What is Global Ceramic Coatings for Semiconductor Equipment Market?
The Global Ceramic Coatings for Semiconductor Equipment Market is a specialized segment within the broader semiconductor industry, focusing on the application of ceramic coatings to semiconductor manufacturing equipment. These coatings are crucial for enhancing the performance and longevity of equipment used in the production of semiconductors. Ceramic coatings provide a protective layer that can withstand high temperatures, corrosive environments, and mechanical wear, which are common in semiconductor manufacturing processes. This market is driven by the increasing demand for semiconductors across various industries, including electronics, automotive, and telecommunications. As technology advances, the need for more efficient and durable manufacturing equipment grows, leading to a higher demand for ceramic coatings. These coatings help in reducing maintenance costs and downtime, thereby improving the overall efficiency of semiconductor production. The market is characterized by continuous innovation, with companies investing in research and development to create advanced coatings that meet the evolving needs of the semiconductor industry. The growth of this market is also supported by the expansion of semiconductor manufacturing facilities worldwide, particularly in regions like Asia-Pacific, which is a major hub for semiconductor production.
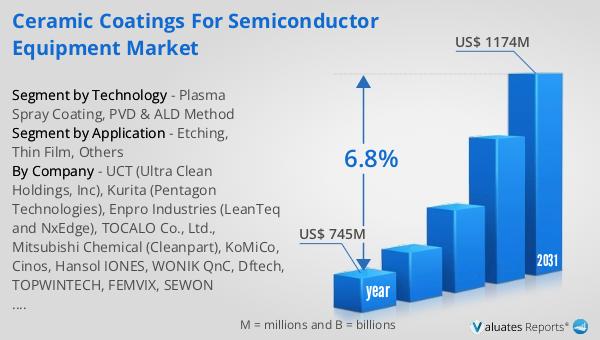
in the Global Ceramic Coatings for Semiconductor Equipment Market:
In the Global Ceramic Coatings for Semiconductor Equipment Market, various types of ceramic coatings are utilized by different customers based on their specific needs and applications. One of the most common types is alumina coatings, known for their excellent thermal stability and resistance to wear and corrosion. These coatings are widely used in semiconductor equipment that operates under high-temperature conditions, providing a protective barrier that extends the equipment's lifespan. Another popular type is yttria-stabilized zirconia (YSZ) coatings, which offer superior thermal insulation and are often used in environments where thermal shock resistance is critical. YSZ coatings are particularly beneficial in processes that involve rapid temperature changes, as they help prevent damage to the equipment. Silicon carbide coatings are also prevalent in the market, valued for their high hardness and chemical resistance. These coatings are ideal for equipment exposed to harsh chemical environments, as they provide a robust protective layer that minimizes the risk of corrosion and degradation. Additionally, titanium nitride coatings are used for their excellent wear resistance and low friction properties, making them suitable for components that experience significant mechanical stress. Customers in the semiconductor industry choose these coatings based on factors such as the specific manufacturing process, the operating environment, and the desired performance characteristics. For instance, in processes that involve aggressive chemicals, such as etching, silicon carbide coatings are preferred due to their chemical inertness. On the other hand, in applications where thermal management is crucial, such as thin film deposition, YSZ coatings are favored for their thermal insulation properties. The choice of coating also depends on the equipment's design and the materials used in its construction, as compatibility between the coating and the substrate is essential for optimal performance. Furthermore, the selection of ceramic coatings is influenced by the cost considerations and the expected return on investment. While advanced coatings may offer superior performance, they also come with a higher price tag, prompting customers to weigh the benefits against the costs. In some cases, customers may opt for a combination of different coatings to achieve the desired balance of performance and cost-effectiveness. The market is also seeing a trend towards the development of multifunctional coatings that combine the benefits of different materials, offering enhanced protection and performance in a single layer. This innovation is driven by the need to address the complex challenges faced by semiconductor manufacturers, such as increasing production efficiency and reducing downtime. As the semiconductor industry continues to evolve, the demand for specialized ceramic coatings is expected to grow, with customers seeking solutions that meet their specific requirements and contribute to the overall success of their manufacturing operations.
Etching, Thin Film, Others in the Global Ceramic Coatings for Semiconductor Equipment Market:
The usage of Global Ceramic Coatings for Semiconductor Equipment Market in areas such as etching, thin film, and others is pivotal to the efficiency and effectiveness of semiconductor manufacturing processes. In the etching process, ceramic coatings play a crucial role in protecting equipment from the aggressive chemicals used to remove material from the semiconductor wafer. These coatings provide a barrier that prevents corrosion and degradation, ensuring the longevity and reliability of the equipment. Silicon carbide coatings are particularly favored in etching applications due to their excellent chemical resistance and durability. By minimizing the wear and tear on equipment, these coatings help reduce maintenance costs and downtime, contributing to increased productivity and cost savings for manufacturers. In the thin film deposition process, ceramic coatings are essential for managing thermal conditions and ensuring uniform film growth. Yttria-stabilized zirconia (YSZ) coatings are commonly used in this area for their superior thermal insulation properties, which help maintain the optimal temperature conditions required for thin film deposition. These coatings also provide a smooth surface that facilitates the even distribution of thin films, resulting in high-quality semiconductor devices. The use of ceramic coatings in thin film applications enhances the precision and consistency of the manufacturing process, leading to improved device performance and yield. Beyond etching and thin film, ceramic coatings are also used in other semiconductor manufacturing processes, such as chemical vapor deposition (CVD) and physical vapor deposition (PVD). In these processes, the coatings protect equipment from the high temperatures and reactive gases involved, ensuring stable and reliable operation. Alumina coatings are often used in CVD and PVD applications for their excellent thermal stability and resistance to wear and corrosion. These coatings help maintain the integrity of the equipment, reducing the risk of contamination and defects in the semiconductor devices. The versatility and effectiveness of ceramic coatings make them an indispensable component of semiconductor manufacturing, enabling manufacturers to meet the demands of a rapidly evolving industry. As technology advances and the complexity of semiconductor devices increases, the need for specialized coatings that can withstand the rigors of modern manufacturing processes will continue to grow. Manufacturers are increasingly looking for coatings that offer a combination of properties, such as thermal stability, chemical resistance, and mechanical strength, to address the diverse challenges they face. The development of new and innovative ceramic coatings is expected to play a key role in the future of semiconductor manufacturing, providing the solutions needed to achieve higher levels of efficiency, quality, and performance.
Global Ceramic Coatings for Semiconductor Equipment Market Outlook:
The global market for ceramic coatings used in semiconductor equipment was valued at $745 million in 2024, with projections indicating it will grow to a revised size of $1,174 million by 2031, reflecting a compound annual growth rate (CAGR) of 6.8% over the forecast period. Meanwhile, the broader semiconductor market was estimated at $526.8 billion in 2023 and is expected to reach $780.7 billion by 2030. Our research suggests that the global semiconductor manufacturing wafer fabrication market is anticipated to expand from $251.7 billion in 2023 to $506.5 billion by 2030, achieving a remarkable CAGR of 40.49% during the forecast period. These figures underscore the significant growth potential within the semiconductor industry, driven by increasing demand for advanced electronic devices and the continuous evolution of technology. The expansion of the ceramic coatings market is closely linked to the broader trends in semiconductor manufacturing, as these coatings are essential for enhancing the performance and durability of equipment used in the production of semiconductors. As the industry continues to innovate and develop new technologies, the demand for high-quality ceramic coatings is expected to rise, supporting the growth of the market and contributing to the overall advancement of semiconductor manufacturing.
Report Metric | Details |
Report Name | Ceramic Coatings for Semiconductor Equipment Market |
Accounted market size in year | US$ 745 million |
Forecasted market size in 2031 | US$ 1174 million |
CAGR | 6.8% |
Base Year | year |
Forecasted years | 2025 - 2031 |
Segment by Technology |
|
Segment by Application |
|
By Region |
|
By Company | UCT (Ultra Clean Holdings, Inc), Kurita (Pentagon Technologies), Enpro Industries (LeanTeq and NxEdge), TOCALO Co., Ltd., Mitsubishi Chemical (Cleanpart), KoMiCo, Cinos, Hansol IONES, WONIK QnC, Dftech, TOPWINTECH, FEMVIX, SEWON HARDFACING CO.,LTD, Frontken Corporation Berhad, KERTZ HIGH TECH, Hung Jie Technology Corporation, Oerlikon Balzers, Beneq, APS Materials, Inc., SilcoTek, Alumiplate, ASSET Solutions, Inc., Persys Group, Entegris, Inficon, Value Engineering Co., Ltd, HTCSolar, Jiangsu Kaiweitesi Semiconductor Technology Co., Ltd., HCUT Co., Ltd, Ferrotec (Anhui) Technology Development Co., Ltd, Shanghai Companion, Chongqing Genori Technology Co., Ltd, GRAND HITEK |
Forecast units | USD million in value |
Report coverage | Revenue and volume forecast, company share, competitive landscape, growth factors and trends |