ideal for use in aerospace applications, where reliability and performance are critical. Agricultural wear components, such as nozzles, bearings, and cutting tools, also benefit from the properties of low-pressure injection ceramics. The high hardness, wear resistance, and chemical stability of ceramics ensure long-lasting performance in harsh agricultural environments. Other applications of low-pressure injection ceramics include automotive components, industrial machinery, and consumer electronics. The versatility and performance of ceramics make them suitable for a wide range of uses, from engine parts and cutting tools to electronic substrates and protective coatings. The ability to produce complex shapes and fine details with low-pressure injection molding further enhances the applicability of ceramics in these diverse industries. As a result, the Global Low-pressure Injection Ceramic Market continues to expand, driven by the increasing demand for high-performance materials that offer superior mechanical, thermal, and electrical properties.
Global Low-pressure Injection Ceramic Market Outlook:
The global Low-pressure Injection Ceramic market was valued at US$ 188 million in 2023 and is anticipated to reach US$ 317 million by 2030, witnessing a CAGR of 7.8% during the forecast period 2024-2030. This significant growth reflects the increasing demand for high-performance ceramic components across various industries. The market's expansion is driven by the unique advantages of low-pressure injection molding, which allows for the production of complex shapes and fine details with high precision and uniformity. These properties are particularly valuable in applications that require high mechanical strength, thermal stability, and resistance to wear and corrosion. As industries such as aerospace, medical, electronics, and automotive continue to seek advanced materials that can meet their stringent performance requirements, the demand for low-pressure injection ceramics is expected to rise. The market's growth is also supported by ongoing advancements in material science and manufacturing technologies, which are expanding the range of applications for low-pressure injection ceramics. As a result, the Global Low-pressure Injection Ceramic Market is poised for significant growth in the coming years, driven by the increasing adoption of these advanced materials in a wide range of high-performance applications.
Report Metric | Details |
Report Name | Low-pressure Injection Ceramic Market |
Accounted market size in 2023 | US$ 188 million |
Forecasted market size in 2030 | US$ 317 million |
CAGR | 7.8% |
Base Year | 2023 |
Forecasted years | 2024 - 2030 |
Segment by Type |
|
Segment by Application |
|
Production by Region |
|
Consumption by Region |
|
By Company | Nishimura Advanced Ceramics, Ceramco, Fraunhofer IKTS, STC Material Solutions, Xiamen Fine Ceramics Technology |
Forecast units | USD million in value |
Report coverage | Revenue and volume forecast, company share, competitive landscape, growth factors and trends |